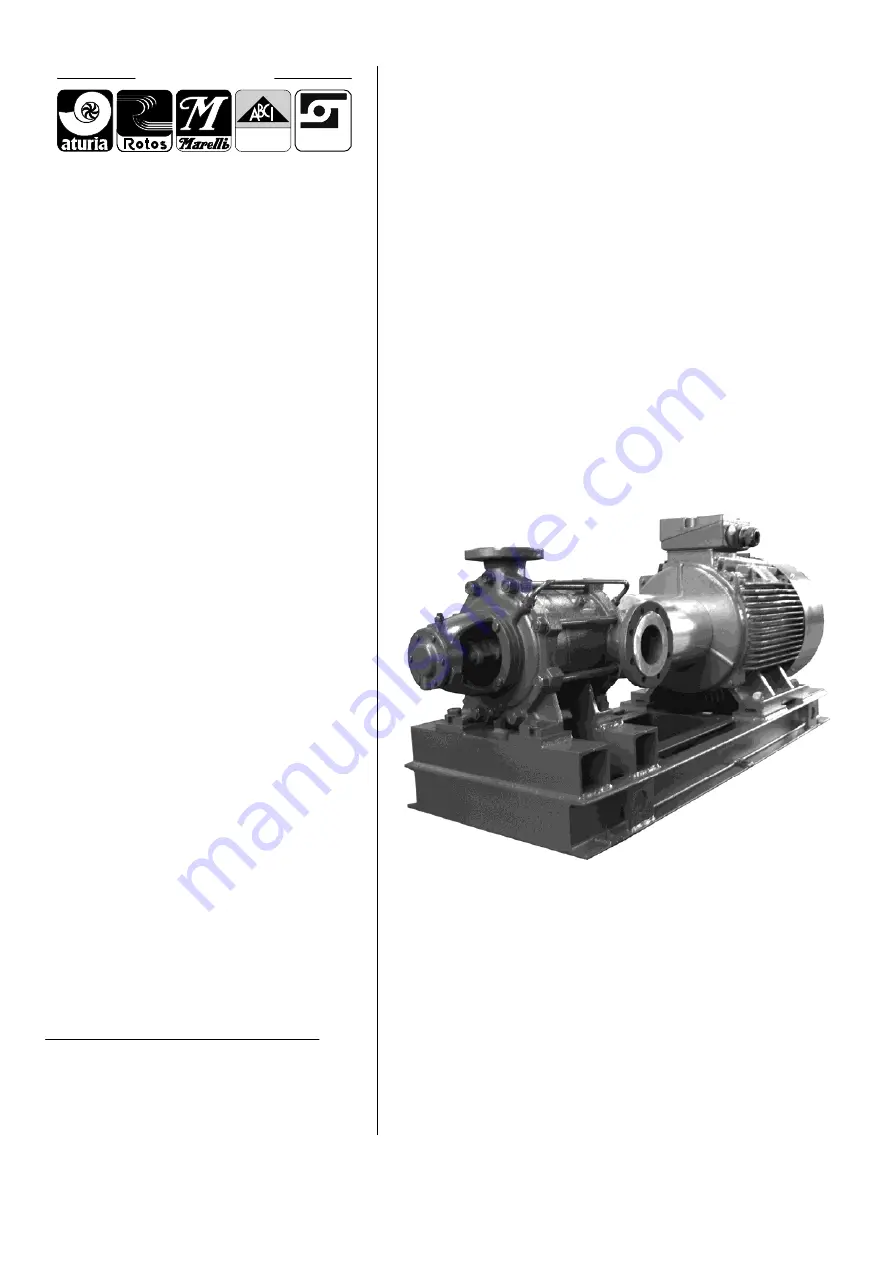
LTK0E01D 05/2017
1
T
T
K
K
M
M
U
U
L
L
T
T
I
I
S
S
T
T
A
A
G
G
E
E
C
C
E
E
N
N
T
T
R
R
I
I
F
F
U
U
G
G
A
A
L
L
P
P
U
U
M
M
P
P
S
S
I
I
N
N
S
S
T
T
R
R
U
U
C
C
T
T
I
I
O
O
N
N
M
M
A
A
N
N
U
U
A
A
L
L
20060 Gessate (MILANO), ITALY / Piazza Aturia, 9
Tel. +39-0295423200 /Fax +39-0295423202
www.gruppoaturia.com
Gruppo Aturia
S.p.A.
Gruppo Aturia
AUDOLI &
BERTOLA
ARIS
CHIAPPA
Summary of Contents for TK
Page 23: ......
Page 24: ...LTK0E01B 01 2012 23 ...
Page 25: ...LTK0E01B 01 2012 24 ...
Page 26: ...LTK0E01B 01 2012 25 ...
Page 27: ......
Page 28: ...LTK0E01B 01 2012 26 ...
Page 29: ...LTK0E01B 01 2012 27 ...
Page 30: ...LTK0E01B 01 2012 28 ...
Page 32: ......