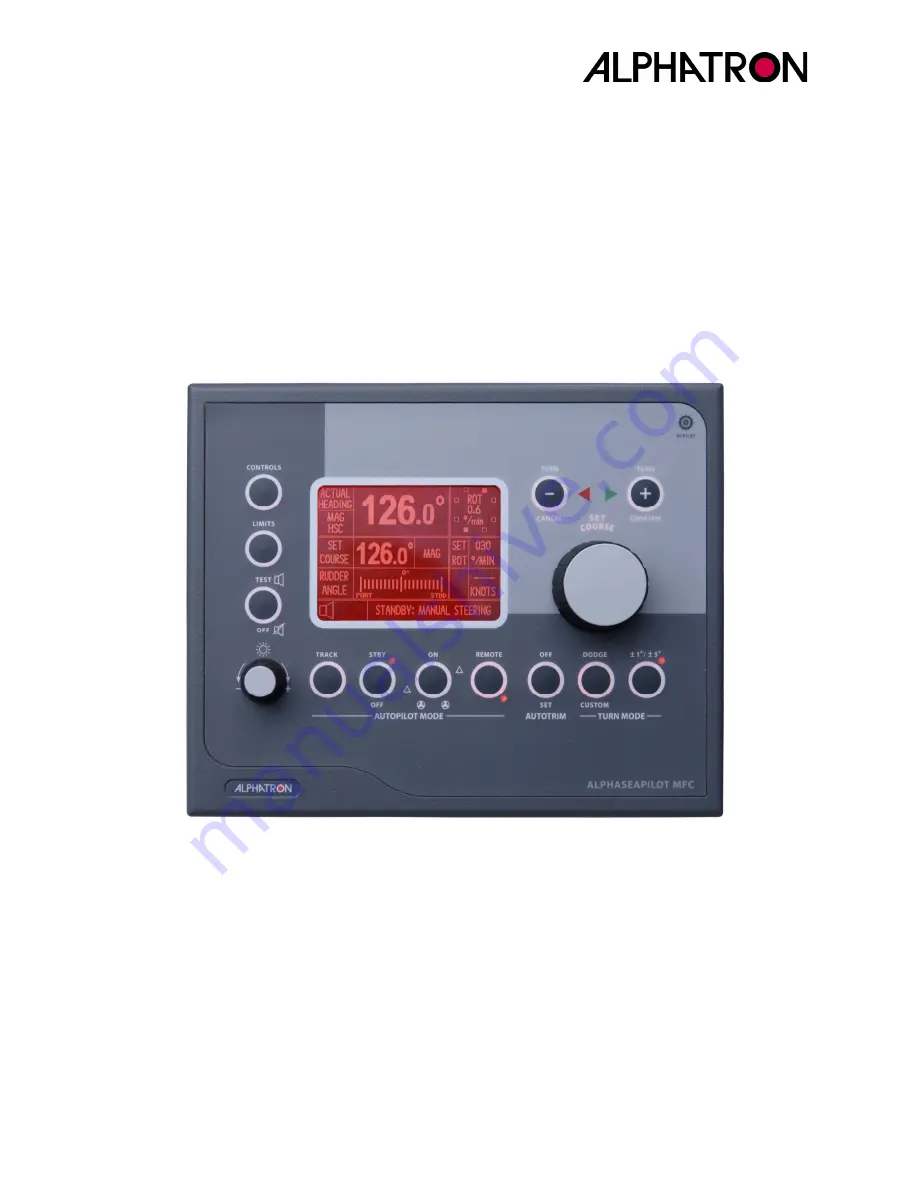
ALPHASEAPILOT MFC
Autopilot
Operating manual
ALPHATRON MARINE B.V.
Schaardijk 23
3063 NH ROTTERDAM
The Netherlands
Tel: +31 (0)10 – 453 4000
Fax: +31 (0)10 – 452 9214
P.O. Box 210003
3001 AA ROTTERDAM
Web: www.alphatronmarine.com
Mail: [email protected]
The information in this Manual is subject to change without notice and
does not represent a commitment on the part of ALPHATRON MARINE
B.V.
Document
:
Manual ALPHASEAPILOT MFC
Issue
:
1.1
ALPHATRON MARINE B.V.
Manufactured for Alphatron by Navitron Systems Ltd., Havant Hants UK