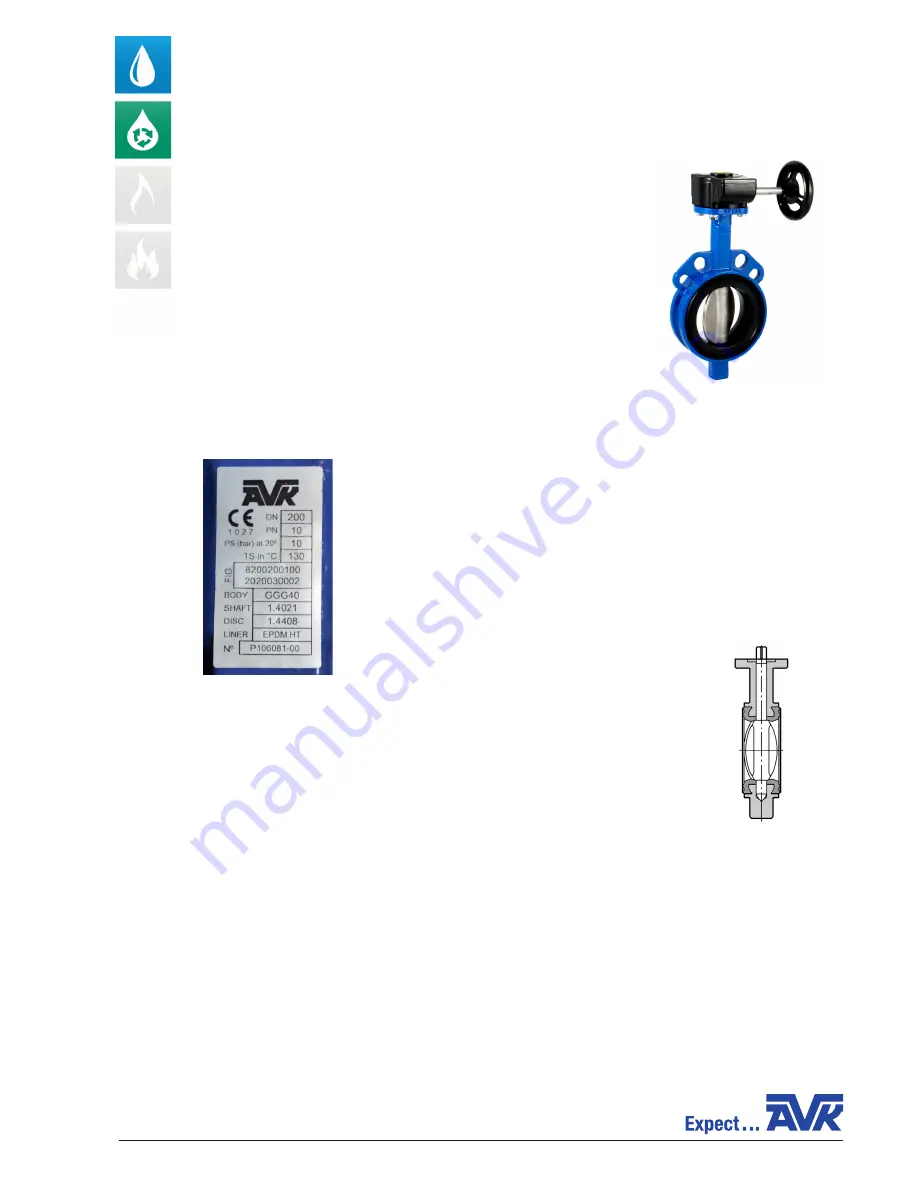
1. INTRODUCTION
To guarantee the benefits of the butterfly valves, proper procedures and
compliance with this installation instruction are essential. The installation
must be carried out according to
good installation practise
and only by
qualified personnel. AVK reserves the right to decline responsibility for
damage or failure caused by non-compliance with the recommendations
in this instruction.
Please note that fluid residues inside the butterfly valve may be dangerous to
people and to the environment. The butterfly valve must be handled with the
necessary precaution and must be carefully cleaned prior to maintenance.
Any kind of maintenance is performed on the user´s own risk and must be
executed by trained staff only. Only original spare parts must be used.
Dimensions, materials and application of the butterfly valves are according to
series 820 datasheets.
2. MARKING
Label:
• Manufacturer
• Product specification
• Item number
• Material specification
• Internal order number
3. STORAGE
AVK butterfly valves must always be stored free from dust and humidity.
The valve is supplied with the disc slightly open and must remain so until the installation is
completed (fig. 1).
Butterfly valves supplied with a single acting spring closing pneumatic actuator must be
stored with disassembled actuator to avoid a permanent deformation of the liner. The
actuator is mounted after installation of the valve in the piping.
INSTALLATION & MAINTENANCE INSTRUCTIONS - ORIGINAL VERSION
AVK BUTTERFLY VALVES, CENTRIC WITH LOOSE LINER
SERIES 820
COPYRIGHT©AVK GROUP A/S 2014 - AVK INTERNATIONAL A/S, BIZONVEJ 1, DK-8464 GALTEN - WWW.AVKVALVES.EU
MI Butterfly820 rev. C August 2017 GB
FIG. 1