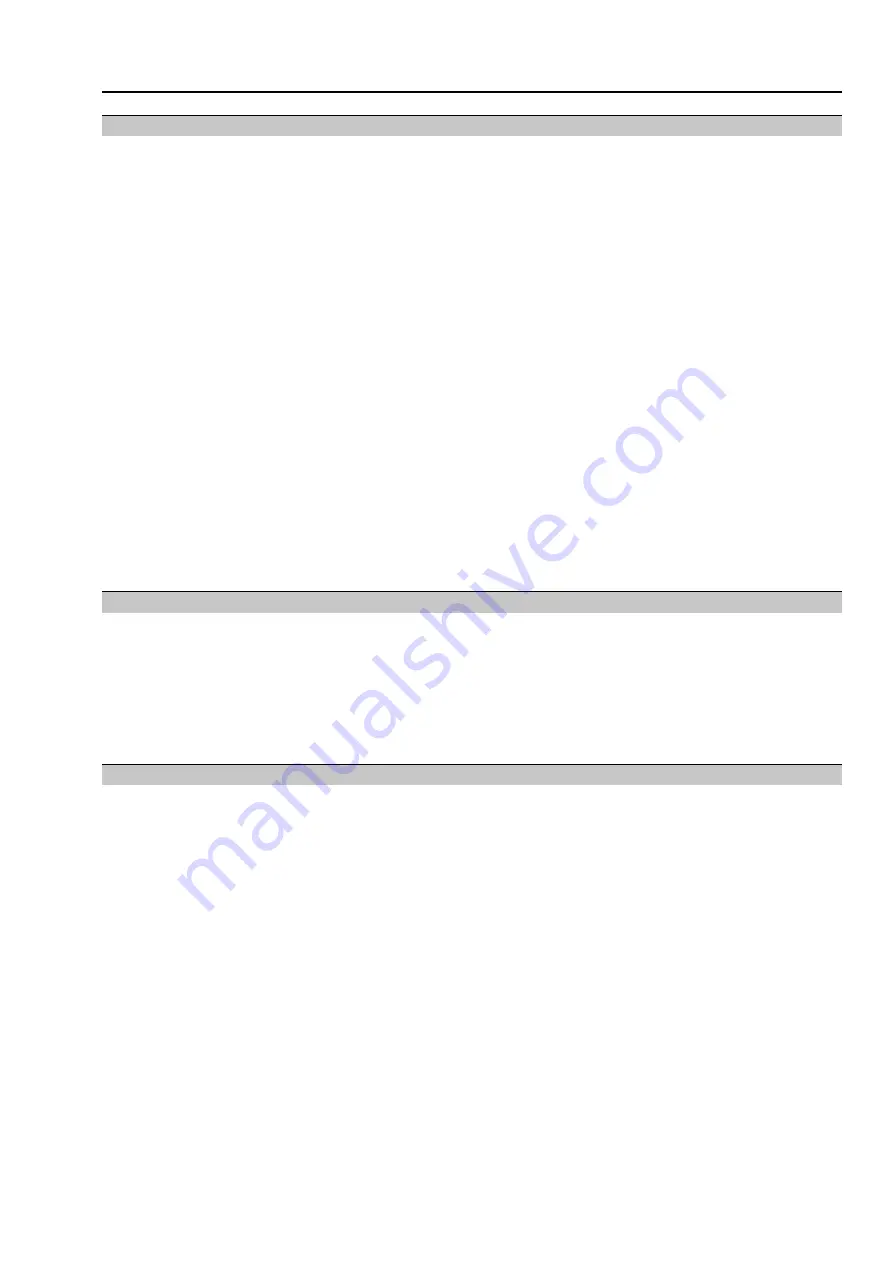
3.3.
Protection against uncontrolled operation (self-locking/brake)
For self-locking AUMA actuators, it can be assumed that a load up to maximum
torque will not result in uncontrolled valve operation from standstill due to valve torque
load. Consequently, in these cases, further protection against uncontrolled operation
is not imperatively required. This might become necessary if, for example, self-locking
can either not be guaranteed due to vibration or if it is insufficient. In addition, certain
applications may require active position locking, for example by using a brake. There
are user-specific standards demanding this type of protection. Therefore, each project
must be subject to individual verification if any further protection is required. In any
case, this protection is required for actuators without self-locking.
At the time of compilation of this document, the available actuators of the type ranges
below were self-locking: SQ 05.2 – SQ 14.2, SQR 05.2 – SQR 14.2, SQEx 05.2 –
SQEx 14.2 and SQREx 05.2 – SQREx 14.2.
If actuators with insufficient self-locking function paired with “Forced torque seating
in end position” SIL seating type are used for the safety function, the following effect
might occur: During ESD, the actuator operates to the end position and switches off
due to reaching the end position and the tripping torque. Thereafter, the gear train
is relieved and the torque falls below the preset limit value. As a matter of fact, the
actuator controls detect this incident and switch the actuator on again since the
behaviour is correctly considered as termination of the ESD condition. The latter
generates additional torque until the switching off condition is reached again, and
so on. The “pumping effect” of the actuator is the consequence.
To successfully avoid this incident, we recommend either selecting actuator or other
elements with sufficient self-locking within the gear train or – if acceptable from a
process and safety point of view – selecting “Forced limit seating in end position” as
safety function.
3.4.
Operation mode (low/high demand mode)
The safety functions of the actuators supplied by AUMA are suitable for the low
demand mode and may only be used in this operation mode. If a non-safety
instrumented function of basic process control system is executed via the same
actuator in addition to the safety function, note that while considering the sum of
non-safety instrumented function, required tests and safety function, the defined
number of maximum permissible cycles
1)
for the respective actuator as well as the
maximum number of starts
2)
may not be exceeded during deployment of the actuator
within a safety instrumented system.
3.5.
Further notes and indications on architecture
HFT is 0.
The systematic capability is 3 (SC=3).
Only flanges of F07 or FA 07 sizes or larger may be used for valve attachment.
If the actuator is equipped with one of the three position transmitter types, i.e. MWG,
RWG or EWG, these elements may not be integrated within the safety instrumented
system.
The actuator safety functions can be considered as type A device.
The operating time for a complete travel must exceed 4 seconds. Attention: Any
modification of the nominal swing angle (90°) results in operating time change.
Safety function(s) and their feedback signals may only be issued via the digital inputs
and outputs of the SIL module.
The signal issued via
SIL fault
output must be permanently evaluated. If the
output signals a fault, assumption can be made that the safety function is not
available. The safety function must be checked without delay. Possibly further safety
measures are to be taken until the safety function is restored without fault.
1)
Definition of “cycles” according to EN 15714-2:2010
2)
Definition of “starts” according to EN 15714-2:2010
11
Part-turn actuators
with AC 01.2-SIL/ACExC 01.2-SIL
Architecture, configuration and applications