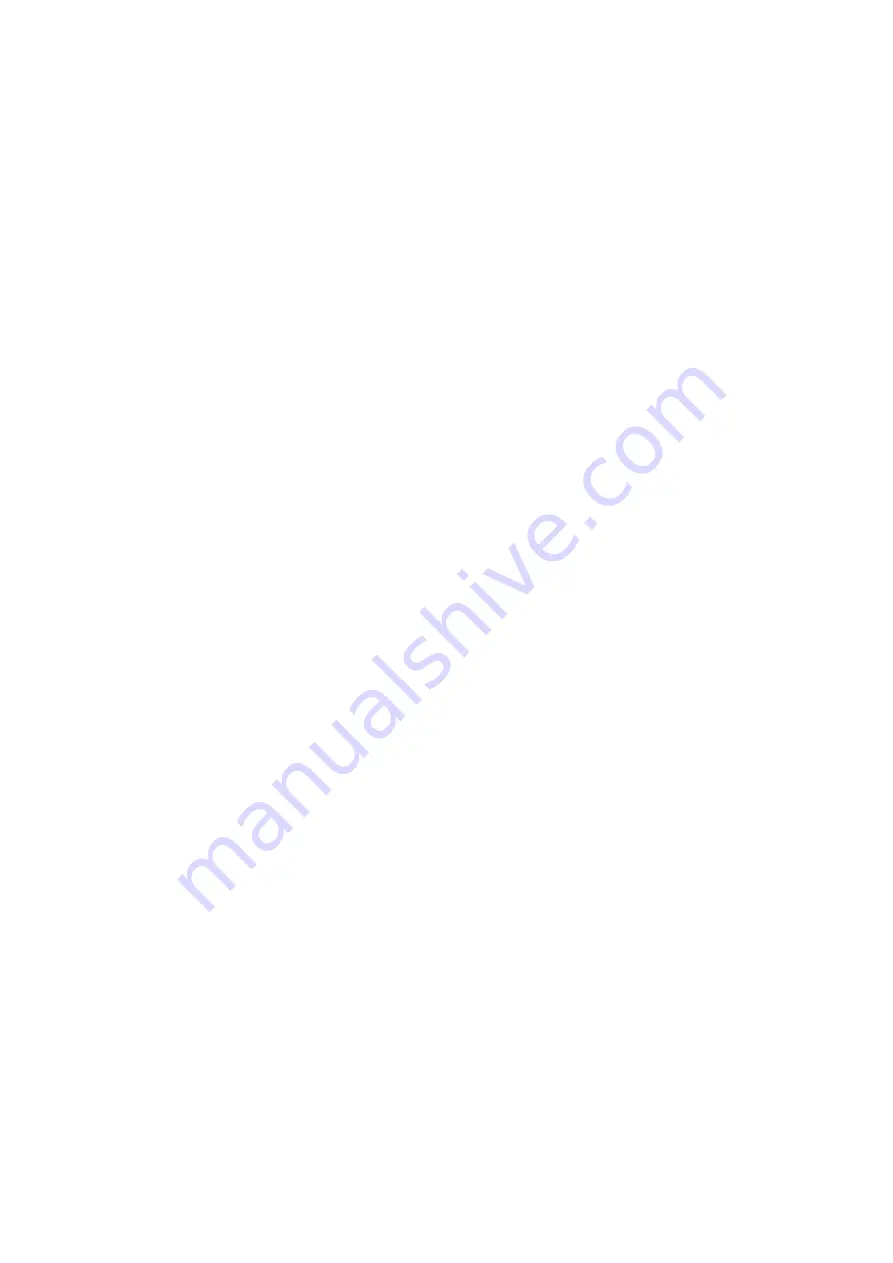
8
-
do not operate at the extremes of the operating curve: maximum head (discharge valve shut too tight) or maximum flow (total
absence of loss and lift in discharge circuit).
-
set the operating point for which the pump has been requested
-
check that there are no unusual vibrations or noises due to inadequate fixing or cavitation
avoid excessively short and/or frequent start-ups by adjusting the consent appliances
Motor power ; kW
0,75÷5,5
Max. no. starts/hour ; 2-4 poles
20 - 40
- check that temperature, pressure and characteristics of liquid match order specifications
7.4
USE
-
switch automatic control on
-
do not activate valves whilst the pump is in operation
-
risks of dangerous water hammer effects in case of sudden or improper valve actuation (only trained personnel should
operate valves)
-
completely empty and wash the pump before using a different liquid
-
isolate or empty the pump if the crystallization temperature of the liquid is the same or lower than the ambient temperature
-
stop the pump if the liquid temperature exceeds the maximum allowed temperature indicated in the general notes; if the
increase is of approximately 20%, check internal parts
-
close the valves in case of leaks
-
wash with water only if compatible from the chemical point of view. As alternative use an appropriate solvent that will not
generate dangerous exothermal reactions
-
contact the liquid supplier for information on the appropriate fire precautions
-
empty the pump in case of long periods of inactivity (in particular with liquids which would easily crystallize)
7.5
SHUTDOWN
-
disconnect the motor
-
before starting maintenance, turn off the suction and discharge valves
8
MAINTENANCE
-
all these maintenance operations must be performed under the supervision of qualified personnel
-
make periodic inspections (2 to 6 months depending on the type of liquid and the operating conditions) on the rotating parts
of the pump; clean or replace as necessary
-
make periodic inspections (3 to 5 months depending on the type of liquid and the operating conditions) on the functionality of
the motor control system; efficiency must be guaranteed
-
make periodic inspections (2 to 30 days depending on the type of liquid and the operating conditions) of the in- line and foot
filters as well as of the bottom valve
-
the presence of liquid below the pump could be a clue to pump problems
-
excessive current consumption could be an indication of impeller problems
-
unusual vibrations could be due to unbalanced impeller (due to damage or presence of foreign material obstructing its
blades)
-
reduced pump performance could be due to an obstruction of the impeller or damages to the motor
-
motor damages could be due to abnormal friction within the pump
-
damaged parts must be replaced with new original parts
the replacement of damaged parts must be carried out in a clean dry area
8.1
DISMANTLING
Tools required:
Open end wrenches CH6 , CH10 , CH13 , CH17 , CH19, Hex key wrench CH6, Phillips screw driver
Right handed nuts and bolts
- all these maintenance operations must be performed under supervision of qualified personnel
- cut off the power supply from the motor and disconnect the electrical wiring; pull the wires out from the terminal
box and isolate their extremities accordingly
- close the suction and discharge valves and open the drain valve
- use gloves, safety glasses and acid-proof overalls when disconnecting and washing the pump
- disconnect the piping and leave enough time for the residual liquid to exit the pump body and atmospheric air to
fill the empty volume
- wash the pump before carrying out any maintenance work
- do not scatter the liquid in the environment
- before attempting to dismantle the pump ensure that its motor is disconnected and that it may not be started
accidentally
- before the inspection, check that you have spare O-rings ready to hand for re-installing at the end of operations
Summary of Contents for ZMR 02.30
Page 2: ...2 1 DISASSEMBLING SEQUENCE ...
Page 16: ...16 ...
Page 17: ...17 ...
Page 18: ...18 ...
Page 19: ...19 ...