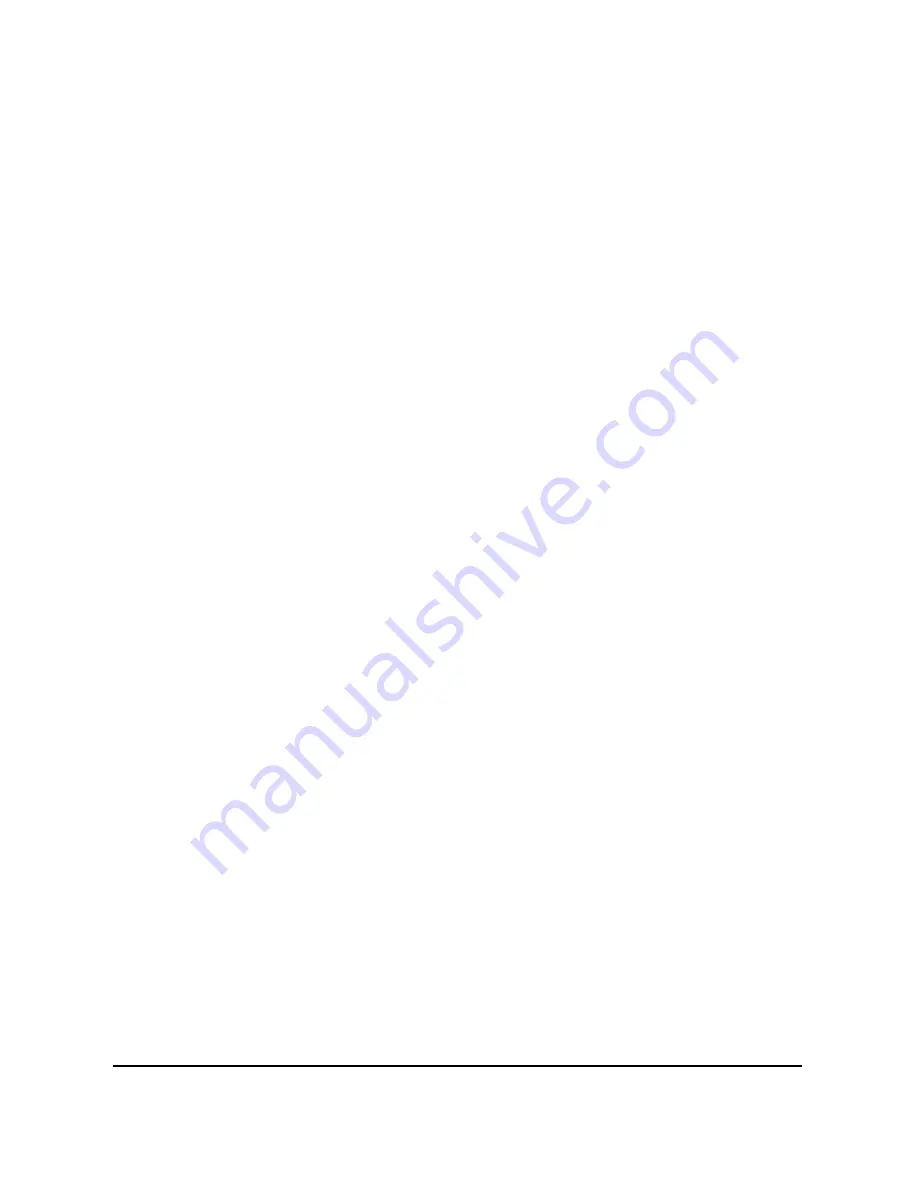
Quick-Change
Installation and Operation Manual
Document #9620-20-c-dkgm dkft-03
Pinnacle Park
•
1031 Goodworth Drive
•
Apex, NC 27539
•
Tel: 919.772.0115
•
Fax: 919.772.8259
•
www.ati-ia.com
•
Email: info@ati-
ia.com
C - 3
C. Control and Signal Modules
DKG-M and DKF-T—EtherNet/IP Control &
Quick Connect Pass-through Modules
1. Product Overview
The EtherNet/IP modules enable the user to control and communicate with ATI's Heavy Automation Robotic
Tool Changers using EtherNet/IP. It also passes the EtherNet/IP network through a managed switch to the
tool side. With the default switch settings it supports EtherNet/IP Quick Connect. This allows utilizing
EtherNet/IP on the Robot- and on the Tool-side with short connection times.
Control of the Tool Changer is realized through the Master Node along with the reporting of Tool Changer
I/O, such as Lock, Unlock, and Ready-to-Lock signals. The Tool-side module supports Tool-ID reported
through the Master-side and functions as a pass-through for the EtherNet/IP network and power to
downstream equipment.
When the Tool Changer is coupled, the Master and Tool modules pass signals using a spring-loaded pin
block. A flexible boot surrounds the pin block to seal the connection from moisture and liquid while coupled
(see
and for more information refer to
Section 10—Drawings
General fault reporting is supported for the presence of power for Logic/Inputs and the Tool Changer valve.
Advanced diagnostic and fault reporting is supported for output short circuit and overload conditions as well
as for the presence of Tool-ID. Refer to
Sections 3—Product Information
Section 4—Operation
for more
information on these attributes.
The DKG Module incorporates ATI’s exclusive Arc Prevention Circuit which extends the life of all electrical
power contacts on the pin block. Refer to
Section 3.2—Arc Prevention Circuit
for more information about
this feature.
A single or double solenoid valve is provided with the Master valve adapter for Lock/Unlock control of the
Tool Changer. The user is required to provide a pneumatic supply source to the Tool Changer.
The Unlock signal to the solenoid valve is routed through a “Tool Stand Interlock” (TSI) safety circuit that
prevents the robot from unlocking the Tool from the Master when the mated assembly is not in a Tool Stand.
1.1 Master Module
One standard 4-Pin Mini connector is provided on the Master for the power supply of the DKG’s
EtherNet/IP interface and sensor inputs. The same 4-Pin connector also supplies the output power to the
Tool module. One 4-Pin M12 D-Coded connector is provided on the Master module for EtherNet/IP
communications interface with the Master and downstream tooling.
1.2 Tool Module
The DKF Tool module employs a thumbwheel switch for setting the Tool-ID input. This allows the user
to distinguish between the different Tools that are being used in a robotic cell or on a production line.
The Tool-ID is reported through the Master module bitmap. See
EtherNet/IP bitmap and detailed I/O information.
One 4-Pin M12 D-Coded connector is provided on the Tool module for EtherNet/IP communications
interface with the downstream tooling.