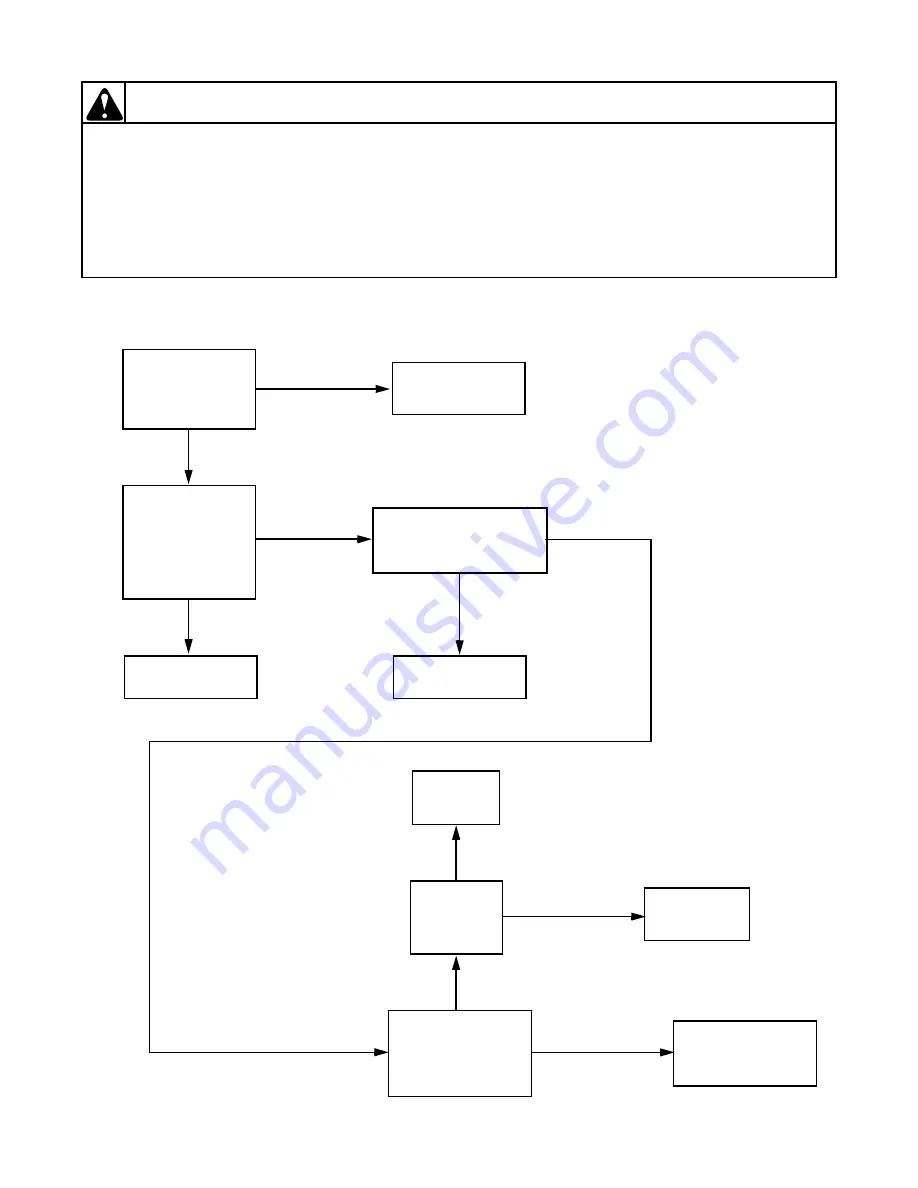
26
M411429
Section 3 Troubleshooting
To reduce the risk of electric shock, fire, explosion, serious injury or death:
• Disconnect electric power to the tumbler before servicing.
• Close gas shut-off valve to gas tumbler before servicing.
• Close steam valve to steam tumbler before servicing.
• Never start the tumbler with any guards/panels removed.
• Whenever ground wires are removed during servicing, these ground wires must be
reconnected to ensure that the tumbler is properly grounded.
W002
WARNING
© Copyright, Alliance Laundry Systems LLC – DO NOT COPY or TRANSMIT
26. SPARK TO PILOT BURNER — PILOT LIGHTS — NO MAIN BURNER
(Electronic Pilot Ignition Models Only)
24 VOLTS BETWEEN
TERMINAL 3 AND
GROUND ON
ELECTRONIC
PACKAGE
YES
NO
REPLACE LEFT COIL
(Main Operator)
WIRE BETWEEN
SENSOR AND
TERMINAL 4 OF
ELECTRONIC
PACKAGE
CONNECTED
SECURELY
SENSOR SECURELY
SEATED IN
PILOT BURNER
REPLACE
SENSOR
CLEAR PILOT ORIFICE
OR USE LARGER
PILOT ORIFICE
PILOT FILTER,
TUBE OR
ORIFICE
OBSTRUCTED
YES
NO
NO
YES
YES
YES
CORRECT
NO
CORRECT
YES
CRACK IN
SENSOR
CERAMIC
INSULATOR
YES
CHECK GAS
PRESSURE
NO