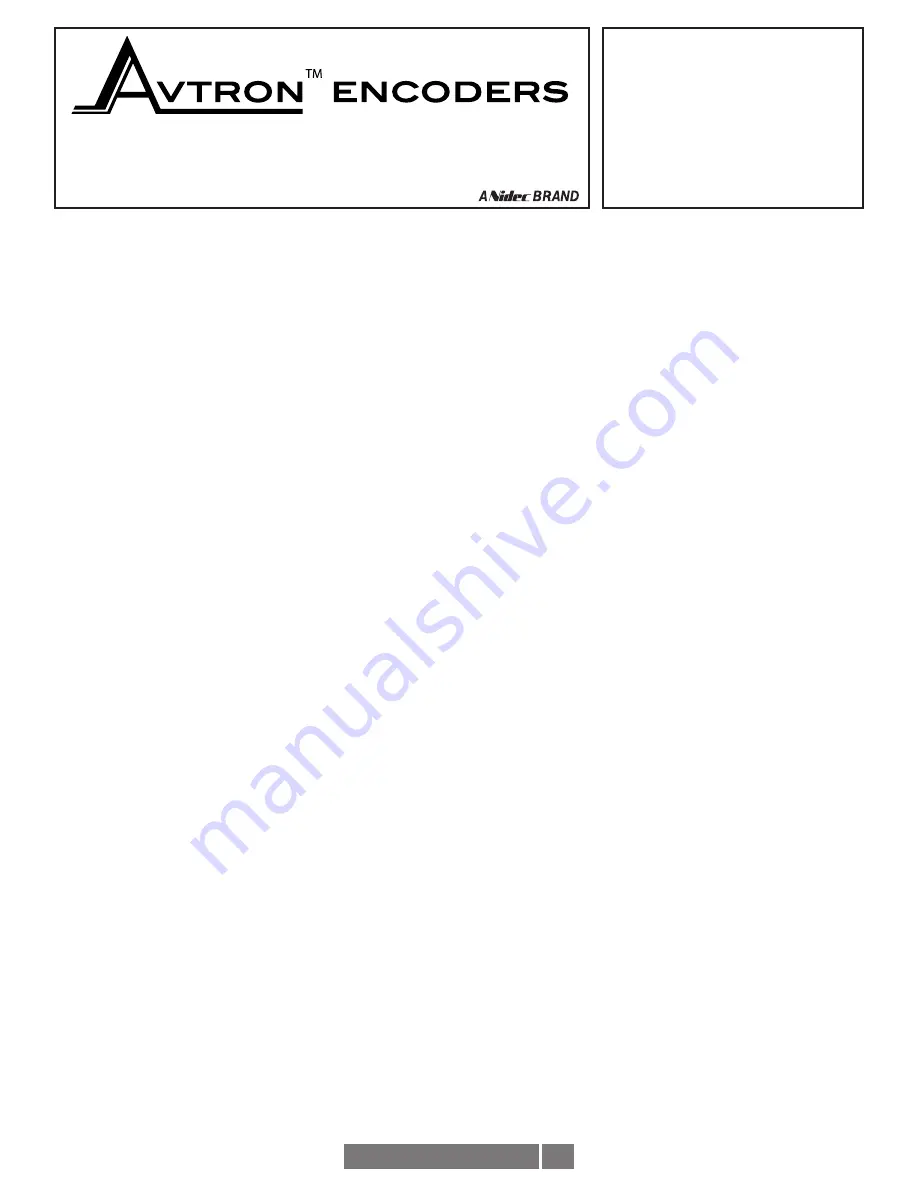
M6C-4, M6C-5
1
A40346
2 4 3 Tu x e d o A v e n u e , C l e v e l a n d , O h i o 4 4 1 3 1
T E L : + 1 2 1 6 - 6 4 2 - 1 2 3 0 - E - M A I L : e n c o d e r h e l p d e s k @ n i d e c - i n d u s t r i a l . c o m
W E B : w w w. a v t r o n e n c o d e r s . c o m
ATEX / IECEx Encoder
Instructions
M6C-4, M6C-5
EXPLOSION PROTECTED
HOLLOW SHAFT
DESCRIPTION
The Avtron Model M6C-4 and M6C-5 are Hollow Shaft Incremental
Encoders (also known as tachometers or pulse generators). This model
utilizes flameproof and increased safety construction for suitability in
hazardous locations. The M6C is certified for use in CAT 2 (Zone 1) Gas
Group IIB potentially explosive atmospheres with ambient temperature
range of -20°C to +80°C. A low temperature option with ambient
temperature range of -40°C to +80°C is available by specifying
Modification Codes 001 or 005. Marking codes are shown below.
Compliance with Essential Health and Safety Requirements of
60079-0, 60079-1, and 60079-7 is assured per the approvals listed
below.
Marking (standard):
II 2 G Ex de IIB T4 Gb (Tamb -20°C to +80°C)
Marking (low temperature):
II 2 G Ex de IIB T4 Gb (Tamb -40°C to +80°C)
Approvals:
ATEX per Certificate No. TRAC14ATEX0007X
IECEx per Certificate No. IECEx TRC 14.0005X
When mounted to a motor or machine, the M6C output is directly
proportional to shaft position (pulse count) or speed (pulse rate). The
M6C can be used for both control and instrumentation applications.
Hollow shaft encoders eliminate shaft couplings, adapter flanges,
or accessory mounting faces. The M6C employs a hollow shaft and
clamping collar to lock the encoder to the shaft. An anti-rotation
bracket prevents rotation of the encoder while allowing for shaft end
float.
The enclosures on all Model M6Cs are rated IP 66 to protect the
internal components from the entry of dust and water. Additionally, the
M6C uses magnetoresistive sensing technology, making the M6C ideal
for demanding industrial environments.
All M6Cs can be equipped with one or two outputs. Each output is
electrically independent and totally isolated.
The outputs can be wired as single ended single phase, single
ended two phase (A,B), or differential (A Quad B). Output resolution is
determined by the rotor’s base PPR (pulses per revolution), times a
sensor multiplier. The sensor module can provide: 1/2 the base PPR,
the base PPR, or double the base PPR (see table). With two outputs, the
same encoder can provide two different PPRs from a given rotor at the
same time. Only one rotor per encoder is possible.
Example: an M6C could use a 1024 PPR sensor output on one side for
feedback to a drive system, and simultaneously use a 256 PPR sensor
on the other side for a process computer.
INSTALLATION CONSIDERATIONS
The M6C standard flexible anti-rotation bracket will tolerate ± 0.1” of
shaft end float. Consideration should be taken when positioning the
encoder.
CAUTION
Be careful not to damage clamping fingers during handling.
Do not tighten clamping collar before installation onto
motor shaft. Damaging clamping fingers can affect the quality
of installation.
M6C ENVIRONMENT
The M6C does not produce flammable gasses or dusts in normal
operating modes. The M6C does not cause injury or harm when used
in conjunction with the installation guide. The M6C does not produce
ignition capable electrical sparks or arcs and has been designed not
to produce potential ignition sources from electromagnetic, acoustic,
optical or other energy sources. The M6C is not considered as a safety
device and is not suitable for connection into a safety system.
The installer should refer to the latest edition of the following standards
before installing or operating in a Hazardous Area:
EN 1127-1 Explosive Atmospheres - Explosion prevention and
protection, basic concepts, and methodology.
EN 60079-14 Electrical apparatus for explosive gas at mo spheres -
Part 14: Electrical installations in hazardous areas (other than mines).
The M6C housing and shaft materials are listed in the spe cifications.
These materials are not considered as able to trigger an explosion in
normal operating modes and various fault modes in accordance with
the requirements for Cat 2 equip ment. These materials are not known
to react with any explosive atmo spheres to which the M6C may be
subject. It is however the responsibility of the end user to ensure that
the M6C is selected correctly for the potentially explosive atmosphere
in which the equipment is to be put into service.
INSTALLATION
CONDITIONS FOR SAFE USE
• Installation should be performed only by qualified personnel.
Safety precautions must be taken to ensure machinery cannot
rotate and all sources of power are removed during installation.
• Termination instructions on sheet 2 must be followed to ensure
“Increased Safety” rating of entry cover
• The M6C “Increased Safety” conduit entry covers must not be
opened in Flammable Atmosphere or when energized. Tighten
cover screws to 40 in-lb [4.5 N-m] to prevent loosening.
• The ambient temperature range is: -20°C
≤
Tamb
≤
80°C standard.
-40°C
≤
Tamb
≤
80°C for modification codes 001 and 005.
• Contact the original manufacturer for information on the flameproof
joints.
• Socket head cap screws holding the flameproof cover onto the
encoder have a minimum yield strength of 1220 N/mm2.
• Do not open the M6C housing. Doing so will void the warranty and
may cause the risk of fire or explosion. There are no field
replaceable parts in the M6C. The unit should be returned to the
factory for all repairs.