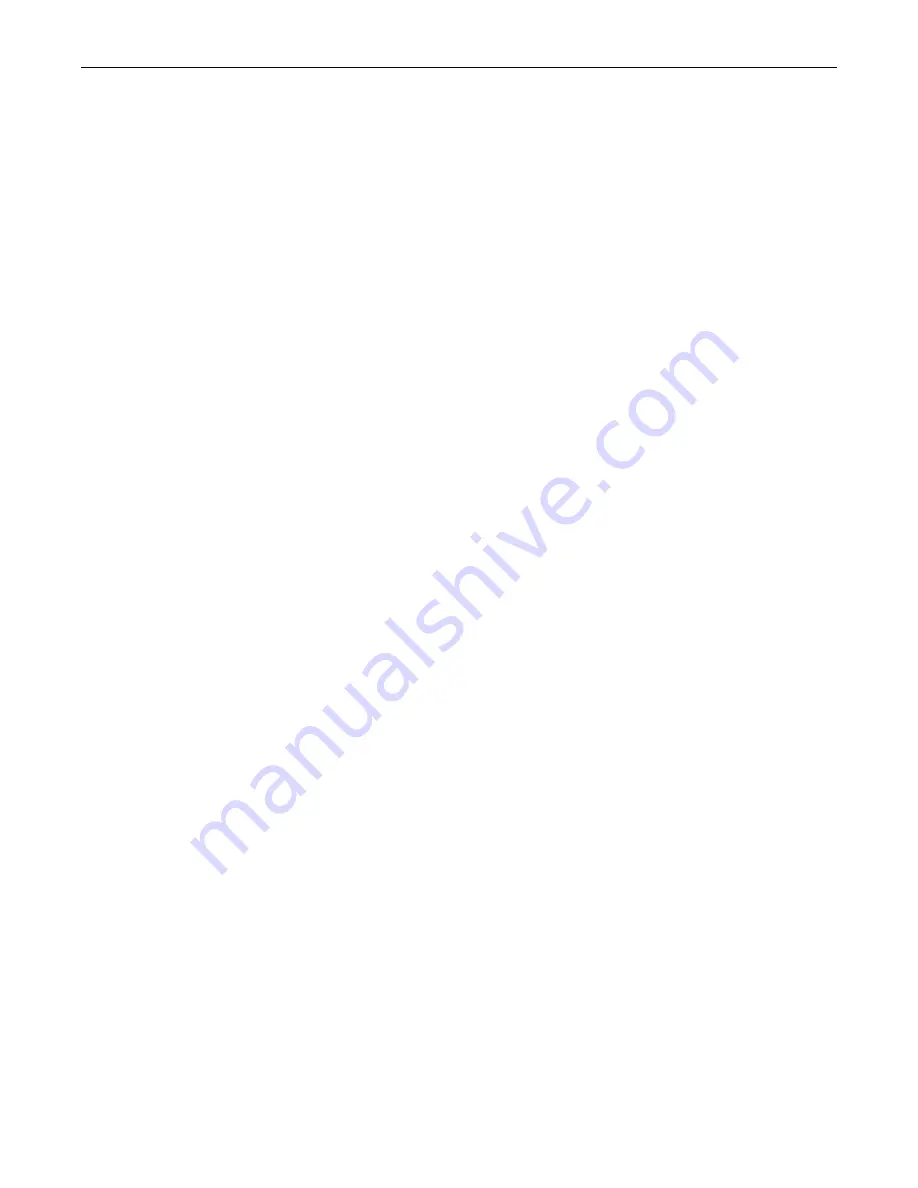
Amiad Water Systems | 2019
TEQUATIC™ PLUS F-150 Filter, C-series Skid
14
Installation
2.5.5 Feed Pump
The filter skid is designed to operate with a constant feed pressure between 30 and 80 psi that is
maintained as flow changes with minimal pressure variation. In the case where this type of feed water
is not available a dedicated feed pump should be used. The feed pump should be pressure controlled
using a VFD with a pressure sensor and a closed loop, PID feedback system. The filter skid will provide
a dry contact to control the on/off function of the feed pump but the speed control must be self
contained in the feed pump VFD PID software.
Below are the design considerations that must be addressed when building a feed pump skid.
•
The pump selection should be capable of delivering 130% of the desired filtrate flow rate while
maintaining a minimum of 30 psi inside the filter housing.
•
Pressure drop from the feed pump to the filter skid must be taken into account when sizing the
feed pump.
•
In the case of multiple filters fed by a single feed pump reduce the feed pump flow requirement
by 5% for each additional filter. It is recommended that a maximum of 4 filters be served by
a single feed pump. The feed pump flow capacity can not drop below 110% of the combined
filtrate flow rates.
•
The feed pump VFD should have inputs for a remote on/off command. The command will be given
by a dry contact within the filter skid control system; closed = on, open = off.
•
The feed pump VFD should have adjustable ramp-up and ramp-down functions. The recommended
initial values are Ramp-up = 30 seconds, and Ramp-down = 5 seconds. The pump should build
pressure slowly but, be able to drop pressure quickly if flow stops.
•
The feed pump VFD must have an analog input to reference a pressure sensor and associated PID
function to maintain a pressure set point.
•
Depending on the VFD and pressure sensor combination, the VFD likely needs the ability to
invert and bias the output speed such that the pressure versus speed are inverse functions.
•
The proportional gain should be set high enough to accurately reach the setpoint but, set low
enough to prevent oscillations (hunting) near the set point.
•
The pressure set point must be adjustable for tuning the desired pressure.
•
The feedback pressure sensor should be located as close to the pump outlet as possible to provide
accurate pressure control.
Any feed pump setup must be tested prior to installing a filter. The testing should include verification
the VFD can maintain a setpoint, verification the pump speed can adjust as flow requirements change,
and verification the VFD can accept the on/off commands from the filter skid.