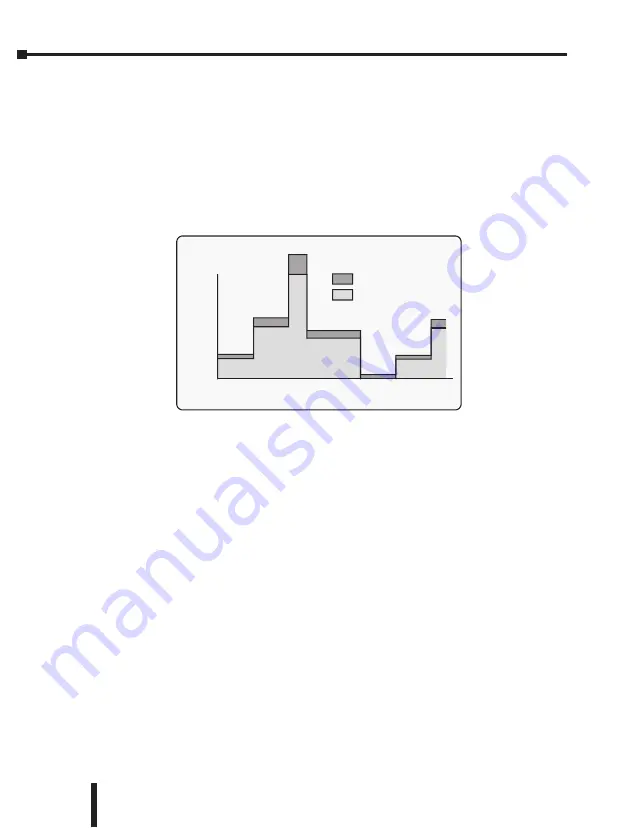
Chapter 3: Applications
3.4.5 – How Much Energy?
The amount of energy used by a squirrel-cage induction motor operating with a soft starter in
energy-optimizing mode is shown in the following figure (Figure 3.4.5.1), for the same duty cycle
as Figure 3.4.1.2. By reducing the voltage when torque demand is below maximum, the
magnetizing current is proportioned to the torque current.
Compare Figure 3.4.5.1 (energy-optimizing) with Figure 3.4.1.2 (non-optimizing). (These graphical
representations are illustrative only and not to scale.) Arriving at any exact figure for the energy
cost saved requires each individual case to be examined in detail, taking into account the motor
rating, type, and any special characteristics such as load, load characteristics, duty cycle, supply
voltage, and the cost of electricity.
Figure 3.4.5.1: Energy Savings
The calculations to cover all the likely or possible conditions would be laborious. An empirical
method for arriving at a usefully realistic estimate has been devised. Used with a proper sense of
engineering circumspection, the tables in Section 3.4.6 allow a user to gain a reasonably close
estimate of the savings to be achieved within the motor by using the SR44 optimizing Soft Starter.
The method does not include any additional savings and benefits conferred by other sources, such
as:
• reduction of
heating losses
in cabling because of the lower voltages;
• potential reduction of
maximum demand
charges;
• further energy savings and other benefits deriving from the soft-starting process itself;
• reduced
total energy demand
;
• reduced
wear and tear
;
• reduced
maintenance and replacement
costs.
40 60 80 100 120 140 160
seconds
%
FLC
100
50
0
Current demand with Energy Saving in operation
Magnetizing current
Torque current
SR44 Series Soft Starter User Manual
1st Ed, Rev B 07/31/2019
3–18
Summary of Contents for Stellar SR44
Page 1: ...STELLAR SR44 SOFT STARTER USER MANUAL SR44 M WO 1st Edition Revision B...
Page 2: ...BLANK PAGE SR44 Series Soft Starter User Manual 1st Ed Rev B 07 31 2019...
Page 6: ...SR44 Series Soft Starter User Manual 1st Ed Rev B 07 31 2019 w 4 BLANK PAGE...
Page 8: ...BLANK PAGE SR44 Series Soft Starter User Manual 1st Ed Rev B 07 31 2019...
Page 12: ...Table of Contents BLANK PAGE SR44 Series Soft Starter User Manual 1st Ed Rev B 07 31 2019 t 4...
Page 23: ...ELECTRICAL INSTALLATION 2 CHAPTER CHAPTER 2 2 CHAPTER BLANK PAGE 2 1c...
Page 75: ...KEYPAD MENU ITEMS AND PARAMETERS CHAPTER 5 CHAPTER CHAPTER 5 BLANK PAGE 5 5 1c...
Page 237: ...BLANK PAGE SR44 Series Soft Starter User Manual 1st Ed Rev B 07 31 2019...
Page 238: ...SR44 Series Soft Starter User Manual 1st Ed Rev B 07 31 2019...