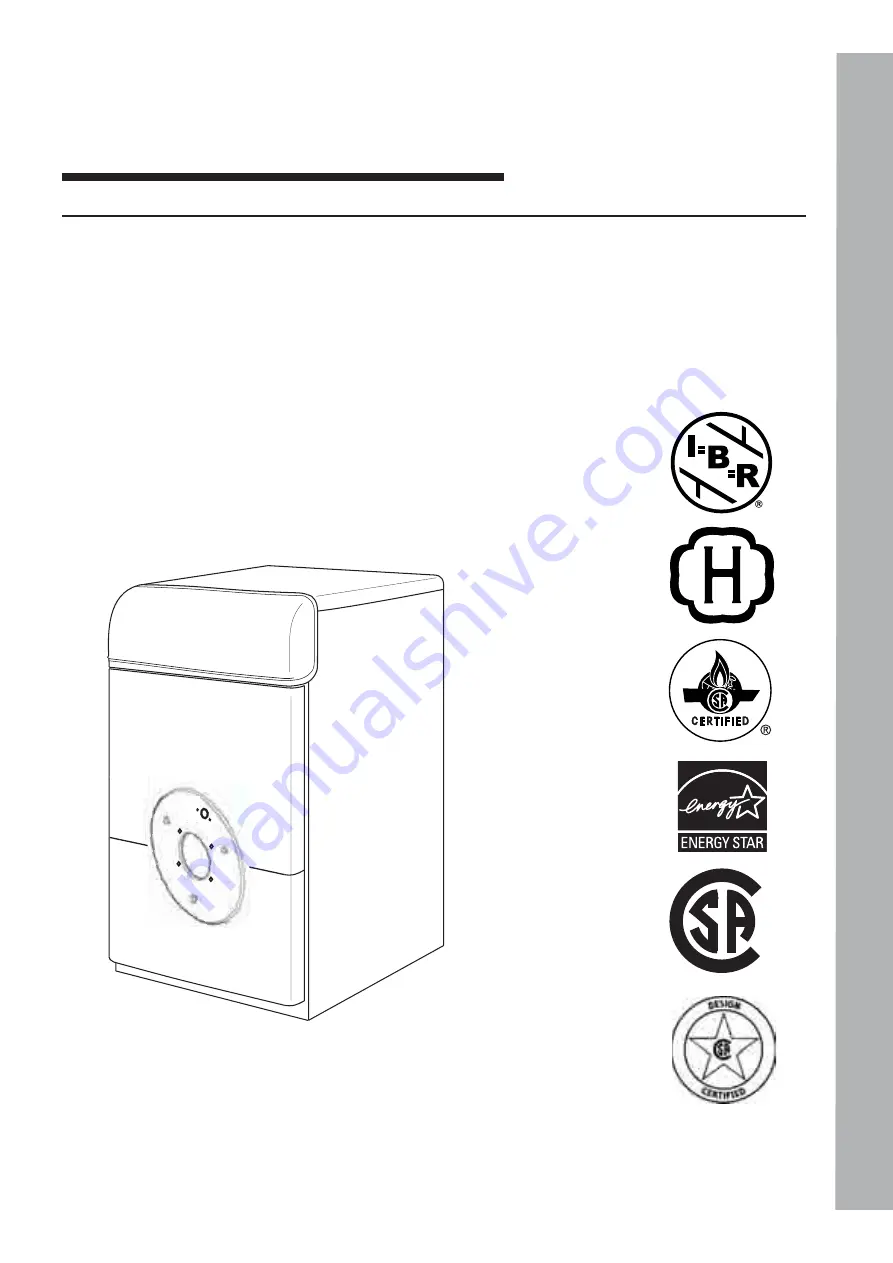
Oil Fired Water Boiler
with Three Pass Cast Iron Heat Exchanger
INSTALLATION GUIDE
*PFWF071A93ABA
*PFWF099A94ABA
*PFWF132A95ABA
*PFWF164A96ABA
* May be “A” or “T”
IMPORTANT —
This Document is
customer property
and is to remain with this unit. Please
return to service information pack upon completion of work.
ALL phases of this installation must comply with NATIONAL, STATE AND LOCAL CODES
18-CG03D1-4
C
US
®
*PFWF201A97ABA
*PFWF242A98ABA
*PFWF286A99ABA