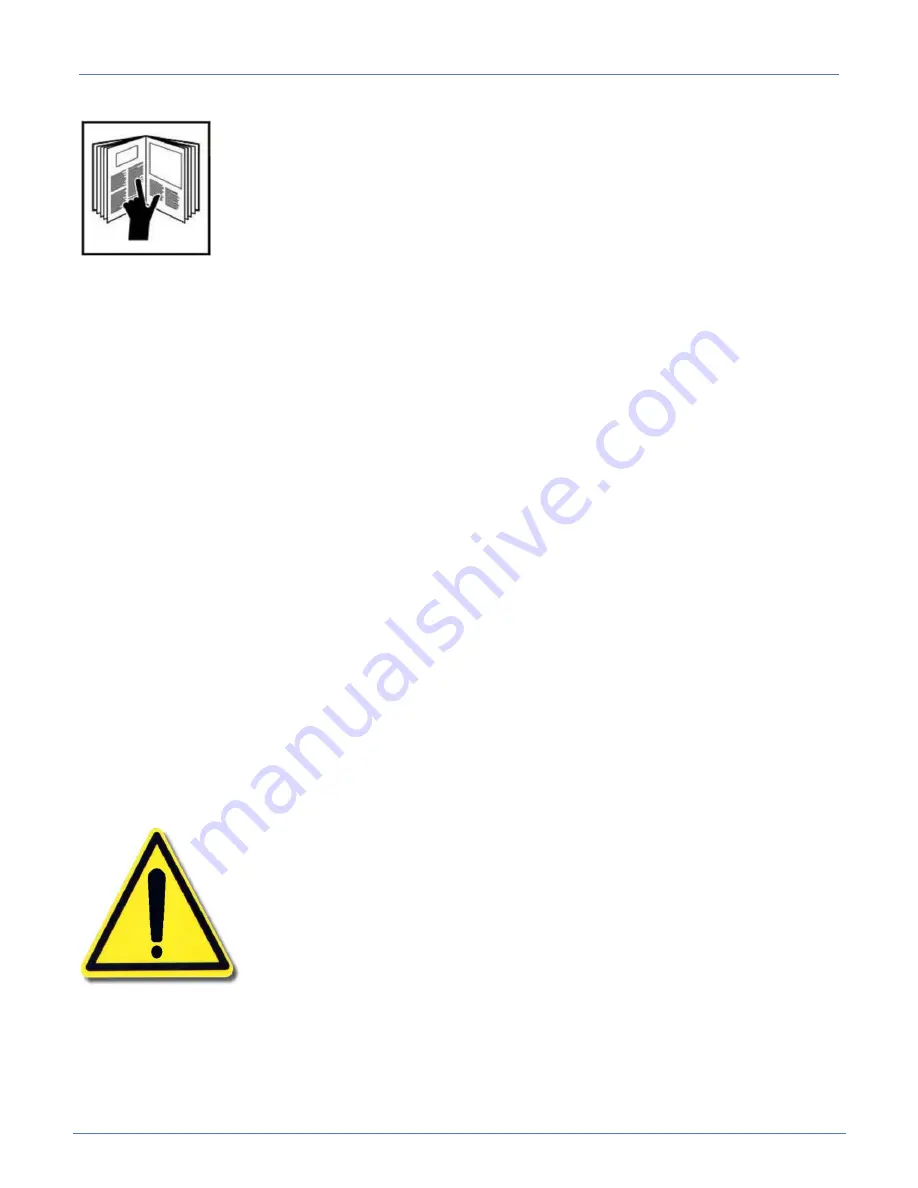
Technical Manual & Parts Lists
1
Important Safety Instruction
This part of the Instruction Material is provided for the safe use of your equipment.
It contains important information to help work safely with the unit and describes the
dangers inherent in machinery. Some of these dangers are obvious, while others are
less evident.
Mandatory Information
All persons operating and/or working on the 4300A should read and understand all parts of the Safety
Instructions. This applies, in particular, for persons who only operate and/or work on the unit
occasionally (e.g. for maintenance and repair). Persons who have difficulty reading must receive
particularly thorough instruction.
Scope of the Instruction Material
The Instruction Material comprises:
Safety information
Operator Instructions
Electrical and Pneumatic diagrams
And may also include;
A list of recommended spare parts
Instruction Manual(s) for components made by other manufacturers
The layout and installation diagram containing information for installation
Intended Use
Our machines are designed and built in line with the state of the art and the accepted safety rules.
However, all machines may endanger the life and limb of their users and/or third parties and be damaged
or cause damage to other property, particularly if they are operated incorrectly or used for purposes
other than those specified in the Instruction Manual.
Exclusion of Misuse
Non-conforming uses include, for example, using the equipment for something
other than it was designed for, as well as operation without duly installed safety
equipment. The risk rests exclusively with the end user.
Conforming use of the machine includes compliance with the technical data,
information and regulations in all parts of the complete Instruction Material, as
well as compliance with the maintenance regulations. All local safety and
accident prevention regulations must also be observed.
From
the
library
of:
Diamond
Needle
Corp
Summary of Contents for 4300A
Page 2: ...From the library of Diamond Needle Corp ...
Page 28: ...Technical Manual Parts Lists 21 4 Create Edit Style From the library of Diamond Needle Corp ...
Page 78: ...Technical Manual Parts Lists 71 From the library of Diamond Needle Corp ...
Page 80: ...Technical Manual Parts Lists 73 From the library of Diamond Needle Corp ...
Page 92: ...Technical Manual Parts Lists 85 From the library of Diamond Needle Corp ...
Page 94: ...Technical Manual Parts Lists 87 From the library of Diamond Needle Corp ...
Page 98: ...Technical Manual Parts Lists 91 From the library of Diamond Needle Corp ...
Page 100: ...Technical Manual Parts Lists 93 From the library of Diamond Needle Corp ...
Page 104: ...Technical Manual Parts Lists 97 From the library of Diamond Needle Corp ...
Page 106: ...Technical Manual Parts Lists 99 From the library of Diamond Needle Corp ...
Page 112: ...Technical Manual Parts Lists 105 From the library of Diamond Needle Corp ...
Page 114: ...Technical Manual Parts Lists 107 From the library of Diamond Needle Corp ...
Page 116: ...Technical Manual Parts Lists 109 From the library of Diamond Needle Corp ...
Page 118: ...Technical Manual Parts Lists 111 From the library of Diamond Needle Corp ...
Page 122: ...Technical Manual Parts Lists 115 From the library of Diamond Needle Corp ...