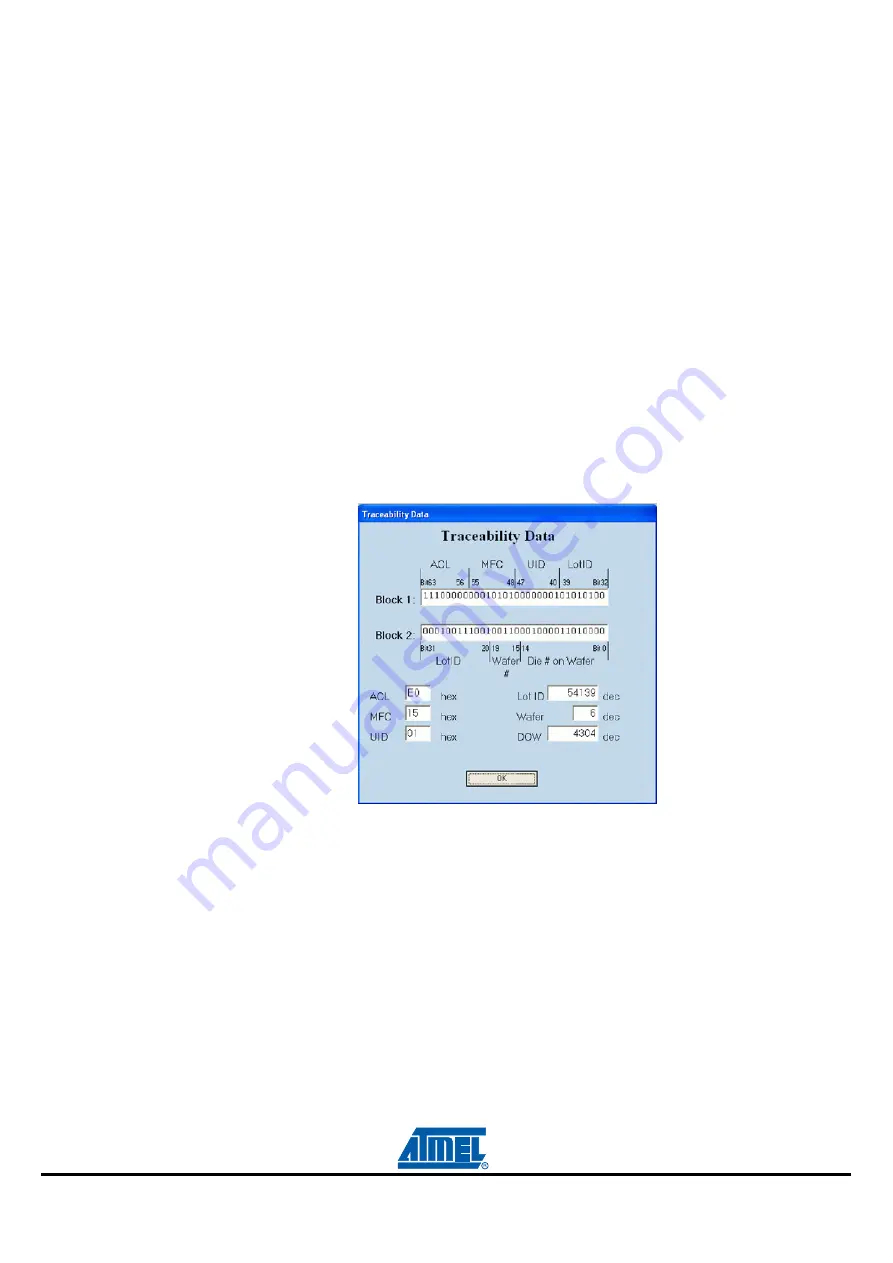
Host Software
RFID Application Kit ATAK2270 User Manual
5-25
4871E–RFID–04/08
5.4.3
Readout Manufacturer (Traceability) Data
The Traceability Data button allows direct access to block 1 an 2 of page 1 which contain the 64-bit
traceability data programmed and locked by Atmel during production. The data consist of both,
ISO/IEC15693 and ISO/IEC7816-6 compliant identifiers:
ACL Allocation
Class
MFC
Manufacturer Code
UID
Unique Identification Class
Furthermore, the trace data contain production specific information from manufacturer:
Lot ID
Lot ID Number
Wafer
Wafer Number
DOW
Die On Wafer Number
To read out the data, the Terminator synchronization has to be configured in advance, but the trace data
cannot be synchronized by a header.
Figure 5-26. Traceability Data Window
ACL Allocation
Class
MFC
Manufacturer Code
UID
Unique ID Customer
Lot ID
Lot ID Production Number
Wafer
Wafer Production Number
DOW
Die On Wafer Production Number
The Traceability Data window shows the data contents in two formats:
The text box Block 1 and Block 2 show the binary data stream stored by Block 1 and Block 2, 32 bits
each. The bit position of the various ISO identifiers is shown.
The text box ACL, MFC, UID, Lot ID, Wafer, and DOW show the trace information converted to hex
format for easier interpretation of the data.