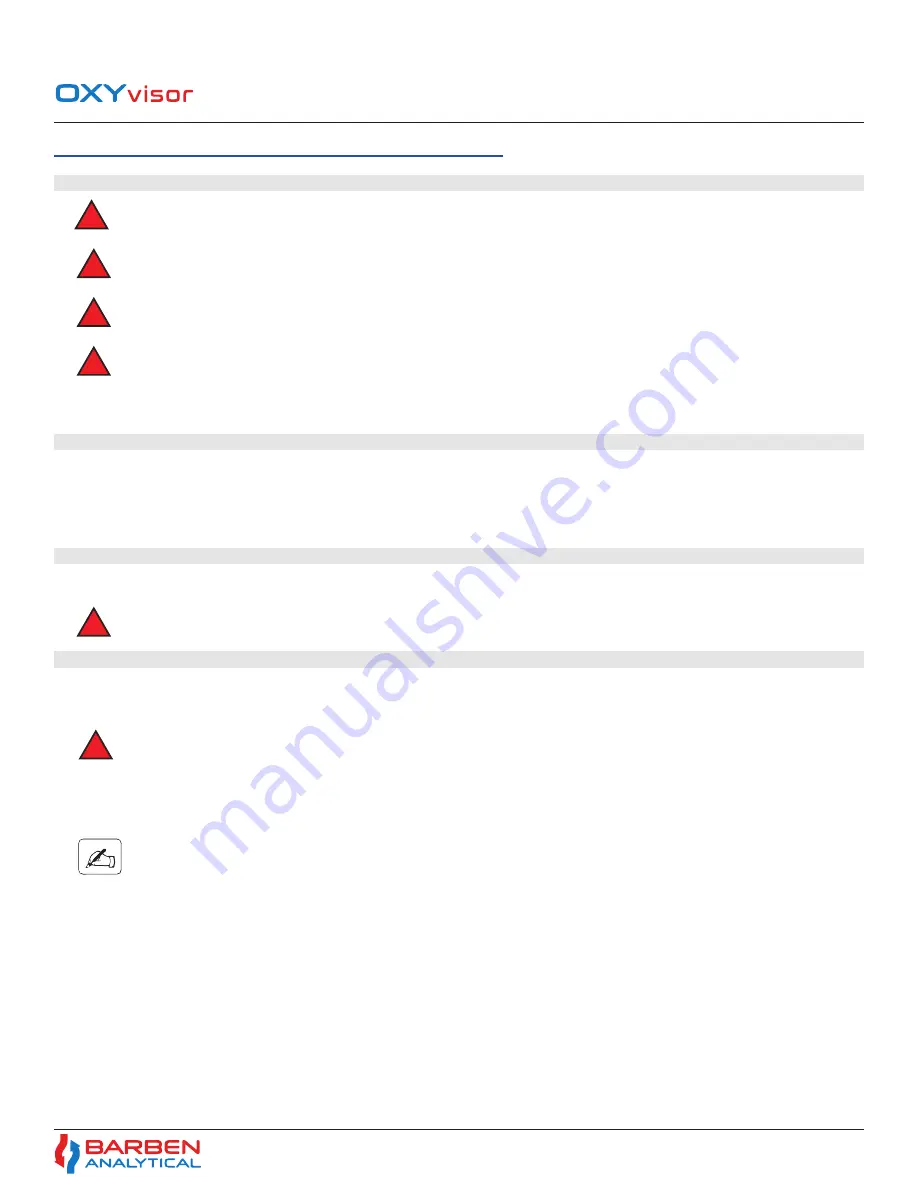
23
IOM (Safety) -
Installation, Operation and Maintenance
Optical Oxygen Analyzer
Section 5- Maintenance / Repair / Service
5.1 Safety Instructions
Only use original accessories or original spare parts as described within this instruction. Observe all relevant installation and safety
instructions described in the instructions for the device or enclosed with the accessory or spare parts.
If an error message exist: (1) Check the gravity of the error, (2) Correct the error, and (3) If the device is faulty take it out of operation.
The
OXYvisor
is not intended for field repair, except a few minor direct part replacements. The only field components allowed for replacement are
the Rear (Wiring) Compartment lid and the Junction Box.
The
OXYvisor
analyzer has minimal maintenance requirements. As good practice, from time-to-time it is recommended to:
•
Visually inspect the analyzer and its components for any damage.
•
Check the Alarm Log for any conditions and take actions if they persist.
•
Wash the analyzer clean with water to remove any buildups of corrosive components.
Maintenance for the BOS oxygen sensors are not covered in this manual. Please consult the BOS maintenance manual.
5.2 Maintenance Overview
5.3 Repairs
There is a danger of explosion when performing repairs and maintenance on the device in a hazardous area. Isolate the device from
power and ensure the atmosphere is explosion-free (hot work permit) before opening the analyzer.
Danger of explosion in areas subject to explosion hazard. Connect the device correctly after maintenance. Close and seal the device
after maintenance work.
Flameproof joints are not intended to be repaired. For repair or replacement of any part, contact Barben Analytical.
Technical Assistance is available directly from, Barben Analytical | AMETEK - 5200 Convair Drive, Carson City NV 89706 | +1.775.883.2500 | Sales.
[email protected]
Section 5
Maintenance / Repair / Service
This section covers removal and installation of field removable or replaceable items.
5.4 Service
The Rear (Wiring) Compartment lid can be removed by:
1.
Using a tool (2 mm Hex), unlock the Rear (Wiring) Compartment 2 mm Hex Lock.
2.
Turn the Rear (Wiring) Compartment lid by rotating counter-clockwise.
There is a danger of explosion when carrying out repairs and maintenance on the device in a hazardous area. Isolate the device from
power and ensure the atmosphere is explosion-free (hot work permit) before opening the analyzer.
5.4.1 - Removing and Replacing Rear (Wiring) Compartment Lid
The Rear (Wiring) Compartment lid can be installed and secured by:
1.
Turn the Rear (Wiring) Compartment lid by rotating clockwise.
2.
Ensure lid threads completely, compresses o-ring and no gap exist between lid and main enclosure.
3.
Secure the lid by tightening the 2 mm Hex Lock with tool.
It is important to be careful when screwing the rear lid cover on or off. Thread surface should be free of any grains, pellets and other
impurity, which cause seizing, and thread could be damaged. Never screw on the cover forcefully!
USEFUL INFORMATION
!
WARNING
!
WARNING
!
WARNING
!
WARNING
!
WARNING
!
WARNING