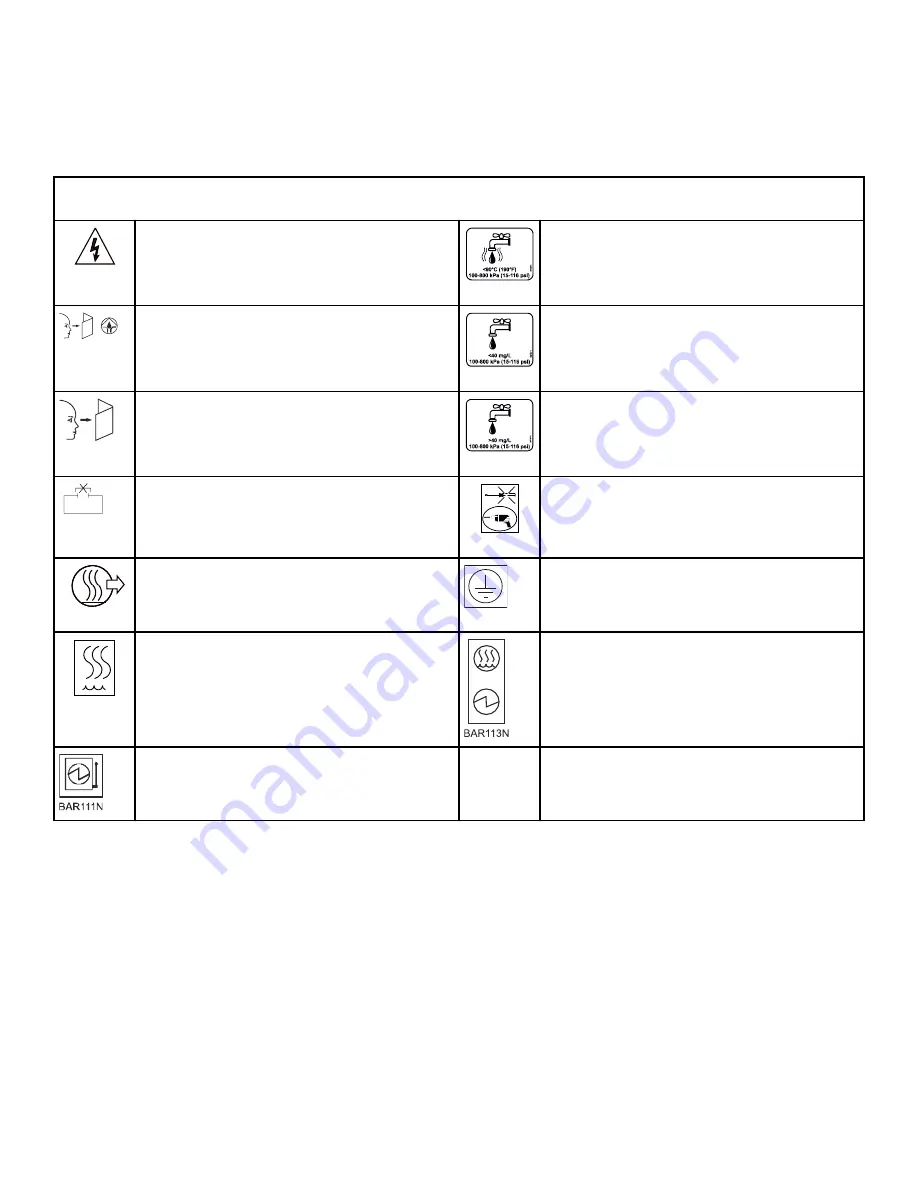
Operation
Symbols on the Machine
Symbols Used
CHM2439N_SVG
Caution, dangerous electrical tension, electrical de-
vices
CHM2446N_SVG
Warm water inlet (red color of the label)
i
530755
CZB93N
Label Lubrication
CHM2447N_SVG
Soft cold water inlet (light blue color of the label)
i
5 0
7 313
CZB94N
Label - read before use
CHM2448N_SVG
Hard cold water inlet (dark blue of the label)
CZW105N
Do not close or cover
CHM2490N_SVG
The holes to be drilled not punched
CHM2443N_SVG
The machine hot air outlet
CZB95N
Earthing Index Plate
CHM2445N_SVG
Steam
Steam heating, Electrical heating
Main switch
Table 27
Operation
©
Copyright, Alliance Laundry Systems LLC -
DO NOT COPY or TRANSMIT
50
Part No. D2601EN
Summary of Contents for UY350 PROFORM TOUCH
Page 2: ......