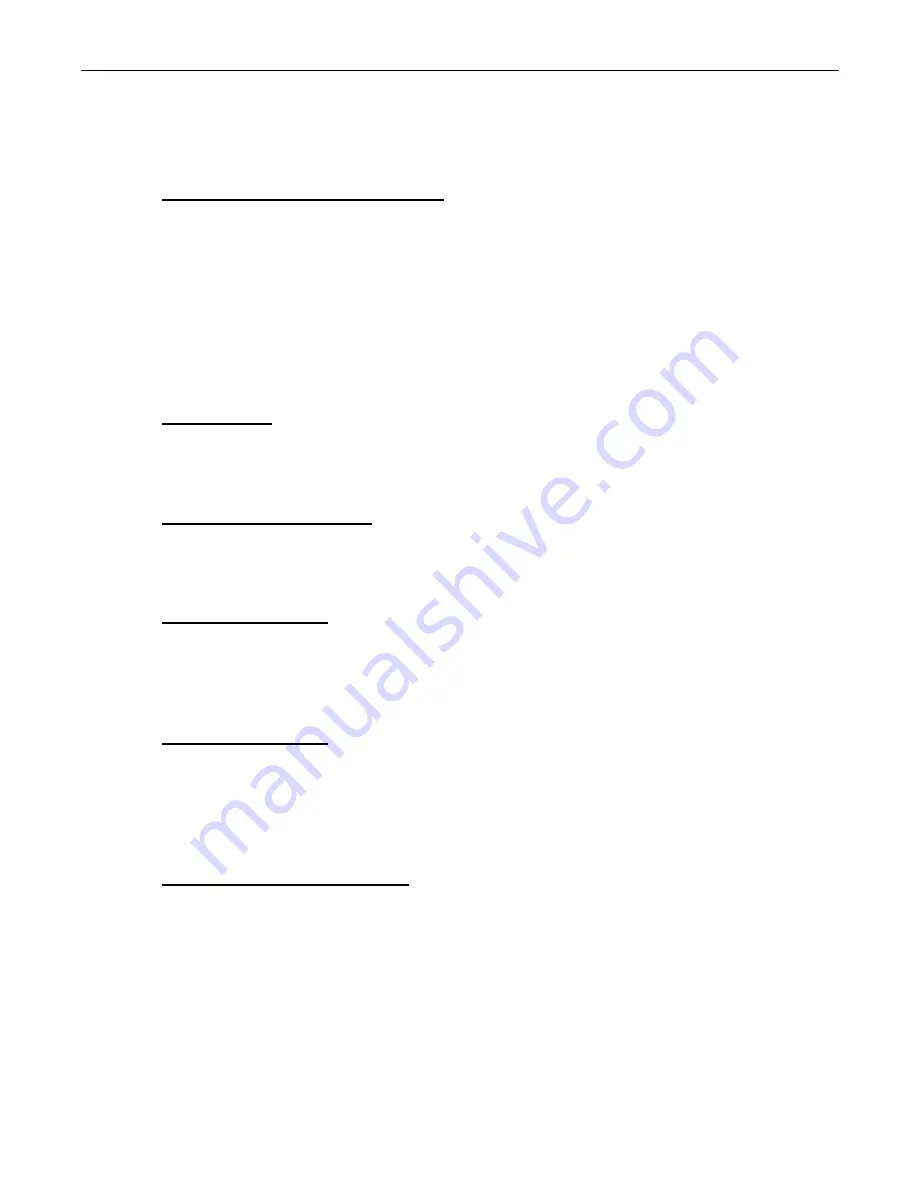
2-2 CURING CHAMBER CONTROLS
Please refer to the
9050,9051,9060,9061,9080,9081 Controller
manual for detailed
instructions on the operation of the temperature controller.
Drain Cylinder/Fill Cylinder switch
The DRAIN CYLINDER/FILL CYLINDER switch is used to fill the cylinder with water or
to remove water from the cylinder. When the switch is in the FILL CYLINDER position, the
cylinder will fill with water. The switch must be in the FILL CYLINDER position or the
pump will not operate. In general, anytime the instrument is in use, the switch should be in
the FILL CYLINDER position. At the conclusion of a test, the CYLINDER DRAIN valve
should be opened and the switch moved to the DRAIN CYLINDER position. This will
remove all water from the cylinder. When the unit is not in use, the switch should be in the
OFF position.
Heater switch
The HEATER switch controls all of the power to the heater elements. This switch will
override any control to the heater by the Temperature Controller.
Pressurize Cylinder switch
The PRESSURIZE CYLINDER switch is used to increase the pressure in the cylinder by
turning the hydraulic pump ON.
Cool Cylinder switch
The COOL CYLINDER switch controls the flow of water to the internal cooling coils. This
switch should always be in the OFF position during a test and then switched to the ON
position at the completion of the test to cool the cylinder.
Cylinder Drain valve
The CYLINDER DRAIN valve is used in conjunction with the DRAIN CYLINDER switch
to drain water from the cylinder after completion of a test. The CYLINDER DRAIN valve
should never be opened until all the pressure has been bled from the cylinder and the
temperature is below 200°F/93°C.
High Pressure Limit Regulator
The HIGH PRESSURE LIMIT REGULATOR knob is used to select the upper set point
pressure prior to the beginning of the test. To select the desired pressure upper limit, turn the
HIGH PRESSURE LIMIT REGULATOR knob in (clockwise) as far as it will go. With the
cylinder filled with water and the FILL CYLINDER switch in the ON position, turn the
pump switch to the ON position until the desired pressure set point is reached. The PUMP
PRESSURE ADJUST regulator may need to be adjusted if the pump will not reach the
desired pressure. Slowly turn the HIGH PRESSURE LIMIT REGULATOR knob out
(counterclockwise) until the pressure just begins to drop. The high-pressure limit regulator is
now at the proper set point. The high-pressure limit regulator will only keep the pressure
Summary of Contents for CHANDLER ENGINEERING 7360V
Page 8: ......
Page 14: ......
Page 22: ......
Page 24: ...CHANDLER ENGINEERING...
Page 25: ......