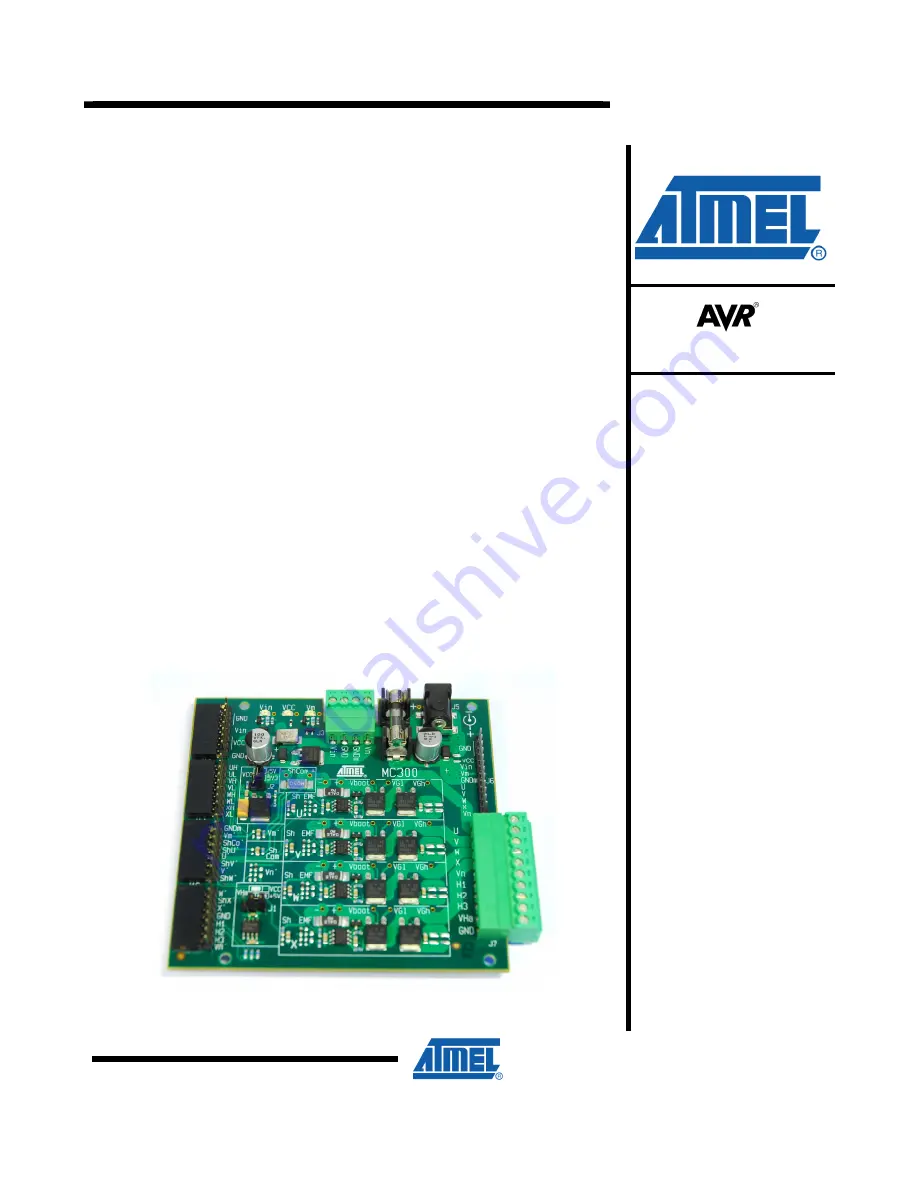
AVR430: MC300 Hardware User Guide
Features
•
General-purpose power stage for DC and stepper motors
•
Modular system with 2,54mm pin header connector for device boards
•
Four half-bridges with independent control of high and low side
•
Onboard voltage regulators for device board (5/3,3V) and Hall sensors (5V)
•
Hall sensor, back-EMF and center voltage feedback to device board
•
Shunt resistor feedback to device board
•
Electric specifications:
-
Driver circuit: Vin 10-20V
-
Motor: Vm 0-40V, Im
max
=6A
•
Dimension: 100x100mm
1 Introduction
The MC300 is a general-purpose power stage board able to drive brushless DC,
brushed DC and stepper motors. The board is designed to be a flexible platform for
developing motor control applications. Power and all signals needed for a controller
(AVR
®
CPU) are available on the left side of the board, giving a modular system
where boards with different microcontrollers can easily be connected.
Figure 1-1.
MC300 Motor control driver board.
8-bit
Microcontrollers
Application Note
Rev. 8124C-AVR-10/08