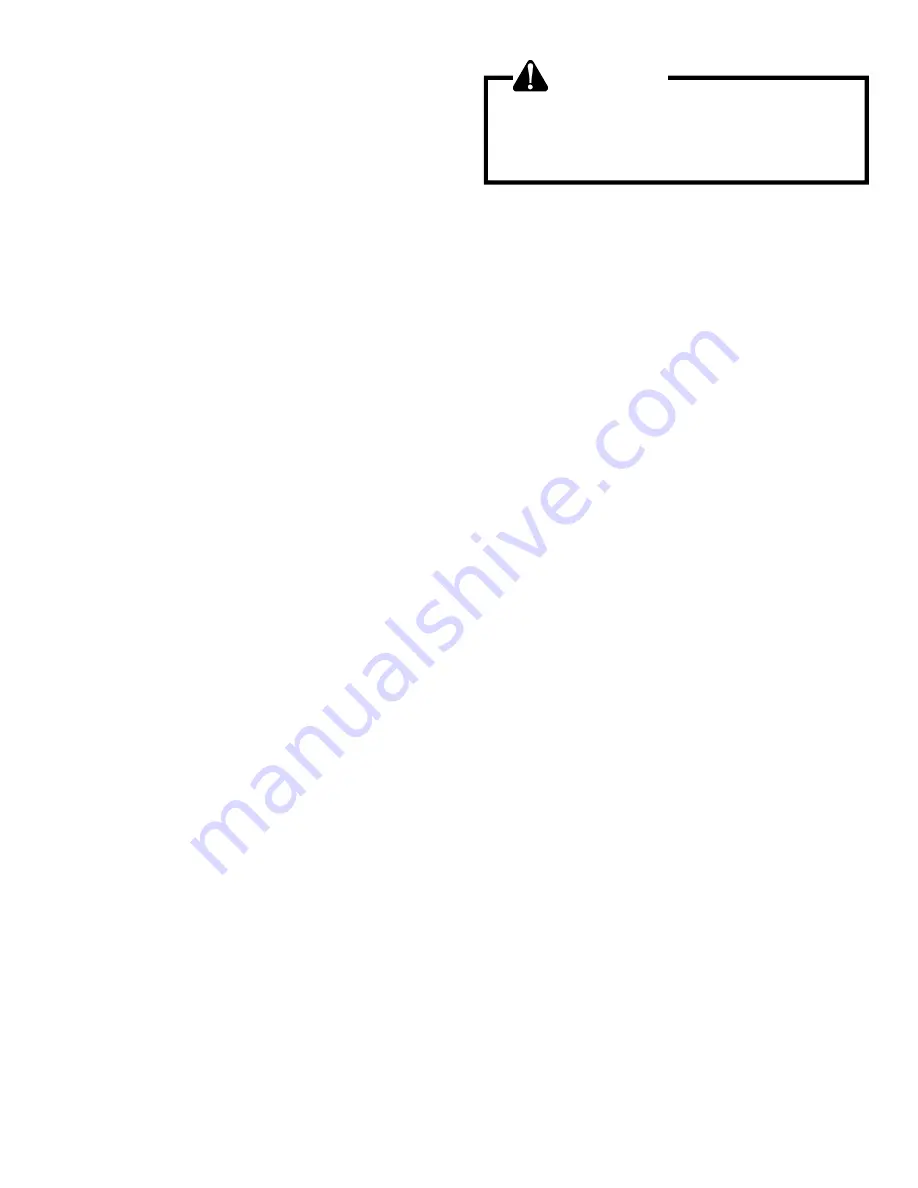
SERVICING
51
0% bleed type expansion valves are used on indoor and outdoor
coils. The 0% bleed valve will not allow the system pressures
(High and Low side) to equalize during the shut down period. The
valve will shut off completely at approximately 100 PSIG.
30% bleed valves used on some other models will continue to
allow some equalization even though the valve has shut-off com-
pletely because of the bleed holes within the valve. This type of
valve should not be used as a replacement for a 0% bleed valve,
due to the resulting drop in performance.
The bulb must be securely fastened with two straps to a clean
straight section of the suction line. Application of the bulb to a
horizontal run of line is preferred. If a vertical installation can-
not be avoided, the bulb must be mounted so that the capillary
tubing comes out at the top.
THE VALVES PROVIDED BY THE MANUFACTURER ARE DESIGNED TO
MEET THE SPECIFICATION REQUIREMENTS FOR OPTIMUM PROD-
UCT OPERATION. DO NOT USE SUBSTITUTES.
S-106
OVERFEEDING
Overfeeding by the thermostatic expansion valve results in high
suction pressure, cold suction line, and possible liquid slugging
of the compressor.
If these symptoms are observed:
1. Check for an overcharged unit by referring to the cooling per-
formance charts in the servicing section.
2. Check the operation of the power element in the valve as ex-
plained in S-110 Checking Thermostatic Expansion Valve
3. Check for restricted or plugged equalizer tube.
S-107
UNDERFEEDING
Underfeeding by the thermostatic expansion valve results in low
system capacity and low suction pressures.
If these symptoms are observed:
1. Check for a restricted liquid line or drier. A restriction will be
indicated by a temperature drop across the drier.
2. Check the operation of the power element of the valve as de-
scribed in S-110 Checking Thermostatic Expansion Valve Op-
eration.
S-108
SUPERHEAT
The thermostatic expansion valve is factory adjusted to maintain
7-9 degrees superheat of the suction gas. Before checking the
superheat or replacing the valve, perform all the procedures out-
lined under Air Flow, Refrigerant Charge, Thermostatic Expansion
Valve - Overfeeding, Underfeeding. These are the most common
causes for evaporator malfunction.
CHECKING SUPERHEAT
Refrigerant gas is considered superheated when its temperature
is higher than the saturation temperature corresponding to its
pressure. The degree of superheat equals the degrees of tempera-
ture increase above the saturation temperature at existing pres-
sure. See Temperature - Pressure Chart on following pages.
CAUTION
To prevent personal injury, carefully connect and
disconnect manifold gauge hoses. Escaping liquid
refrigerant can cause burns. Do not vent refrigerant
to atmosphere. Recover during system repair
or final unit disposal.
1. Run system at least 10 minutes to allow pressure to
stabilize.
2. For best results, temporarily install a thermometer on the
liquid line at the liquid line service valve and 4-6" from the
compressor on the suction line. Ensure the thermometer
makes adequate contact and is insulated for best possible
readings. Use liquid line temperature to determine sub-
cooling and vapor temperature to determine superheat.
NOTE: A
N
OPTIONAL
METHOD
IS
TO
LOCATE
THE
THERMOMETER
AT
THE
SUCTION
LINE
SERVICE
VALVE
. E
NSURE
THE
THERMOMETER
MAKES
ADEQUATE
CONTACT
AND
IS
INSULATED
FOR
BEST
POSSIBLE
READINGS
.
3. Refer to the superheat table provided for proper system
superheat. Add charge to lower superheat or recover charge
to raise superheat.
Superheat Formula = Suct. Line Temp. - Sat. Suct. Temp.
EXAMPLE:
a. Suction Pressure = 143 PSIG
b. Corresponding Temp. = 50°F.
c. Thermometer on Suction Line = 58°F.
To obtain the degrees temperature of superheat, subtract 50.0
from 58.0°F.
The difference is 8° Superheat. The 8° Superheat would fall in the
± range of allowable superheat.
S-109
CHECKING SUBCOOLING
Refrigerant liquid is considered subcooled when its temperature
is lower than the saturation temperature corresponding to its
pressure. The degree of subcooling equals the degrees of tem-
perature decrease below the saturation temperature at the exist-
ing pressure.
1. Attach an accurate thermometer or preferably a thermocouple
type temperature tester to the liquid service valve as it leaves
the condensing unit.
2. Install a high side pressure gauge on the high side (liquid)
service valve at the front of the unit.
3. Record the gauge pressure and the temperature of the line.
4. Review the technical information manual or specification
sheet for the model being serviced to obtain the design
subcooling.