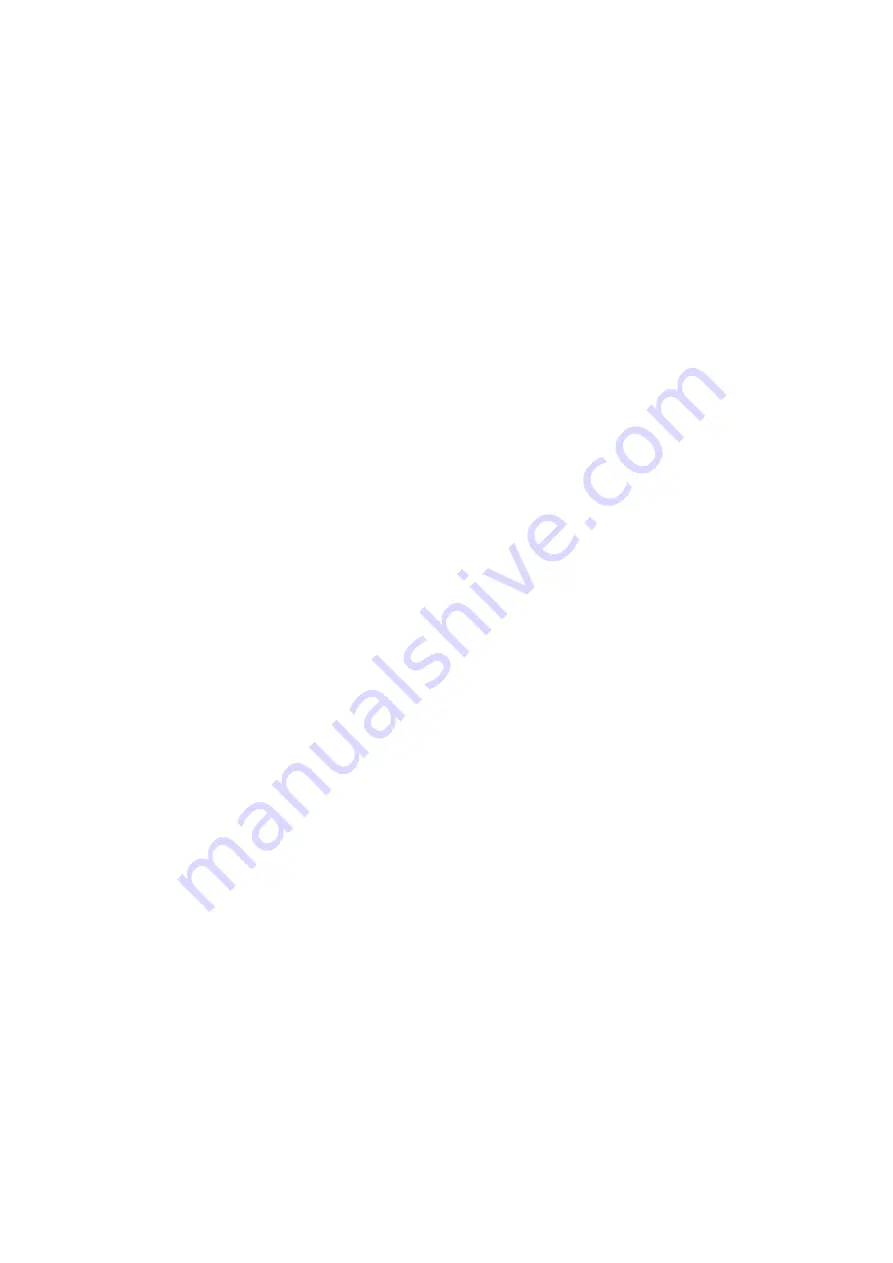
ASC+ System Auto Split Charge & Engine Start Protect
User Guide and Installation Instructions
Document No 13362 Issue 04
Page 10 of 21
Step 7
•
Connect the blue wire from the 6 way loom (82516) to a point which is “live” when the
ignition switch is on. Normally cct 15
Note
: The blue wire “ignition” must be connected to a source which is guaranteed live
when the vehicle ignition is switched on, such as a direct connection to the keyswitch, or
to its own dedicated supply. Do not connect to a supply shared with any other device
behind a fuse. This signal is used to inhibit battery isolation when the engine is running.
Step 8
•
Connect any permanent loads to the permanent supply provided from the controller –
3 amps maximum see Figure 2. The permanent feed output may be used for low
current devices that must remain powered when the battery is isolated; e.g. clock,
radio, central locking.
Note: that any connected devices will continue to drain the battery.
Step 9
Testing the assembly
•
Momentarily press the “Engine Battery On/Off” switch, the primary contactor should
close and the engine loads should now be powered, the “Engine Battery On/Off” LED
should be on.
•
Press and hold in the “Engine Battery On/Off” switch for a minimum of 3 seconds after
which the primary contactor will open and the engine loads will be isolated (the switch
LED should flash whilst the switch is pressed).
•
When the engine loads are isolated the “Engine Battery On/Off” LED will continually
give a brief flash to indicate that the system is powered.
•
Press the “Battery Link” switch, the secondary contactor should close and link the
Main & Auxiliary batteries together. If there is no charging voltage present the
contactor with remain closed for 60 seconds, during this period the “Battery Link”
switch LED will flash.
This completes the installation and testing.