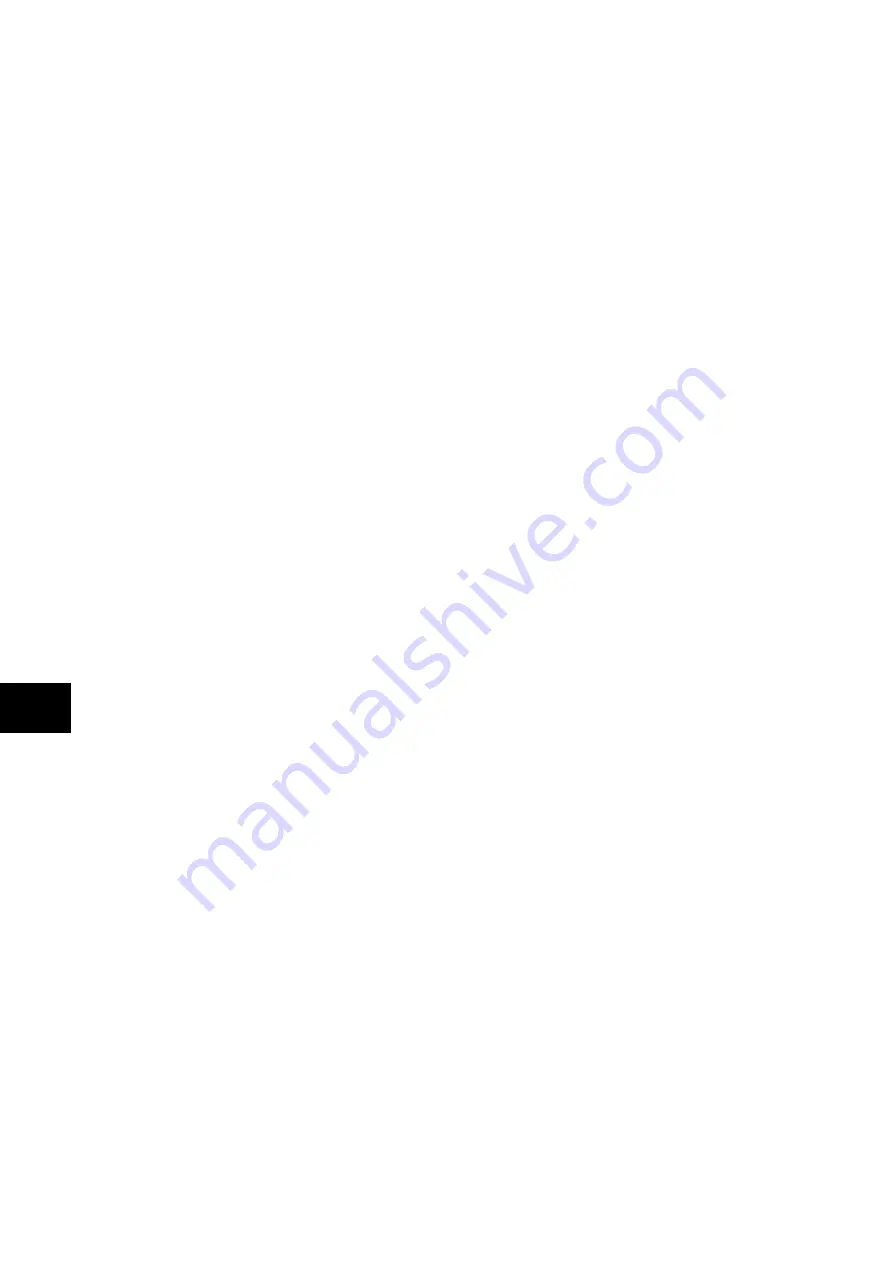
P846/EN FD/D
Firmware Design
(FD) 9-6
MiCOM P846
FD
1.3.2
Co-processor board
The processor used on the second board is the same as that used on the main processor
board. The second processor board has provision for fast access (zero wait state) SRAM for
use with both program and data memory storage. This memory can be accessed by the
main processor board via the parallel bus, and this route is used at power-on to download
the software for the second processor from the flash memory on the main processor board.
Further communication between the two processor boards is achieved via interrupts and the
shared SRAM. The serial bus carrying the sample data is also connected to the co-
processor board, using the processor’s built-in serial port, as on the main processor board.
The co-processor board also handles all communication with the remote differential relay(s).
This is achieved via optical fibre communications and hence the co-processor board holds
the optical modules to transmit and receive data over the fibre links.
1.3.3
Internal communication buses
The relay has two internal buses for the communication of data between different modules.
The main bus is a parallel link that is part of a 64-way ribbon cable. The ribbon cable carries
the data and address bus signals in addition to control signals and all power supply lines.
Operation of the bus is driven by the main processor board that operates as a master while
all other modules within the relay are slaves.
The second bus is a serial link that is used exclusively for communicating the digital sample
values from the input module to the main processor board. The DSP processor has a built-in
serial port that is used to read the sample data from the serial bus. The serial bus is also
carried on the 64-way ribbon cable.
1.3.4
Input module
The input module provides the interface between the relay processor board and the analog
and digital signals coming into the relay. The input module consists of two PCBs; the main
input board and a transformer board.
1.3.4.1 Transformer board
The transformer board holds up to four voltage transformers (VTs) and up to five current
transformers (CTs). The current inputs will accept either 1A or 5A nominal current (menu
and wiring options) and the voltage inputs can be specified for either 110V or 440V nominal
voltage (order option). The transformers are used both to step-down the currents and
voltages to levels appropriate to the relay’s electronic circuitry and to provide effective
isolation between the relay and the power system. The connection arrangements of both the
current and voltage transformer secondary’s provide differential input signals to the main
input board to reduce noise.
1.3.4.2 Input board
The main input board is shown as a block diagram in Figure 2. It provides the circuitry for
the digital input signals and the analog-to-digital conversion for the analog signals. Hence it
takes the differential analog signals from the CTs and VTs on the transformer board(s),
converts these to digital samples and transmits the samples to the processor board via the
serial data bus. On the input board the analog signals are passed through an anti-alias filter
before being multiplexed into a single analog to digital converter chip. The A - D converter
provides 16-bit resolution and a serial data stream output. The digital input signals are opto
isolated on this board to prevent excessive voltages on these inputs causing damage to the
relay's internal circuitry.
Summary of Contents for MiCOM P846
Page 2: ......
Page 4: ......
Page 5: ...Safety Section P846 EN SS H11 SS SAFETY SECTION...
Page 6: ...P846 EN SS H11 Safety Section SS...
Page 8: ...P846 EN SS H11 Safety Section SS 2 SS...
Page 16: ...P846 EN IT D Introduction MiCOM P846 IT...
Page 18: ...P846 EN IT D Introduction IT 1 2 MiCOM P846 IT...
Page 26: ...P846 EN TD D Technical Data MiCOM P846 TD...
Page 38: ...P846 EN GS D Getting Started MiCOM P846 GS...
Page 58: ...P846 EN ST D Getting Started MiCOM P846 ST...
Page 60: ...P846 EN ST D Settings ST 4 2 MiCOM P846 ST...
Page 78: ...P846 EN OP D Operation MiCOM P846 OP...
Page 104: ...P846 EN OP D Operation OP 5 26 MiCOM P846 OP...
Page 106: ...P846 EN AP D Application Notes MiCOM P846 AP...
Page 108: ...P846 EN AP D Application Notes AP 6 2 MiCOM P846 AP...
Page 122: ...P846 EN AP D Application Notes AP 6 16 MiCOM P846 AP...
Page 124: ...P846 EN PL D Programmable Logic MiCOM P846 PL...
Page 126: ...P846 EN PL D Programmable Logic PL 7 2 MiCOM P846 PL...
Page 144: ...P846 EN MR D Measurements and Recording MiCOM P846 MR...
Page 146: ...P846 EN MR D Measurements and Recording MR 8 2 MiCOM P846 MR...
Page 160: ...P846 EN FD D Firmware Design MiCOM P846 FD...
Page 182: ...P846 EN CM D Commissioning MiCOM P846 CM...
Page 228: ...P846 EN CM D Commissioning CM 10 46 MiCOM P846 CM...
Page 230: ...P846 EN MT D Maintenance MiCOM P846 MT...
Page 232: ...P846 EN MT D Maintenance MT 11 2 MiCOM P846 MT...
Page 238: ...P846 EN TS D Troubleshooting MiCOM P846 TS...
Page 240: ...P846 EN TS D Troubleshooting TS 12 2 MiCOM P846 TS...
Page 252: ...P846 EN SC D SCADA Communications MiCOM P846 SC...
Page 272: ...P846 EN SG D Symbols and Glossary MiCOM P846 SG...
Page 280: ...P846 EN SG D Symbols and Glossary SG 14 8 MiCOM P846 SG...
Page 282: ...P846 EN IN D Installation MiCOM P846 IN...
Page 284: ...P846 EN IN D Installation IN 15 2 MiCOM P846 IN...
Page 296: ...P846 EN IN D Installation IN 15 14 MiCOM P846 IN...
Page 297: ......