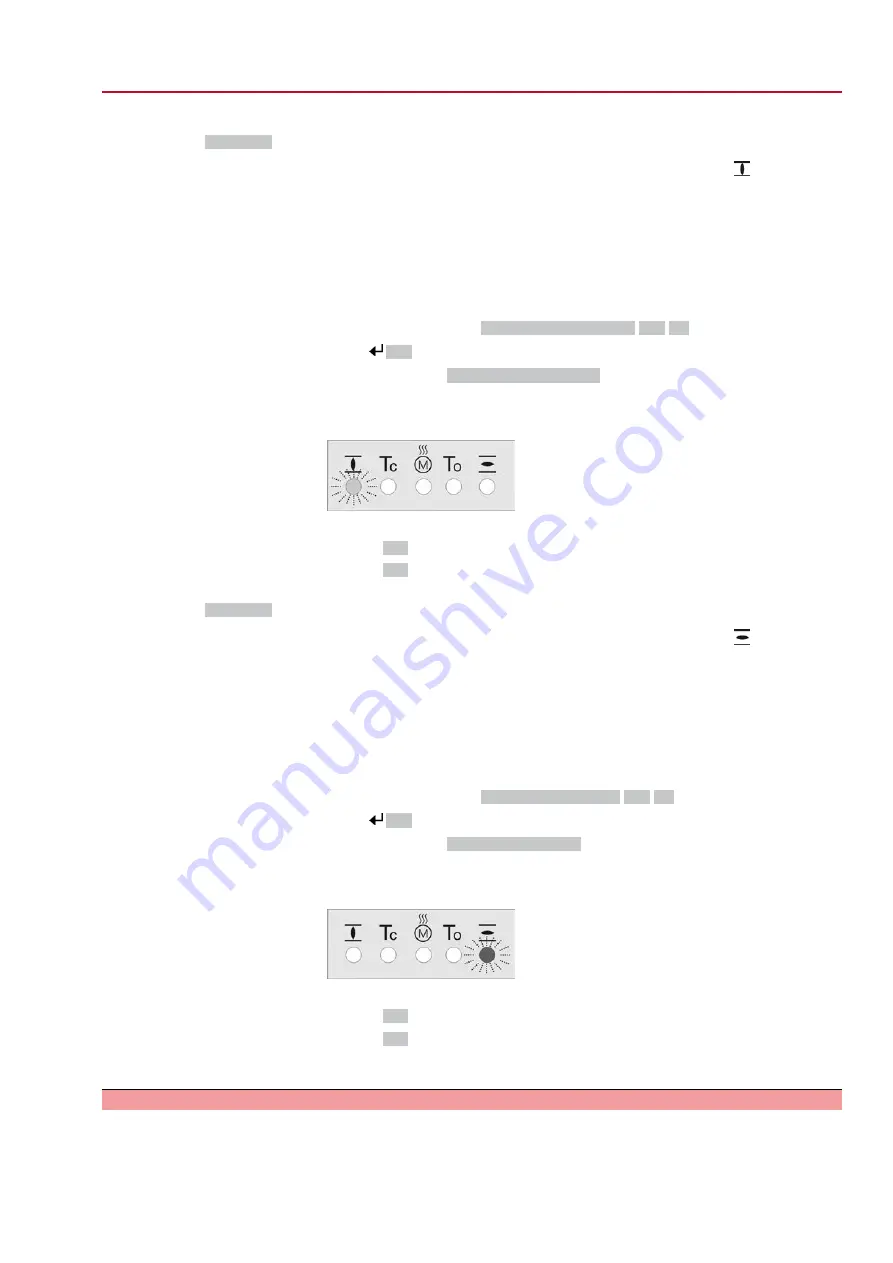
Set end position
CLOSED
CMD0009
9.
Set end position CLOSED again :
9.1 For large strokes: Set selector switch in position Local control (LOCAL)
and operate actuator in motor operation via push button
(CLOSE) in
direction of the end position.
Information: Stop actuator before reaching end of travel (press STOP
push button to avoid damage.
9.2 Engage manual operation.
9.3 Turn handwheel until valve is closed.
9.4 Set selector switch to position 0 (OFF).
➥
Display indicates:
Set end pos.CLOSED? Yes No
Confirm new end posi-
tion
10. Press
Yes
to confirm new end position.
➥
Display indicates:
End pos. CLOSED set!
➥
The left LED is illuminated (standard version) and thus indicates that the end
position CLOSED setting is complete.
11. Make selection:
→
Edit →
back to step 9: Set end position CLOSED "once again"
→
Esc →
back to step 4; either set end position OPEN or exit the menu.
Set end position OPEN
CMD0010
12. Re-set end position OPEN:
12.1 For large strokes: Set selector switch in position Local control (LOCAL)
and operate actuator in motor operation via push button
(OPEN) in
direction of the end position.
Information: Stop actuator before reaching end of travel (press STOP
push button to avoid damage.
12.2 Engage manual operation.
12.3 Turn handwheel until valve is open.
12.4 Set selector switch to position 0 (OFF).
➥
Display indicates:
Set end pos. OPEN? Yes No
Confirm new end posi-
tion
13. Press
Yes
to confirm new end position.
➥
Display indicates:
End pos. OPEN set!
➥
The right LED is illuminated (standard version) and thus indicates that the end
position OPEN setting is complete.
14. Make selection:
→
Edit →
back to step 12: Set end position OPEN "once again"
→
Esc →
back to step 4; either set end position CLOSED or exit the menu.
Information
If an end position cannot be set: Check the type of control unit in actuator.
10.5.
Operating time (internal): set
Internal operation time setting is only possible if the speed source is set to internal
operating time. If the actuator is controlled via an external speed source, the internal
operating values will not have an impact on the operation behaviour.
67
SQVEx 05.2 – SQVEx 14.2/ SQRVEx 05.2 – SQRVEx 14.2 Control unit: electronic (MWG)
ACVExC 01.2 Modbus RTU
Commissioning (basic settings)