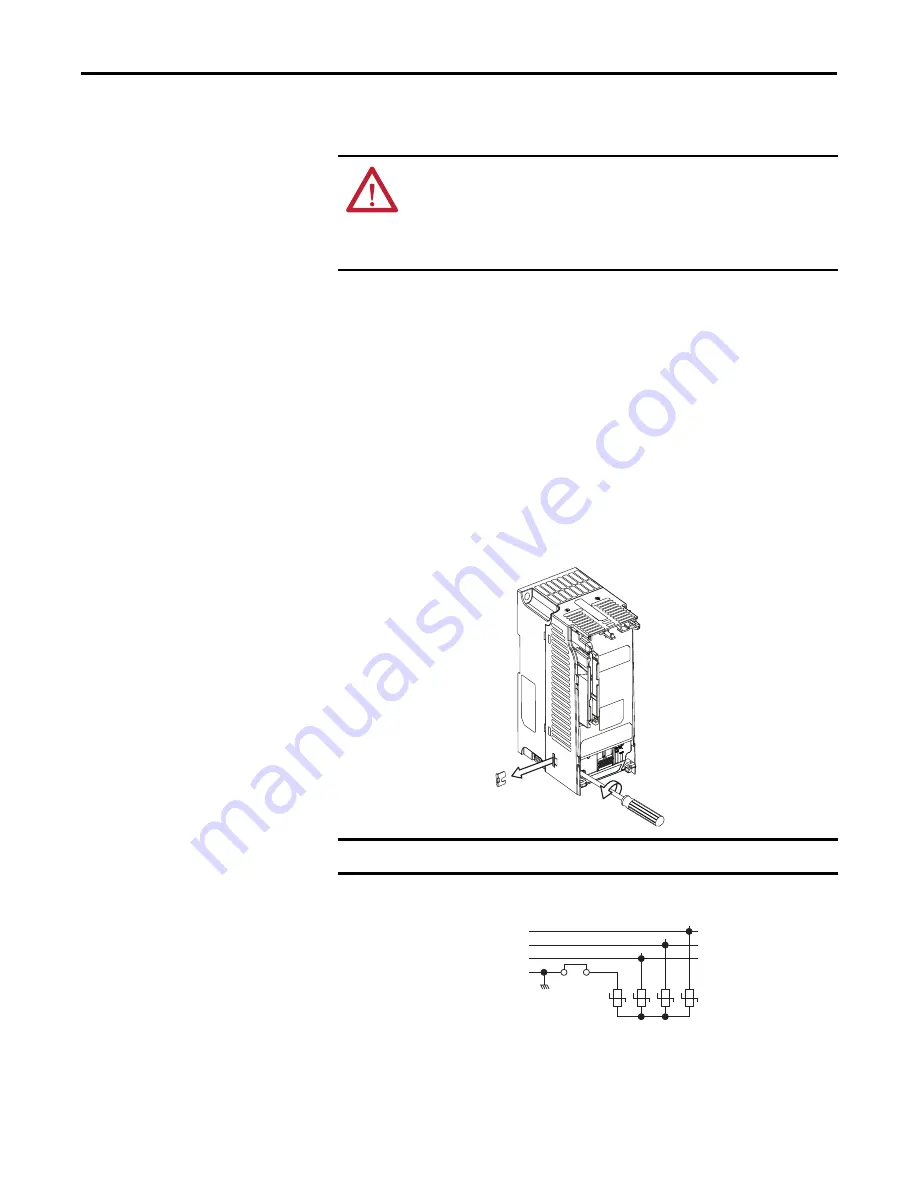
Rockwell Automation Publication 520-UM002B-EN-E - December 2017
17
Installation/Wiring
Chapter 1
AC Supply Source
Considerations
Ungrounded Distribution Systems
Disconnecting MOVs
To prevent drive damage, the MOVs connected to ground shall be disconnected
if the drive is installed on an ungrounded distribution system (IT mains) where
the line-to-ground voltages on any phase could exceed 125% of the nominal line-
to-line voltage. To disconnect these devices, remove the jumper shown in the
diagrams below.
1.
Turn the screw counterclockwise to loosen.
2.
Pull the jumper completely out of the drive chassis.
3.
Tighten the screw to keep it in place.
Jumper Location (Typical)
Phase to Ground MOV Removal
ATTENTION:
PowerFlex 527 drives contain protective MOVs that are referenced
to ground. These devices must be disconnected if the drive is installed on an
ungrounded or resistive grounded distribution system.
ATTENTION:
Removing MOVs in drives with an embedded filter will also
disconnect the filter capacitor from earth ground.
IMPORTANT
Tighten screw after jumper removal.
Power module
R/L1
S/L2
T/L3
1
2
3
4
Three-Phase
AC Input
Jumper
Summary of Contents for PowerFlex 527
Page 4: ...4 Rockwell Automation Publication520 UM002B EN E December 2017 Summary of Changes Notes...
Page 8: ...8 Rockwell Automation Publication 520 UM002B EN E December 2017 Table of Contents Notes...
Page 173: ...Rockwell Automation Publication520 UM002B EN E December 2017 173 Notes...
Page 174: ...174 Rockwell Automation Publication 520 UM002B EN E December 2017 Notes...
Page 175: ......