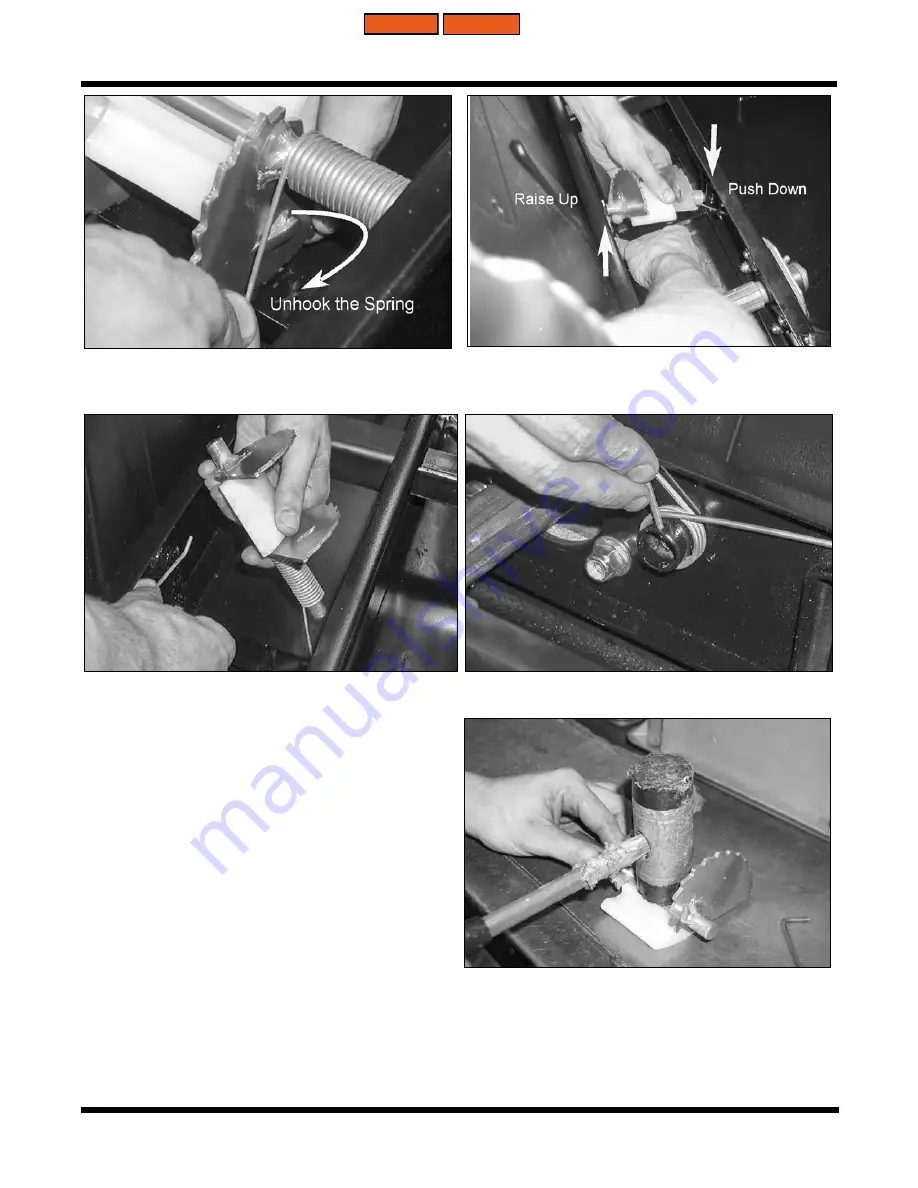
Wheels, Axles & Chains
Argo Service Manual
WA-14
3. Slip the one torsion spring off the cam, and remove the second torsion spring from the
frame assembly by removing the cotter pin that secures it.
Assembling the Chain Tensioner System (Semi-Self Adjust)
1. Place the tensioner block onto a work-
bench and position the slider block over
the shaft of the assembly.
2. With a soft faced mallet, tap the slider
block to snap it on to the shaft.
3. Slip a torsion spring over the welded
bushing in the frame, and secure with a
cotter pin.
4. Slip the second torsion spring on to the
shaft of the tensioner cam assembly.
MAIN INDEX
WA INDEX
Summary of Contents for All 6X6
Page 1: ...Printed in Canada 2022 01 01 All 8X8 MODELS All 6X6 MODELS SERVICE MANUAL 2022...
Page 2: ......
Page 252: ...TR 74 Argo Service Manual Transmission TR INDEX MAIN INDEX...
Page 255: ...TR 77 Argo Service Manual Transmission TR INDEX MAIN INDEX...
Page 268: ...TR 90 Argo Service Manual Transmission Press 101 01 Bearing onto shaft TR INDEX MAIN INDEX...
Page 271: ...TR 93 Argo Service Manual Transmission IDLER SHAFT ASSEMBLY TR INDEX MAIN INDEX...
Page 277: ...TR 99 Argo Service Manual Transmission TR INDEX MAIN INDEX...
Page 286: ...TR 108 Argo Service Manual Transmission TR INDEX MAIN INDEX...