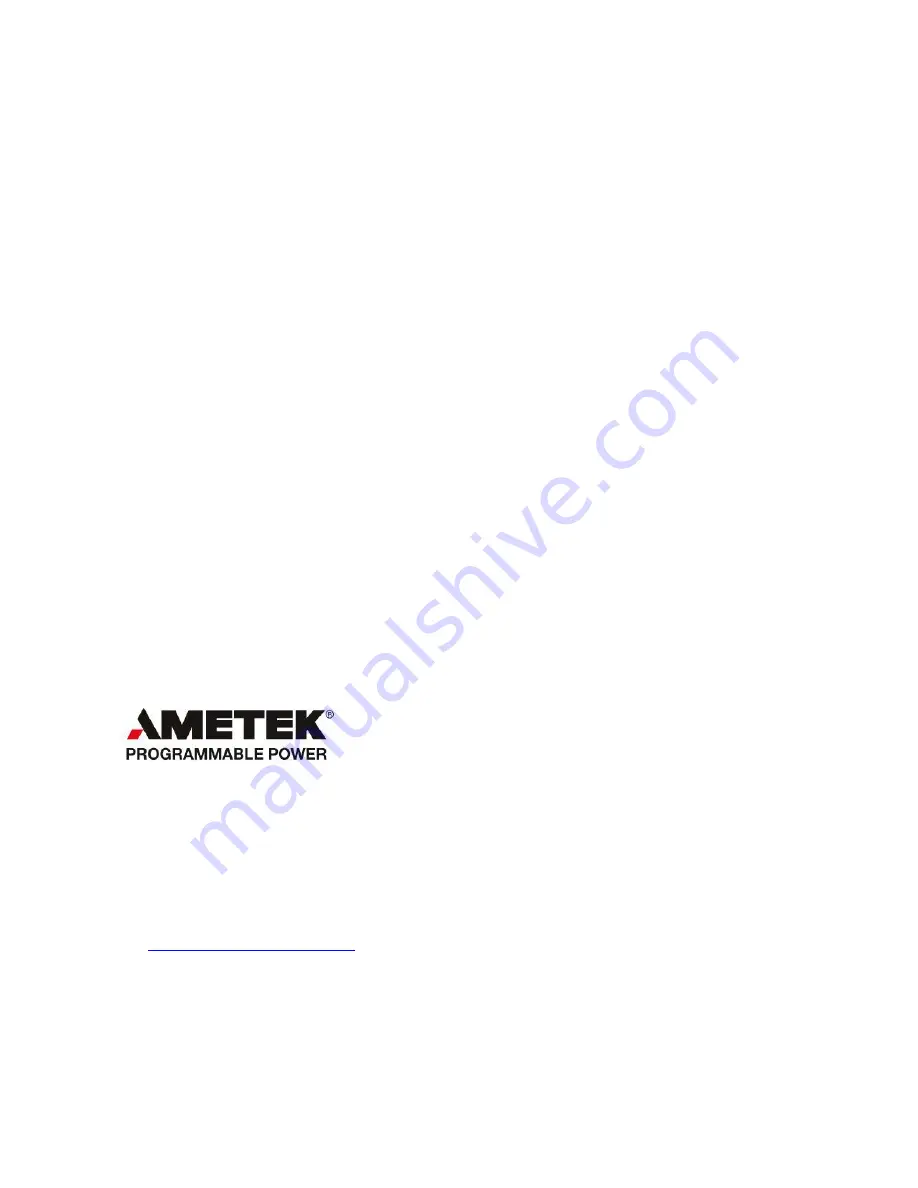
Contact Information
Telephone: 800 733 5427 (toll free in North America)
858 450 0085 (direct)
Fax: 858 458 0267
Email:
Domestic Sales: [email protected]
International Sales: [email protected]
Customer Service:
Web:
www.programmablepower.com
SmartWave™
Switching
Amplifier
Operation Manual
March 2011
Document No. M161668-01 Rev E
This manual covers models:
SW 5550AE
SW 3700AE
SW 1850AE
Summary of Contents for SW 1850AE
Page 2: ......