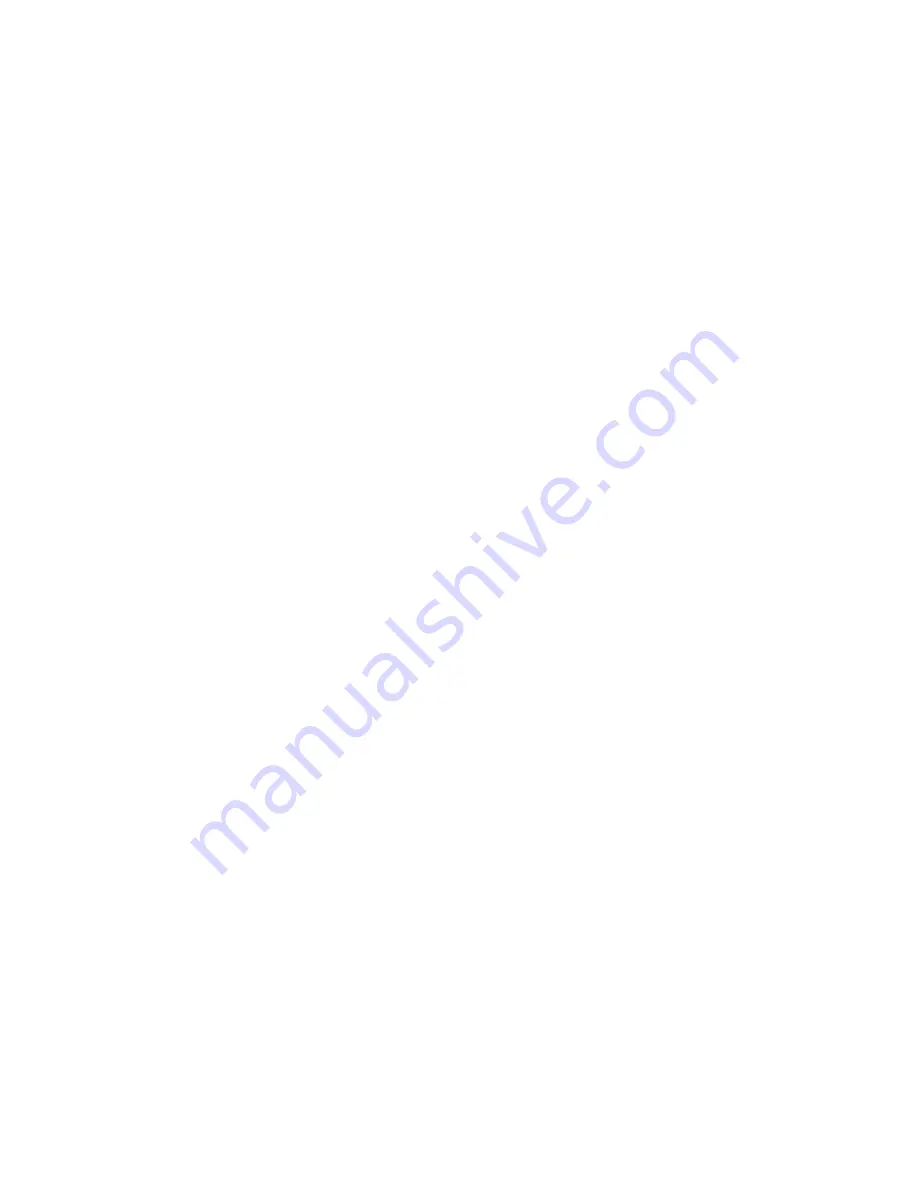
38
the other half of the worm wheel.
Note that it will be necessary to have the Keypad set to AutoConnect=NO (if initializing with the Keypad) or to set the AP
V2 driver / APCC (if initializing from the computer) to Unpark from Park 4. Once this operation is done remember to reset
to Unpark from Last Parked.
Do it twice a year…that should be enough.
TROUBLESHOOTING, TIPS AND SUPPORT
Troubleshooting and Tips
Additional troubleshooting questions are in the GTO Keypad or GTO Servo System manuals. Some of the issues
discussed in these manuals relate to mount communication issues whether you use the keypad or control the mount with a
planetarium program or
PulseGuide
™. Please refer to them.
The Declination (or R.A.) axis does not turn freely, even with the clutch knobs fully loosened.
The design of the clutches is such that spring loaded tips always maintain some friction against the worm wheel.
Consequently, the axes will never spin freely. Back the clutch knobs off by at least two or three full turns to more fully
disengage the clutches. There will always be some friction. The 1100GTO clutches can be fully tightened without worry.
The LED on the GTOCP4 Control Box changes from red to yellow and the motors stop or go out com
-
pletely (for control boxes shipped after 02-25-00).
1. The voltage of your battery has probably gone below 10.5 volts.
2. The current rating of your AC-DC power supply is too low.
Note:
The most common problems are due to inadequate power supply! Voltage must be measured while under load.
Additional explanation:
During slewing under load, the two motors draw up to 3 amps from a 12-volt source. This may
increase when the temperature approaches freezing or below. It is recommended that your supply be rated at a mini-
mum of 12 volts DC at 5 amps continuous. 12.3 to 16 volts with a capacity of 5 to 10 amps is recommended for best
performance. (Do NOT exceed a nominal 18 volt system.) See the Power Considerations section beginning on page
29)
If you also power other equipment (CCD cameras, dew heaters, etc.) from the same source (NOT recommended!), you
will need a supply capable of up to 10 amps. The more equipment you have, the more current capability you will need.
We always recommend giving the mount its own supply and using additional supplies for other equipment.
For portable applications, we recommend heavy-duty deep-cycle batteries designed for deep discharge applications
(i.e. marine, golf cart, fork lift, or wheel chair batteries).
3. The motors are overloaded, probably due to an unbalanced load on your mount.
Rebalance your telescope, and then press one of the N-S-E-W buttons to reset the keypad. Re-enter the last object
on your keypad and the scope will slew to the correct position. Even though your motors had stopped, the logic in the
control box retained the scope position in memory. As long as you didn’t change the pointing position of the scope, you
are still calibrated.
If the scope was moved during re-balancing, simply enter a nearby bright star on the hand controller, press GOTO and
allow the mount to finish slewing. You can then move the scope manually or with the N-S-E-W buttons to center the
star in the eyepiece, and press the #9 RECAL button. This will recalibrate the mount.
Additional explanation:
The GTO drive circuit includes logic for overload protection to prevent burning out the expen-
sive servomotors in case of severe overload on the two axes. The primary cause is an unbalanced load in R.A. If the
extra load opposes the motor rotation, the motor must work harder to track at the sidereal rate and the current will rise
to high levels. If the current exceeds the trip point for more than a minute, the logic will shut the motor off and tracking
stops. It typically takes about 4 lb. of unbalance to trip the overload, but a very heavy load of scopes, accessories and
counterweights on the mount can decrease this unbalance threshold.