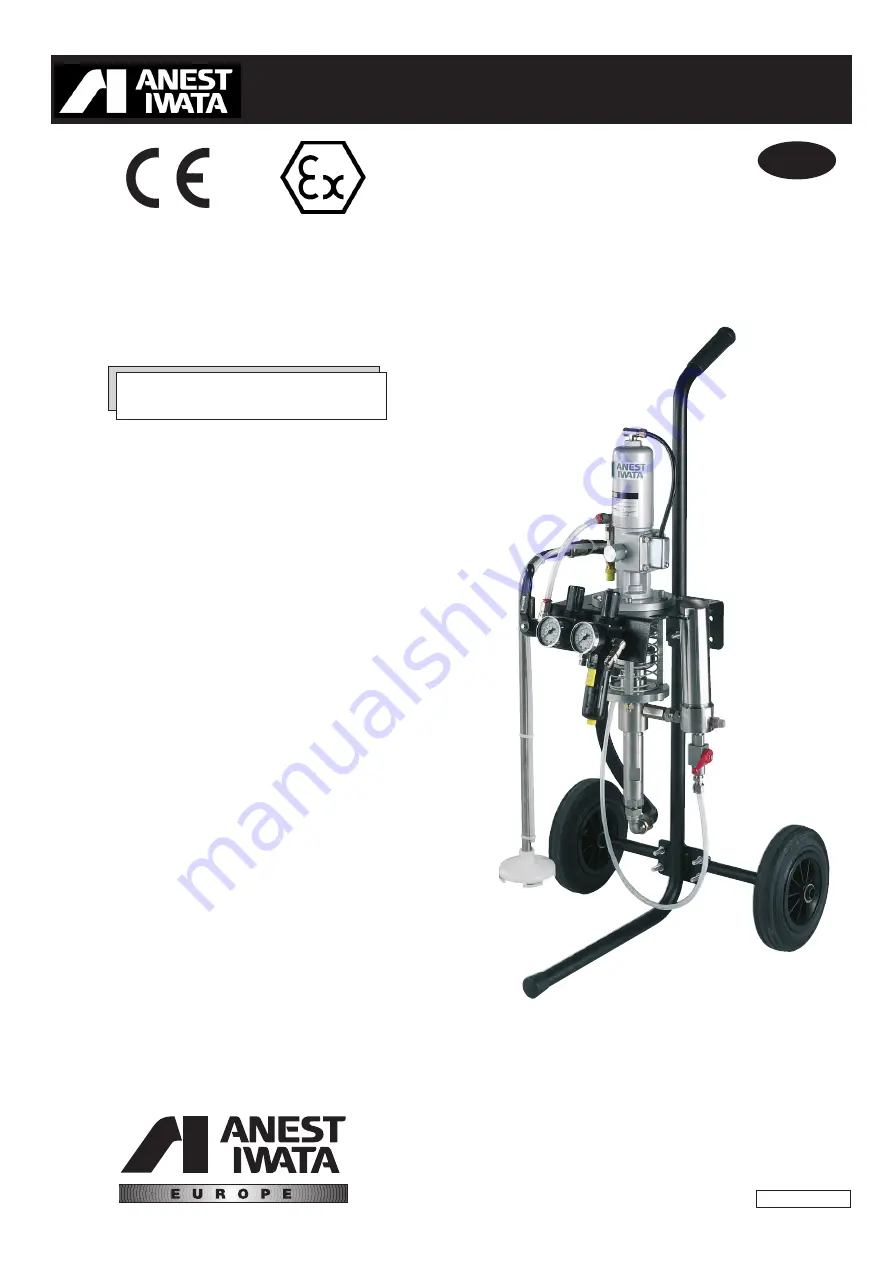
Use and maintenance manual
MUL
MUL
TI SPRA
TI SPRA
Y UNIT
Y UNIT
GB
ME113NERev.13
MSU-113 N
MSU-113 N
ANEST IWATA Europe s.r.l.
46, Corso Vigevano
10155 Torino - Italia
Tel. +39 011-24 80 868
Fax +39 011-85 19 44
www.anest-iwataeu.com
e-mail: [email protected]