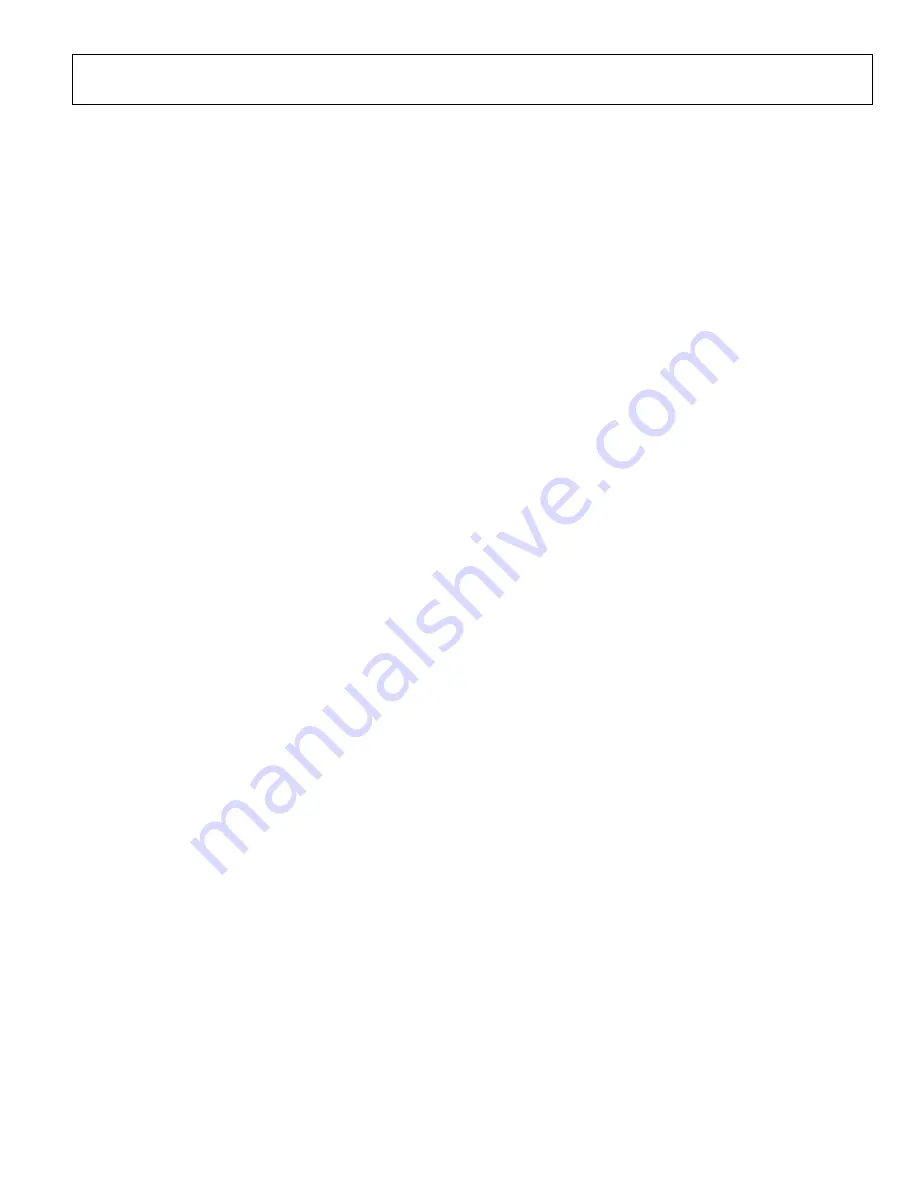
ADuCM310 Hardware Reference Manual
UG-549
Rev. C | Page 23 of 192
Chopping is a common method of offset elimination on input buffers to ADCs.
Chopping requires 2 × ADC conversions per measurement of a buffered ADC input channel.
For example, assume that the input buffer is two input pairs: positive (+) and negative (−) input. V
IN
applied is 100 mV and the offset on
the buffer is 500 µV. Normally, the ADC measures V
IN
+ V
OFFSET
and reports 100.5 mV when the buffer is enabled. With chopping enabled,
the first ADC sample measures V
IN
+ V
OFFSET
and reports 100.5 mV.
For the second ADC sample of this channel, with chopping enabled, the input pairs are switched and the voltage measured by the ADC is
V
IN
− V
OFFSET
= 99.5 mV
Averaging the two results provides the correct result of 100 mV.
To average ADC measurements when the input buffer is enabled, sample an even number of times (that is, 2×, 4×, 6×, and so on).
Auto-Zero Mode
Auto-zero mode does not require averaging so a single ADC measurement gives an accurate result. Signal-to-noise performance of auto-
zero mode is slightly degraded compared to chop mode (see Table 1 of the
data sheet for more details).
ADC INTERNAL CHANNELS
Temperature Sensor Settings
The
provides a voltage output from an on-chip band gap reference that is proportional to the absolute temperature of the low
voltage die. This voltage output is routed through the front end of the ADC multiplexer (effectively, an additional ADC channel input),
facilitating an internal temperature sensor channel that measures die temperature.
The internal temperature sensor is not designed for use as an absolute ambient temperature calculator. The intended use is as an
approximate indicator of the temperature of the
low voltage analog die.
An ADC temperature sensor conversion differs from a standard ADC voltage. The ADC performance specifications do not apply to the
temperature sensor.
When the temperature sensor channel is selected, the ADC update rate must be <80 kSPS.
•
The ADC automatically changes the ADC update rate to 80 kSPS when the temperature sensor, AV
DD
/2, or IOV
DD
/2 input channel is
selected. If a different ADC sampling rate is required for other channels after the conversion on any of these three channels is
completed, the ADCCNVC register must be updated.
•
Note that when the sequencer is enabled and includes any of these three channels, the value in the ADCCNVC does not change and
the ADC sampling rate does not change.
The temperature sensor settings are as follows.
To enable the temperature sensor on the ADC, set ADCCHA[12:0] = 0x1116.
To calculate the die temperature, use the following formula:
T
−
T
REF
= (
V
ADC
−
V
TREF
) ×
K
where:
T
is the temperature result.
T
REF
is 25°C.
V
ADC
is the average ADC result from two consecutive conversions.
V
TREF
is the ADC result in millivolts that corresponds to
T
REF
= 25°C. The user must measure this in their own application because this
value varies from device to device. The typical value used for demonstration purposes is 1290 mV.
K
is the gain of the ADC in temperature sensor mode. Determine the gain by performing a two-point temperature calibration, because
this value varies from device to device. The typical value used for demonstration purposes only is 4.394 mV/°C.
This corresponds to 1/V TC.
Using the default values from the data sheet without any calibration, the equation becomes the following:
T
− 25°C = (
V
ADC
− 1290) × 1/
K
Therefore, assuming V
ADC
at 25°C = 1290 mV and the slope mV/C as 4.394mV/°C,
T
= ((
V
ADC
− 1290)
/
4.394) + 25
where
V
ADC
is in millivolts.
See the latest version of the
data sheet for the most up to date figures.