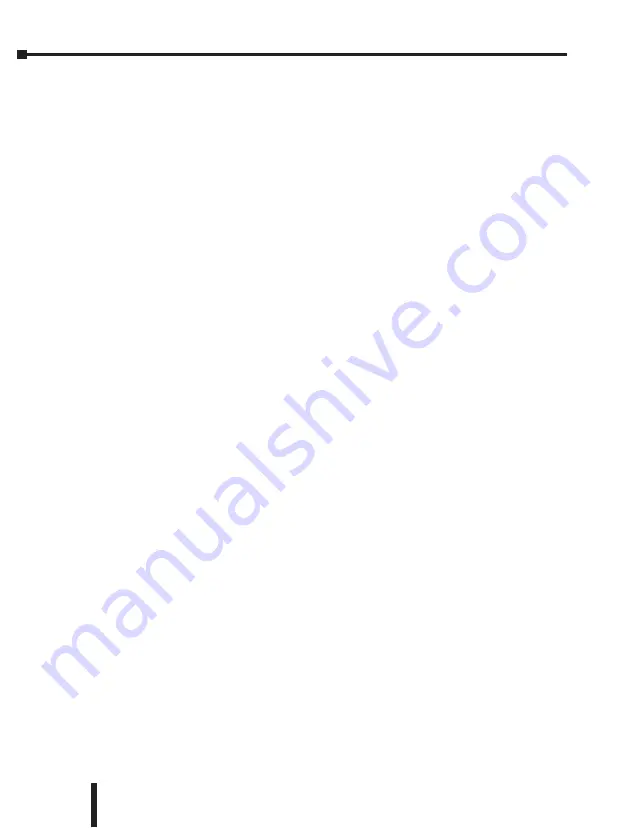
Chapter 3: Applications
There are methods of control, for example, the Wauchope starter, which eliminate or reduce the
reconnection transients. However, such starters are expensive and have reliability implications,
and they are not widely applied for these reasons.
The wye-delta starter also has disadvantages due to the restricted starting torque available (if you
need 40% LRT to break-away, you can only increase the motor size, or revert to direct-on-line).
Combined with the severe effects of the re-switching surges, and the additional costs of bringing
six conductors from the motor to the starter instead of only three; wye-delta only offers an
imperfect solution to the problem of starting the induction motor.
Method C: Primary Resistance Starter
It has long been recognized that the transition step in the wye-delta system was a source of
problems such as welded contactors, sheared drive shafts etc. For many years a method of stepless
control has been available in the form of the primary resistance starter.
This type of controller inserts a resistance in one, or more often in each, of the phase connections
to the stator at start-up, after which it is progressively reduced and shorted out at the end of the
acceleration process. Frequently, the resistances are movable blades that are gradually inserted
into an electrolyte liquid. The mechanism is usually large and expensive, both to purchase and to
maintain, and considerable heat is created by the passage of current through the electrolyte
resistor. This limits the starting frequency (because the electrolyte has to condense back to liquid
before a new start can proceed), and these restrictions prevent this starter from being a popular
option when selecting a control system. However, it has the distinction of being the smoothest
and least stressful method of accelerating an induction motor and its load.
Method D: Other Electro-Mechanical Systems
Other control methods such as auto-transformer starting (popular in North America), primary
reactance starting etc., are employed to a greater or lesser extent, to compensate for some of the
disadvantages of each type of starter discussed. Nevertheless, the fundamental problems of
electro-mechanical starters remain, and it is only in the last decade or two that their dominance
has been challenged by the introduction of power semiconductors controlled by electronics.
3.3.5 – The Semiconductor Motor Controller
During the 1950s, much effort was put into the development of a four-layer transistor device which
had the power to switch large currents at high voltages when triggered by a very small pulse of
current. This device became known as the silicon controlled rectifier (SCR), or in Europe, the
“Thyristor”, and it is the basis on which all soft starting systems are built. The characteristic of
most interest is the ability of the thyristor to switch rapidly (in about 5 millionths of a second) from
“OFF” to “ON” when pulsed, and to remain “ON” until the current through the device falls to
zero (which conveniently happens at the end of each half-cycle in alternating current supplies).
By controlling the switch-on point of a thyristor relative to the voltage zero crossing in each half
wave of an alternating current, it is possible to regulate the energy passing through the device. The
closer the turn-on point is to the voltage zero crossing point, the longer the energy is allowed to
flow during the half-cycle. Conversely, delaying the turn-on point reduces the time for the energy
to flow. Putting two thyristors back-to-back (or anti-parallel) in each of the phase connections to a
motor, and by precisely controlling their turn-on points, an electronic soft starter continuously
adjusts the passage of energy from the supply so that it is just sufficient for the motor to perform
satisfactorily.
So, for instance, by starting with a large delay to the turn on point in each half cycle, and
progressively reducing it over a selected time period, the voltage applied to the motor starts from a
relatively low value and increases to full voltage. Due to the motor torque being proportional to
the square of the applied voltage, the starting torque follows the same pattern giving the
characteristic smooth, stepless start of the soft starter.
SR44 Series Soft Starter User Manual
1st Ed, Rev B 07/31/2019
3–12
Summary of Contents for Stellar SR44
Page 1: ...STELLAR SR44 SOFT STARTER USER MANUAL SR44 M WO 1st Edition Revision B...
Page 2: ...BLANK PAGE SR44 Series Soft Starter User Manual 1st Ed Rev B 07 31 2019...
Page 6: ...SR44 Series Soft Starter User Manual 1st Ed Rev B 07 31 2019 w 4 BLANK PAGE...
Page 8: ...BLANK PAGE SR44 Series Soft Starter User Manual 1st Ed Rev B 07 31 2019...
Page 12: ...Table of Contents BLANK PAGE SR44 Series Soft Starter User Manual 1st Ed Rev B 07 31 2019 t 4...
Page 23: ...ELECTRICAL INSTALLATION 2 CHAPTER CHAPTER 2 2 CHAPTER BLANK PAGE 2 1c...
Page 75: ...KEYPAD MENU ITEMS AND PARAMETERS CHAPTER 5 CHAPTER CHAPTER 5 BLANK PAGE 5 5 1c...
Page 237: ...BLANK PAGE SR44 Series Soft Starter User Manual 1st Ed Rev B 07 31 2019...
Page 238: ...SR44 Series Soft Starter User Manual 1st Ed Rev B 07 31 2019...