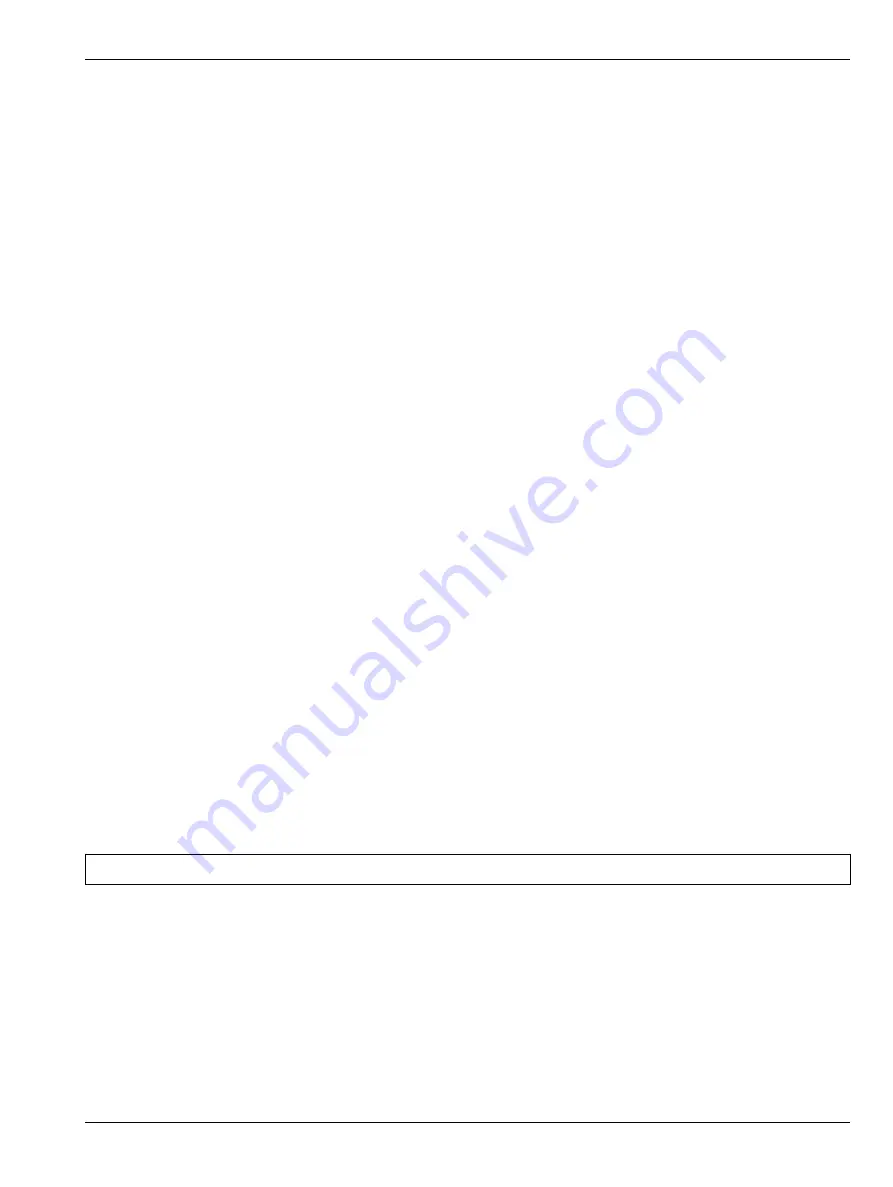
Chapter 3 — Performance Verification
3-10 Pulse Modulation Tests
MG3702xA MM
PN: 10370-10372 Rev. B
3-37
Pulse Power Accuracy
The following procedure describes the measurement of the pulse power accuracy of the MG3702xA's pulse
modulated RF Output. The accuracy is tested with a 1 µs and a 0.5 µs pulse width.
Test Setup
1.
Disconnect the MG3702xA's RF coaxial cable from the front of the unit.
2.
Set up the equipment as described in
, then perform
“.
Test Procedure
1.
Set up the MG3702xA as follows:
a.
Preset the instrument by pressing
Preset
. After preset, the CW menu is displayed.
b.
Turn RF output OFF.
c.
Press
Edit Frequency
to open the current frequency parameter for editing.
d.
Set F0 to the first applicable/next frequency in the test record.
e.
Press
Edit Level
to open the current power level parameter for editing.
f.
Set L0 to the maximum specified leveled output power level for the instrument being tested
(refer to
“MG3702xA Technical Data Sheet”
g.
Connect a fixed attenuator with the proper attenuation value to the MG3702xA
RF Output
(refer to
), and then connect the RF coaxial cable from the
Channel 1
Input
of the Oscilloscope to the fixed attenuator.
h.
Turn RF output ON.
i.
Press
Modulation | Internal
to select the Internal source.
j.
Press
PRI
and enter 4 µs.
k.
Press
W1
and enter 1 µs (or 0.5 µs for <1 µs test).
l.
Press
Off
to turn the internal pulse mode off.
2.
Set up the oscilloscope as follows:
a.
Press the
Source
button (near the trigger) until
Free Run
is illuminated.
b.
Select the
Scale
button at the lower left corner of the display and set the scale to 20 mV/div.
c.
Set the Offset so that the trace is centered on the display (typically 150mV), and select
Close.
d.
Select the
Amplitude
button and then the
Vavg
button (on the left hand side of the display),
then touch
OK
to close.
3.
Read the measured result on the display and record the result as V
ref
in the test record.
4.
On the MG3702xA, press
On
to turn pulse modulation ON.
5.
On the oscilloscope, press the
Source
button (near the trigger) until
Left Module
is illuminated.
6.
Set up the oscilloscope as follows:
a.
Press the
Clear Display
key. Allow the oscilloscope to sample the signal and wait for a
clearly defined waveform to appear on the display.
Note
Use the scroll bar to locate the V avg button.
Summary of Contents for MG3702xA Series
Page 4: ......
Page 5: ......
Page 8: ...TG 8 PN 10370 10372 Rev B MG3702xA MM ...
Page 24: ...1 12 Test Equipment List Chapter 1 General Information 1 10 PN 10370 10372 Rev B MG3702xA MM ...
Page 42: ...2 5 RF Deck Assemblies Chapter 2 Functional Description 2 18 PN 10370 10372 Rev B MG3702xA MM ...
Page 120: ...5 5 Troubleshooting Tables Chapter 5 Troubleshooting 5 24 PN 10370 10372 Rev B MG3702xA MM ...
Page 182: ...Index 4 PN 10370 10372 Rev B MG3702xA MM ...
Page 183: ......