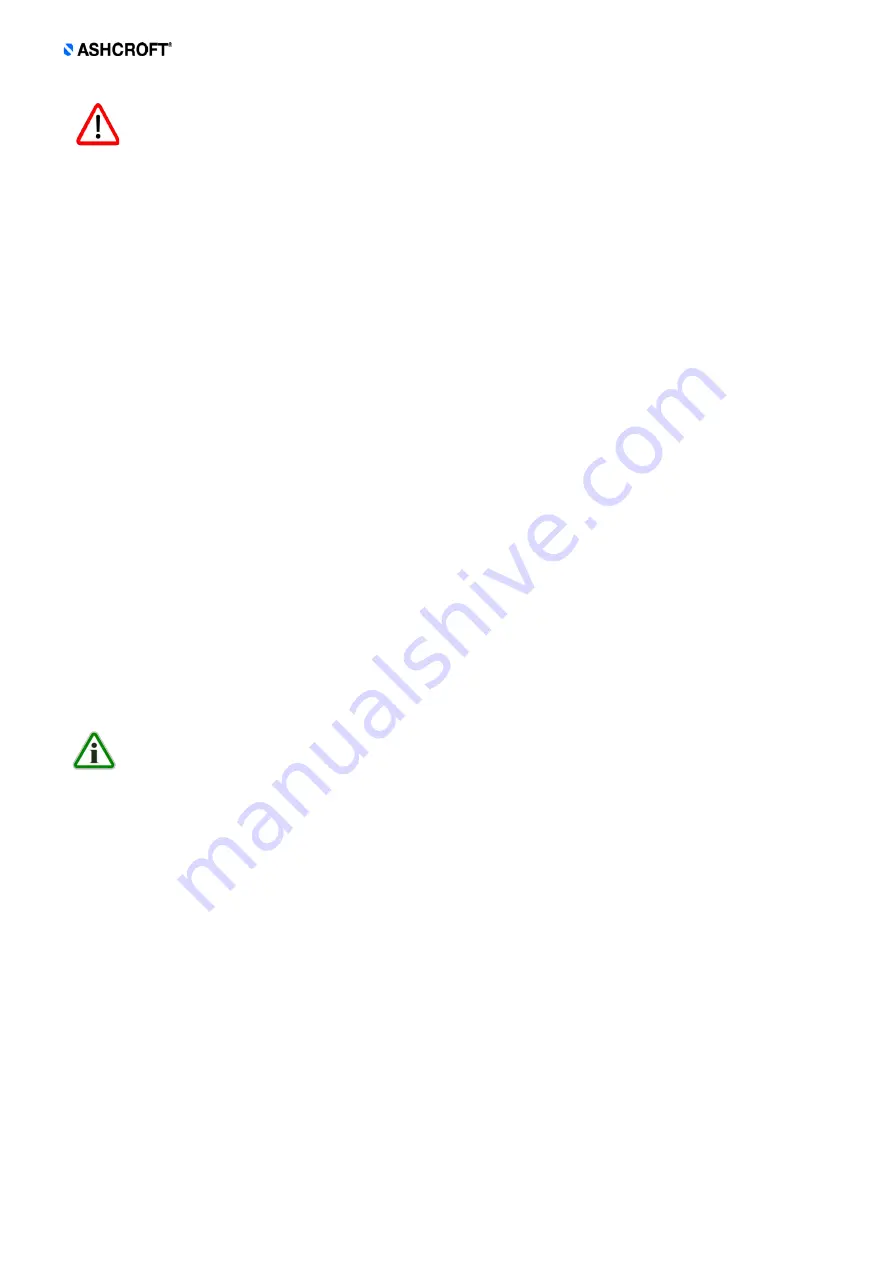
Page 16 of 22
8.4 Electrical connection
Take note of the electrical data in the EU design type test certification and the locally applicable
regulations and guidelines for installing and operating electrical plant in explosion risk areas (e.g.
EN 60079-14, etc.).
Connection to be undertaken by authorized and qualified specialist staff only.
The electrical connection of the device is to be undertaken in accordance with the relevant regulations of the VDE
and the regulations supplied by the local utilities company.
Disconnect the plant from the mains supply before wiring electrical connections.
Before operating the switch all conduit entries and/or junction boxes need to be closed according to the required
safety and electrical codes.
a. Standard product has two 1/2 NPT conduit holes with one permanent plug. 1/2 NPT conduit holes can
be modified or reduced with ATEX approved adapters.
b. Available ATEX approved cable glands can be used.
It is recommended that Teflon tape or other sealant be used on conduit, bushing, gland or plug threads to ensure
integrity of the enclosure.
Cable couplers, glands and conduit connectors must have the correct electrical approvals.
Always follow safety and electrical regulations when connecting these devices.
The system ground of the device is marked with a green coloured screw and/or by the ground symbol.
ATEX approved switches have an external ground screw that must be connected.
8.5 Starting up
A prerequisite for starting up is the proper installation of all measuring and control lines. All connection must be laid in
such a way that no mechanical forces can act on the device.
Before starting up, the tightness of the pressure connection must be checked.
8.6 Subsequent relocation of the level switch
Do not disassemble the device from the measuring point in order to mount it at another measuring
point without cleaning it first. There is a risk of mixing media with unpredictable chemical reactions
.
9
Maintenance
The devices are low maintenance. To ensure reliable operation and a long service life of the device, we nevertheless
recommend that the device is checked regularly. When carrying out maintenance work on the device, the storage
container must be depressurized, unintended starting up must be prevented.
The flameproof joints of the enclosures are not intended to be repaired.
9.1 Cleaning
Deposits of liquid residues and dirt must be removed from the stem/slide bar
Efficient sliding of the floats
Top/low level ring stopp (SEEGER
®
ring) tightness on the stem/slide bar to prevent incorrect tank levels
Functional tests
The exact test cycles must be adapted to the operating and ambient conditions. When various device components
interact, the operating instructions of all other devices must also be observed.
Check float for free movement
Check Reed contact by moving the float up and down