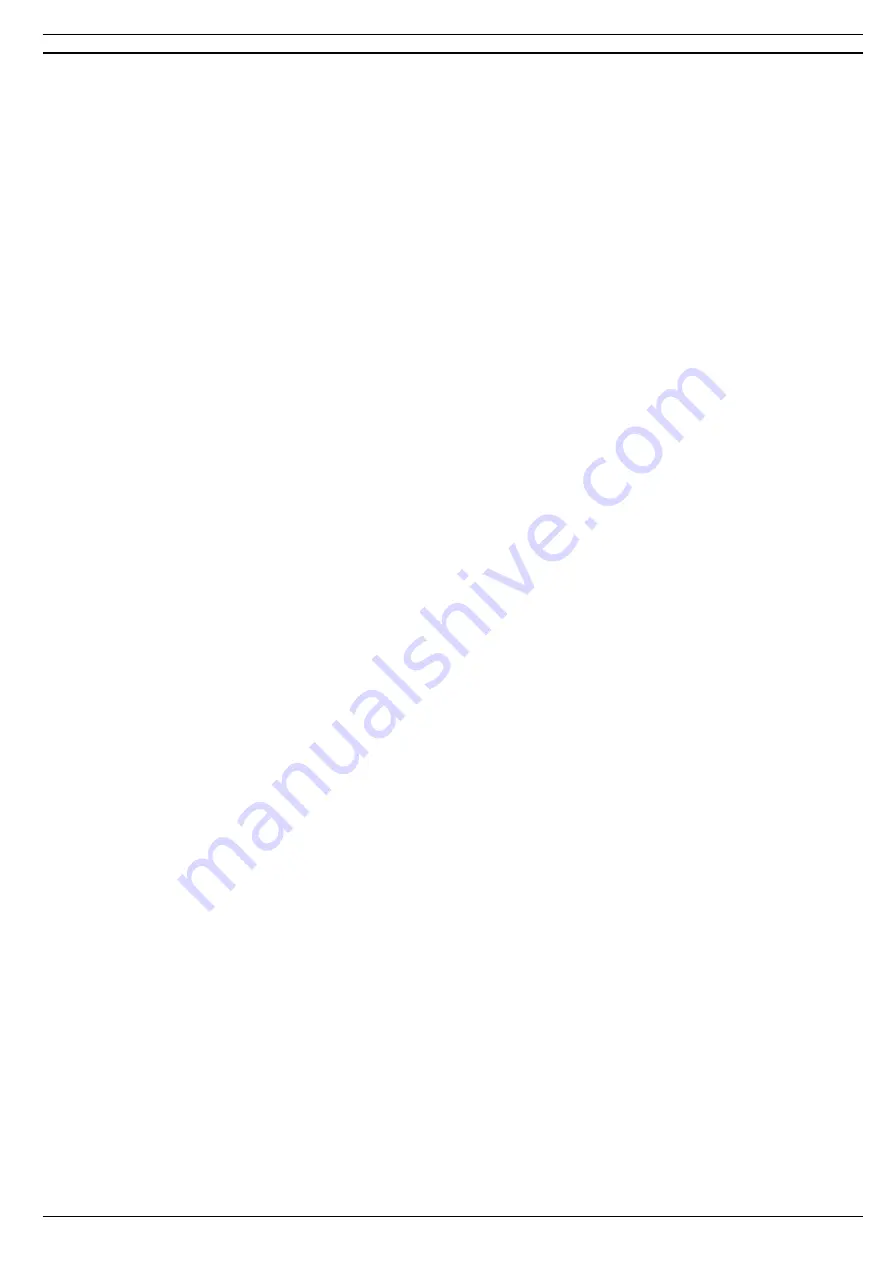
11
10
GUARANTEE TERMS
1. ARAG s.r.l. guarantees this apparatus for a period of 360 days (1 year) from the date of sale to the client user (date of the goods delivery note).
The components of the apparatus, that in the unappealable opinion of ARAG are faulty due to an original defect in the material or production
process, will be repaired or replaced free of charge at the nearest Assistance Center operating at the moment the request for intervention is made.
The following costs are excluded:
-
disassembly and reassembly of the apparatus from the original system;
-
transport of the apparatus to the Assistance Center.
2. The following are not covered by the guarantee:
-
damage caused by transport (scratches, dents and similar);
-
damage due to incorrect installation or to faults originating from insufficient or inadequate characteristics of the electrical system, or to alterations
resulting from environmental, climatic or other conditions;
-
damage due to the use of unsuitable chemical products, for spraying, watering, weedkilling or any other crop treatment, that may damage the
apparatus;
-
malfunctioning caused by negligence, mishandling, lack of know how, repairs or modifications carried out by unauthorized personnel;
-
incorrect installation and regulation;
-
damage or malfunction caused by the lack of ordinary maintenance, such as cleaning of filters, nozzles, etc.;
-
anything that can be considered to be normal wear and tear.
3. Repairing the apparatus will be carried out within time limits compatible with the organizational needs of the Assistance Center.
No guarantee conditions will be recognized for those units or components that have not been previously washed and cleaned to remove residue of
the products used;
4. Repairs carried out under guarantee are guaranteed for one year (360 days) from the replacement or repair date.
5. ARAG will not recognize any further expressed or intended guarantees, apart from those listed here.
No representative or retailer is authorized to take on any other responsibility relative to ARAG products.
The period of the guarantees recognized by law, including the commercial guarantees and allowances for special purposes are limited, in length of
time, to the validities given here.
In no case will ARAG recognize loss of profits, either direct, indirect, special or subsequent to any damage.
6. The parts replaced under guarantee remain the property of ARAG.
7. All safety information present in the sales documents regarding limits in use, performance and product characteristics must be transferred to the
end user as a responsibility of the purchaser.
8. Any controversy must be presented to the Reggio Emilia Law Court.