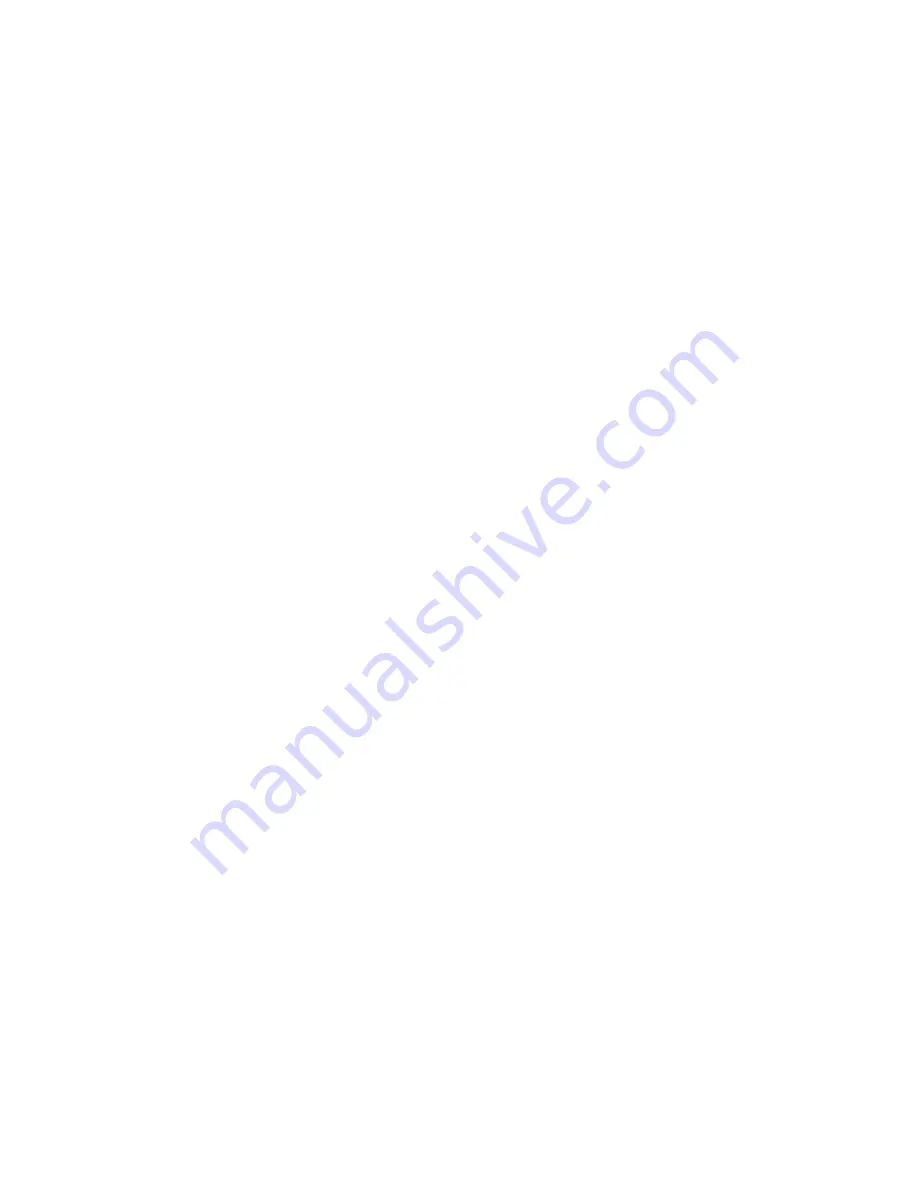
SYSTEM OPERATION
5
This section gives a basic description of heat pump con-
denser unit operation, its various components and their
basic operation. Ensure your system is properly sized for
heat gain and loss according to methods of the Air Condi-
tioning Contractors Association (ACCA) or equivalent.
CONDENSING UNIT
The ambient air is pulled through the heat pump con-
denser coil by a direct drive propeller fan. This air is then
discharged out of the top of the cabinet. These units are
designed for free air discharge, so no additional resistance,
like duct work, shall be attached.
The gas and liquid line connections on present models are
of the sweat type for field piping with refrigerant type cop
-
per. Front seating valves are factory installed to accept the
field run copper. The total refrigerant charge for a normal
installation is factory installed in the heat pump condenser
unit.
AVZC18 models are available in 2 through 5 ton sizes and
use R-410A refrigerant. They are designed for 208/230 volt
single phase applications.
All AVZC18 models use a Daikin rotary compressor specif-
ically designed for R-410A refrigerant. These models are
ComfortNetTM ready.
AVZC18 models use “FVC50K” which is NOT compatible
with mineral oil based lubricants like 3GS. “FVC50K” oil
(required by the manufacturer) must be used if additional oil
is required.
COOLING
The refrigerant used in the system is R-410A. It is a clear,
colorless, non-toxic and non-irritating liquid. R-410A is a
50:50 blend of R-32 and R-125. The boiling point at atmo-
spheric pressure is -62.9°F.
A few of the important principles that make the refrigeration
cycle possible are: heat always flows from a warmer to a
cooler body. Under lower pressure, a refrigerant will absorb
heat and vaporize at a low temperature. The vapors may
be drawn off and condensed at a higher pressure and tem
-
perature to be used again.
The indoor evaporator coil functions to cool and dehumidify
the air conditioned spaces through the evaporative process
taking place within the coil tubes.
NOTE: The pressures and temperatures shown in the
refrigerant cycle illustrations on the following pages are
for demonstration purposes only. Actual temperatures and
pressures are to be obtained from the “Expanded Perfor-
mance Chart”.
Liquid refrigerant at condensing pressure and temperatures
leaves the outdoor condensing coil through the drier and is
metered into the indoor coil through indoor electronic ex-
pansion valve. As the cool, low pressure, saturated refriger-
ant enters the tubes of the indoor coil, a portion of the liquid
immediately vaporizes. It continues to soak up heat and
vaporizes as it proceeds through the coil, cooling the indoor
coil down to about 48°F.
Heat is continually being transferred to the cool fins and
tubes of the indoor evaporator coil by the warm system air.
This warming process causes the refrigerant to boil. The
heat removed from the air is carried off by the vapor.
As the vapor passes through the last tubes of the coil, it
becomes superheated. That is, it absorbs more heat than is
necessary to vaporize it. This is assurance that only dry gas
will reach the compressor. Liquid reaching the compressor
can weaken or break compressor valves.
The compressor increases the pressure of the gas, thus
adding more heat, and discharges hot, high pressure super-
heated gas into the outdoor condenser coil.
In the condenser coil, the hot refrigerant gas, being warmer
than the outdoor air, first loses its superheat by heat trans
-
ferred from the gas through the tubes and fins of the coil.
The refrigerant now becomes saturated, part liquid, part va-
por and then continues to give up heat until it condenses to
a liquid alone. Once the vapor is fully liquefied, it continues
to give up heat which subcools the liquid, and it is ready to
repeat the cycle.
The inverter system can stop the compressor or outdoor
fan to protect the unit. The inverter system can run higher
compressor speed than required from thermostat to recover
compressor oil that flows.
HEATING
The heating portion of the refrigeration cycle is similar to the
cooling cycle. By de-energizing the reversing valve solenoid
coil, the flow of the refrigerant is reversed. The indoor coil
now becomes the heat pump condenser coil, and the out-
door coil becomes the evaporator coil. The check valve at
the outdoor coil will be forced closed by the refrigerant flow,
thereby utilizing the outdoor expansion device. An electron-
ic expansion valve meters the condensed refrigerant to the
outdoor coil.
DEFROST CYCLE
The defrosting of the outdoor coil is controlled by the PCB
and the outdoor coil temperature thermistor and defrost
sensor. The outdoor coil temperature thermistor (Tm) sen-
sor is clamped to a return bend entering the outdoor coil
and the defrost sensor at bottom flowrator leg at outdoor
coil outlet. Defrost timing periods of 30, 60, 90 or 120 min-
utes may be selected via the thermostat setting. PCB will
initiate time defrost at the interval selected from the ther-
mostat. During operation, the microprocessor on the PCB
checks the coil and defrost temperature (Tm and Tb) via
sensors every 5 seconds in heating mode. When the PCB
detects the coil temperature to be high enough (approxi-
mately 54 °F) and defrost sensor more than 43 °F for 30
seconds, the defrost cycle is terminated and the timing pe-
riod is reset. The field service personnel can also advance
a heat pump to the defrost cycle by selecting “force defrost”
option from thermostat.