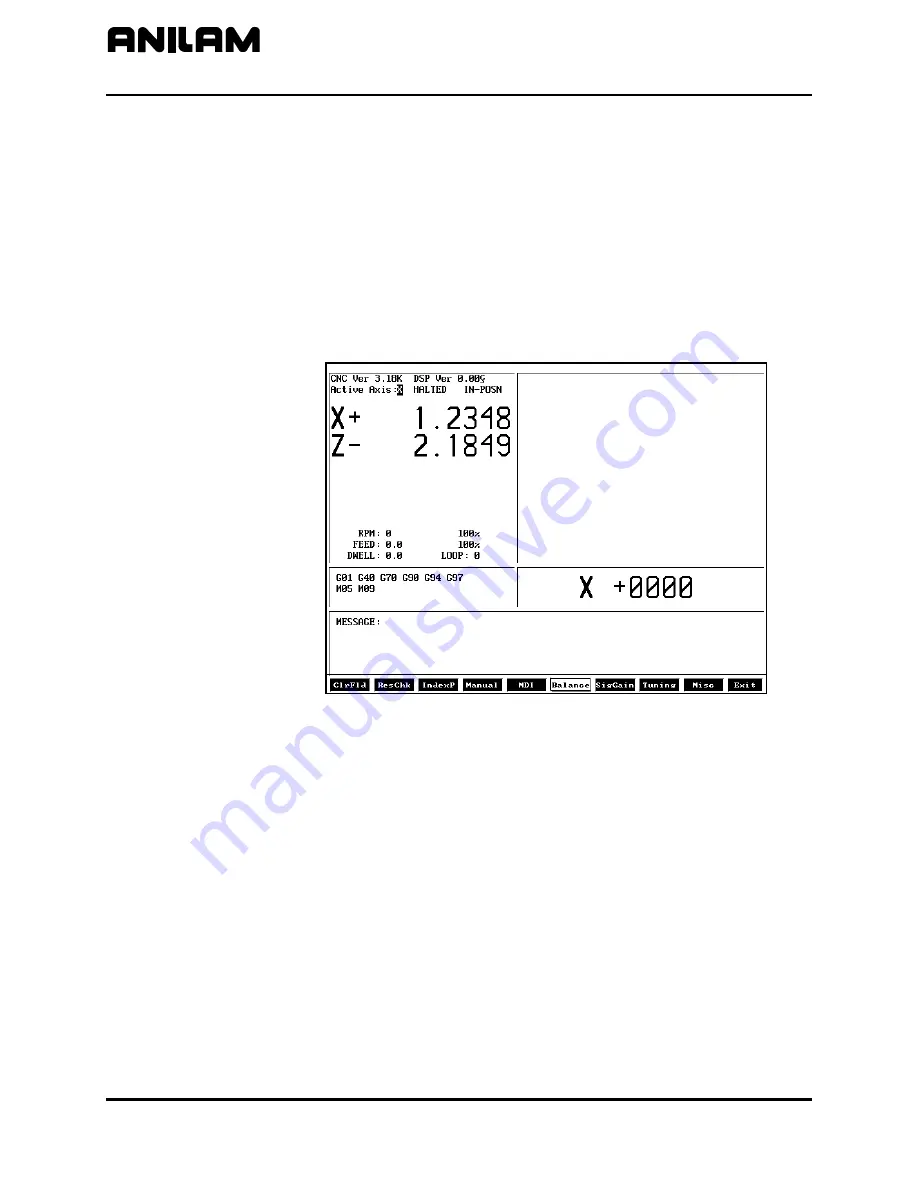
CNC Motion Setup/Testing Utility
P/N 70000634A
All rights reserved. Subject to change without notice.
23-December-05
14
Motion Setup and Testing (MST)
1. At the Software Options menu, select
Motion Setup/Testing
.
2. Press and release the
E
-
STOP
button.
3. Press the
SERVO RESET
to energize the system.
4. Select an axis to be tested by pressing the corresponding key on the
keypad (
X
,
Z
, or
S
).
5. Press
Balance
(
F6
) to perform the balance test on the selected
amplifier (axis) and display the balance test screen. Refer to
Figure 7
.
4200BALANCE
Figure 7, Balance Test Screen
6. Use the keypad up and down
ARROW
keys to change the axis offset
until the selected axis reads: +0000. Use the left and right
ARROW
keys to change the Offset value.
7. To cancel the balance test, press
MANUAL
(
F4
); otherwise, press
SigGain
(
F7
) to perform the signal gain test for the selected amplifier.
Summary of Contents for 4200T CNC
Page 1: ...www anilam com ...