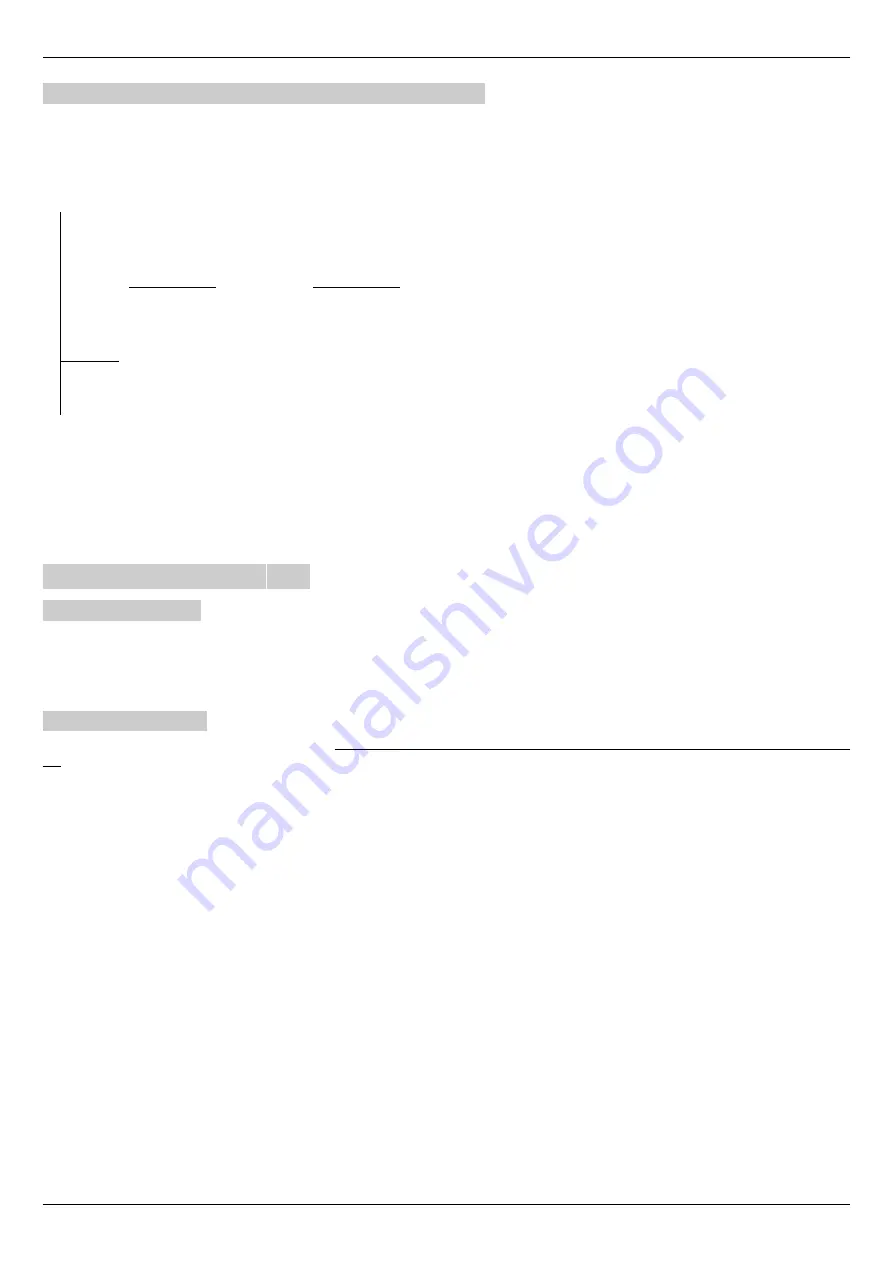
Commissioning
Instruction manual 91/104 V9.2
5.6.8.5 Sequence of commands for gamma change
When you reach the gamma change point, you must execute this sequence of commands to perform the operation correctly:
1. Disable the drive (DEN = OFF).
2. Command the digital input “Stage Bit 0 " in an appropriate way (if there is no turn on the sign, the 0V input means Slow
Range and the 24Vcc input means Fast Range).
3. Change the speed reference (the one entering the AI1 input) to align with the new setting.
NOTE:
If the parameter of “Maximum Speed " is the same in both speed ranges, then there is no need to change the reference
since the signal scale is the same. However, if the above two parameters are different it is necessary that the CNC or the PLC vary
the analog output with this formula:
V
REF1
=
V
REF2
⋅
Max
2
Max
1
or
V
REF2
=
V
REF1
⋅
Max
1
Max
2
with Max
1
and Max
2
are
the values of the parameter “Maximum Speed "
at Gamma 1 and Gamma 2 respectively. From the formule you can calculate the speed references in the various ranges with
respect to each other.
Example: having set the parameter “Maximum Speed " for the Gamma 1 to 2000 RPM and for the Gamma 2 to 7500 RPM, we ad -
mit that we are at a reference of 8V and want to do the gamma change from 1 to 2. What reference will I have to generate from the
CNC to have a linear ramp?
With the 2nd formula substituting VREF
1
= 8V, Max
1
= 2000 RPM, Max
2
= 7500 RPM, I can calculate that V
REF2
= 2,1V.
4. Check with two digital CNC inputs that the contactors are switched correctly.
5. Enable the drive (DEN = ON). The drive may not be enabled immediately due to the residual flow in the motor. In this case a
message appears on the LCD display. As soon as the flow returns to the minimum value, the drive is enabled and powered by
the motor.
6. From now on the drive “Lock" the motor speed and follows the input reference with the selected new speed range.
After selecting the desired range it is possible to stop and restart the motor following the normal procedure indicated in paragraph
"Commands starting sequence“ from page 20.
5.6.9 External torque limit
5.6.9.1 Generality
This function allows you to adjust the motor torque using a selectable analog input, or with a fixed value set on the LCD display. It
should be pointed out that in any case it is essential to have a speed reference connected to the analog input AI1 as in normal mode.
The use of this function can be in several fields: by the use of the asynchronous motor as an axle wrapper of a printing machine, or to
limit the torque in certain machining on a machine tool.
5.6.9.2 Calibration
Before activating this function it is necessary to calibrate the motor as indicated in paragraph "
.
When the motor has been adjusted correctly, you can follow these points to calibrate the function:
•
If an external analogue reference is used to change the torque limit, the shielded cable must be connected to one of the ana -
logue inputs of the drive (see section "Connector X11“ on page 17). The “external torque limit " function shall then be as-
signed to the analog input used; To do this see the paragraph "An.Inp. X dest“ on page 41.
•
The torque limit can be adjusted with the analog input configured just above, or by changing the parameter “Advanced Setup
→ Aux Functions → Ext Torque Limit → Limit Setpoint" with the keypad. In any case, this parameter indicates the external
limit set to it: if it varies by itself, it means that an analog input is connected.
•
Use the “Advanced Setup → Aux Functions → Ext Torque Limit → Torque Limit" menu enable the function by changing
the parameter to ENABLED.
•
In the menu “Advanced Setup → Aux Functions → Ext Torque Limit → Limit Output" if the function is active, you can see
the current value of the torque limit. If the function is not active, this parameter will always be 99.99 % and will not change
even by changing the associated analog input.
The scale of this torque limit is as a percentage of the maximum torque of the motor. If the analog input has the standard gain values
(Gain) the value of 10Vcc on the terminals corresponds to the maximum torque of 100 %; in proportion, a voltage of 5Vcc on the ter-
minals corresponds to 50 % of the maximum torque. As always, you can change the scale of the analog input to adapt it to the signal
(see section Analog input X from page 41).
70
Alter Elettronica s.r.l.