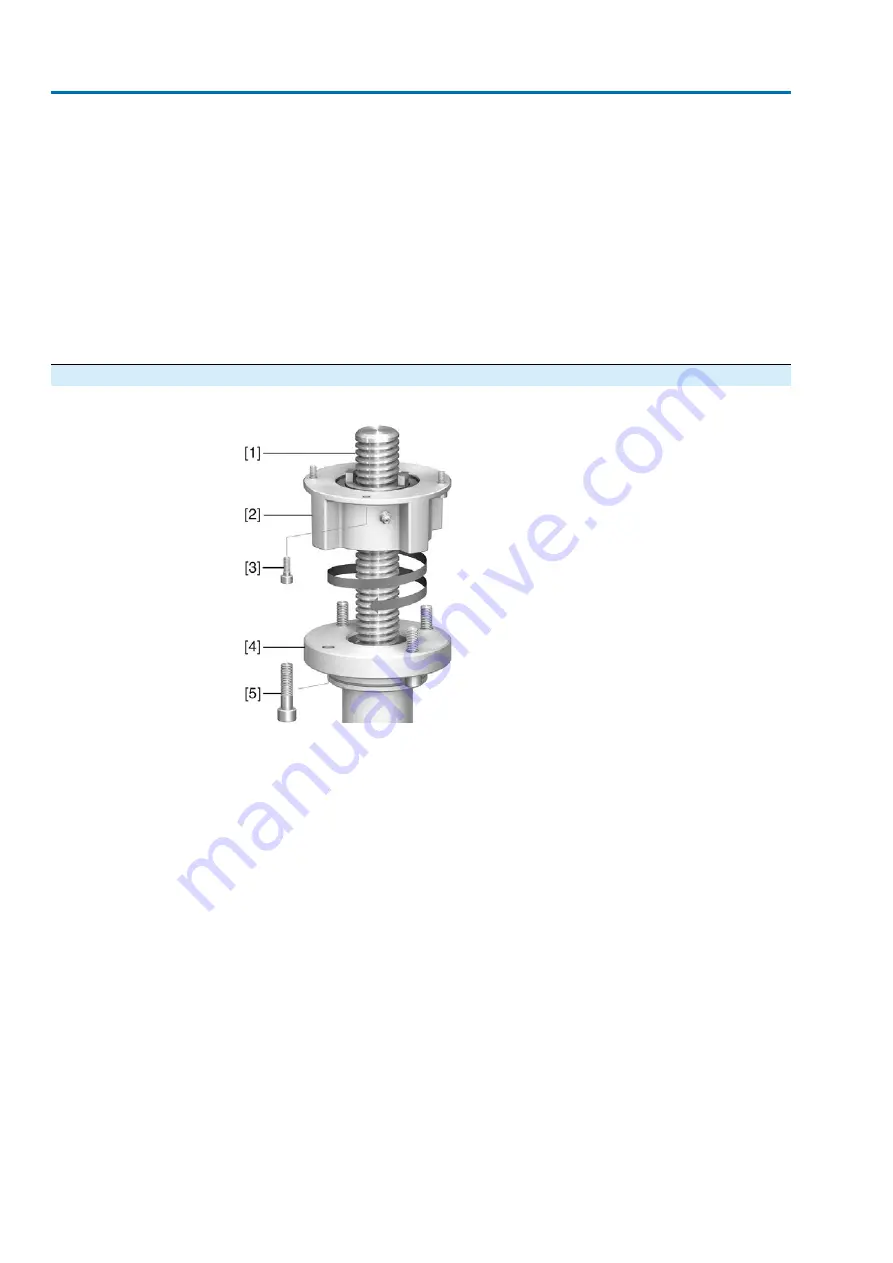
4.
Drill and bore stem nut [1] and cut thread.
Information: When fixing in the chuck, make sure stem nut runs true!
5.
Clean the machined stem nut [1].
6.
Apply sufficient Lithium soap EP multi-purpose grease to axial needle roller and
cage assemblies [2.2] and axial bearing washers [2.1], ensuring that all hollow
spaces are filled with grease.
7.
Place greased axial needle roller and cage assemblies [2.2] and axial bearing
washers [2.1] onto stem nut [1].
8.
Re-insert stem nut [1] with bearings [2] into output drive.
Information: Ensure that dogs or splines are placed correctly in the keyway of
the hollow shaft.
9.
Screw in spigot ring [3] until it is firm against the shoulder.
4.3.1.2. Multi-turn actuator (with output drive type A): mount to valve
Figure 11: Assembly of output drive type A
[1]
Valve stem
[2]
Output drive type A
[3]
Screws to actuator
[4]
Valve flange
[5]
Screws to output drive
1.
If the output drive type A is already mounted to the multi-turn actuator: Loosen
screws [3] and remove output drive type A [2].
2.
Check if the flange of output drive type A matches the valve flange [4].
3.
Apply a small quantity of grease to the valve stem [1].
4.
Place output drive type A on valve stem and turn until it is flush on the valve
flange.
5.
Turn output drive type A until alignment of the fixing holes.
6.
Screw in fastening screws [5], however do not completely tighten.
7.
Fit multi-turn actuator on the valve stem so that the stem nut dogs engage into
the output drive sleeve.
➥
The flanges are flush with each other if properly engaged.
8.
Adjust multi-turn actuator until alignment of the fixing holes.
9.
Fasten multi-turn actuator with screws [3].
18
SAVEx 07.2 – SAVEx 16.2 / SARVEx 07.2 – SARVEx 16.2 Control unit: electronic (MWG)
Assembly
ACVExC 01.2 Non-Intrusive Modbus RTU