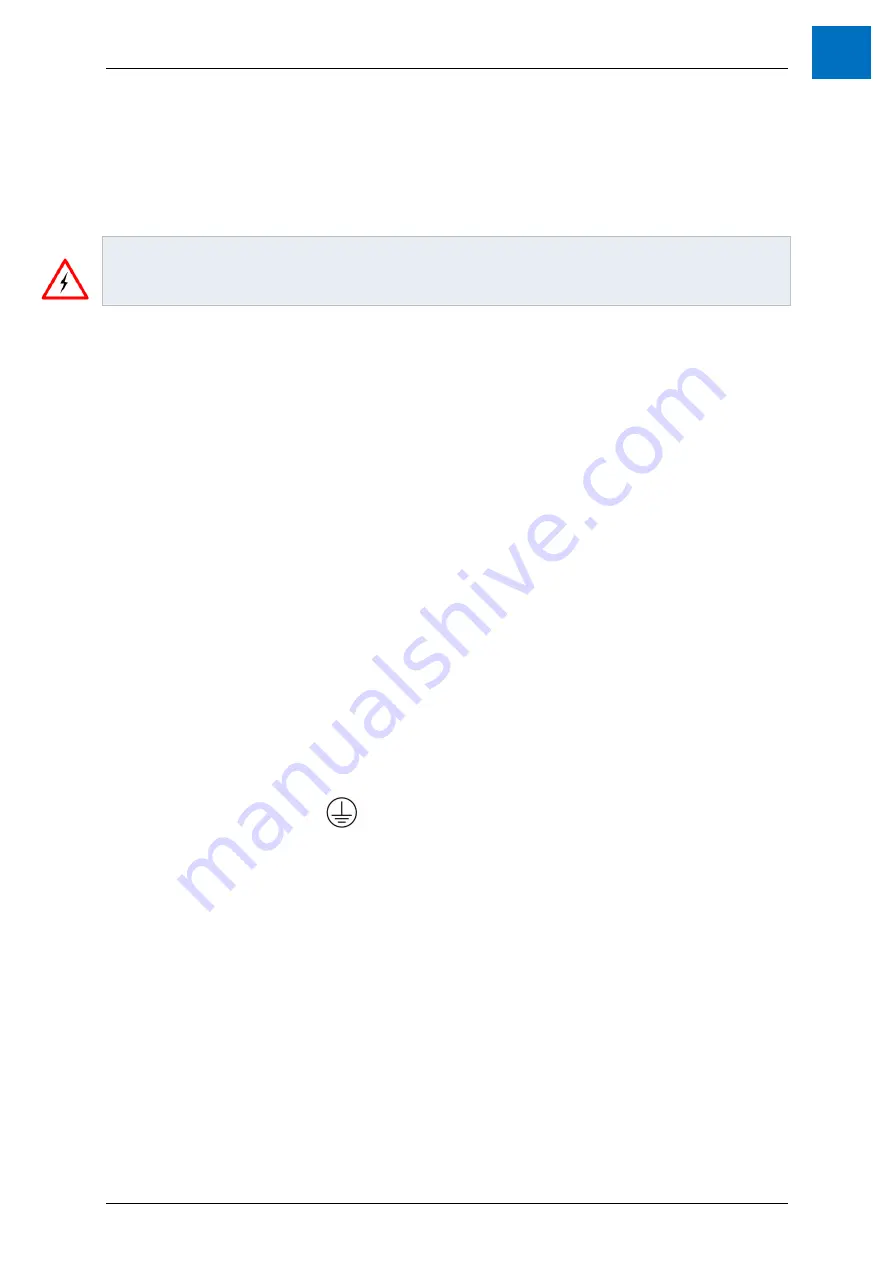
Power Wiring
ANCA Motion
D-000129 Rev 09
63
5
Power Isolation
5.3.1
Power isolation is required to prevent risk of electric shock during maintenance and assembly operations. Ensure
isolation switches, isolation circuit breakers and contactors meet the requirements and applicable safety
regulations of the region of operation. Turn the Main Disconnect mains isolator switch to the Off position and
follow the appropriate lockout procedure when installing or maintaining the drive. See Isolator Ratings given in
DANGER HIGH VOLTAGE
- The working DC Bus is live at all times when power is on. The Main Isolator feeding
the PIU must be switched to the
Off
position at least 15 minutes before any work is commenced on the unit. The
operator must check the DC Bus is discharged and isolated from mains supply with a tested working voltage
measuring instrument prior to disconnecting any connectors or exposing any part of the DC Bus.
Mains Contactors
5.3.2
When the AMD5x Passive Infeed Unit (PIU) is connected directly to a 3 phase mains AC supply with no isolation
contactors, the Drive Array DC Bus & Servo Drive motor armature cable outputs are constantly at a high voltage
even when the PIU is not enabled. The PIU does not include a method to isolate the AC mains supply.
Customers should conduct a risk assessment according to the Safety of Machinery Directive or other relevant
standard to determine if contactor(s) are required, and how they should be coupled with EMERGENCY OFF
functions to provide electrical isolation of output power.
It is recommended that at least one isolation contactor be used on the three phase AC mains supply to the
Passive Infeed Unit. The contactor(s) can provide a safe and reliable method of isolating the Drive Array DC Bus
& Servo Drive motor armature cable outputs, from the line supply. See Contactor Ratings given in
5.4
Grounding
Earth and ground are synonymous; where earth is used in Europe, Australia and New Zealand and ground is
used in the US and Canada.
A grounding system has three primary functions: safety, voltage-reference, and
shield termination. The safety function is required by local regulations and is designated as the Protective Earth.
Signal and control circuits are typically grounded at various points with the ground forming the common voltage
reference. The shield on motor cables reduces emissions from the drive, and correct shield grounding prevents
electrical noise interference to control circuits.
The Protective Earth (PE) Connection from the mains supply eliminates shock hazards by connecting the
AMD5x PIU and Drive, and cabinet parts at same earth potential. The PE also conducts fault currents to ground
until the safety device (fuse or circuit breakers) disconnects the drive from the mains.
Symbol for Protective Earth (PE)
The mains supply protective (PE) wire must have a cross sectional area equal to 10mm
2
(copper conductors), or
a second earthing conductor of the same cross-sectional area as the original earthing conductor must be added.
The correct mains supply protective (PE) wire size must
be used to minimise PIU and Drive touch current.
On the PIU, the mains supply PE is connected to X2 plug and the location is also identified by the PE symbol on
the sheet metal.
Summary of Contents for AMD5x Series
Page 12: ......