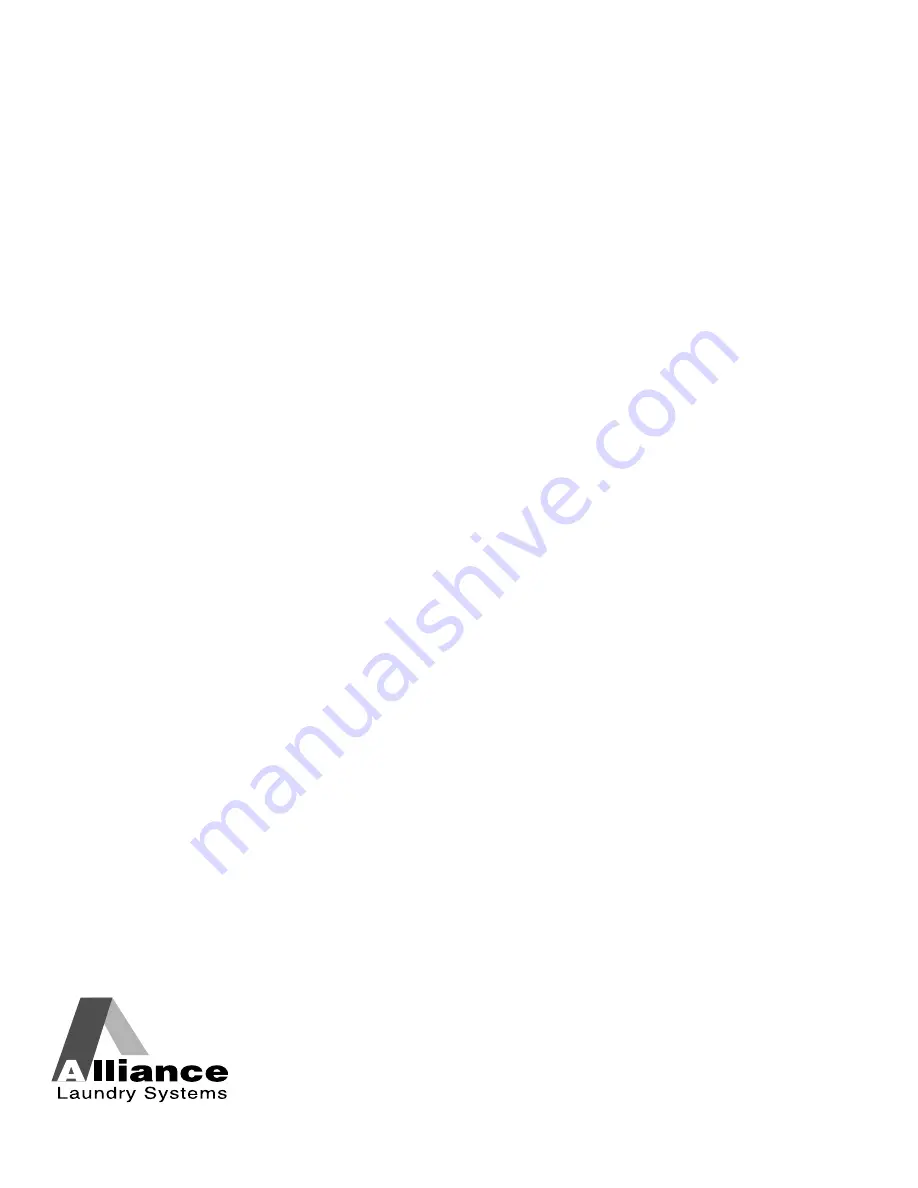
Installation/Operation/Maintenance
Washer-Extractors
Cabinet Freestanding
Refer to Page 9 for Model Identification
Original Instructions
Keep These Instructions for Future Reference.
(If this machine changes ownership, this manual must accompany machine.)
www.alliancelaundry.com
Part No. D1627ENR5
March 2016
Summary of Contents for D1627ENR5
Page 2: ......