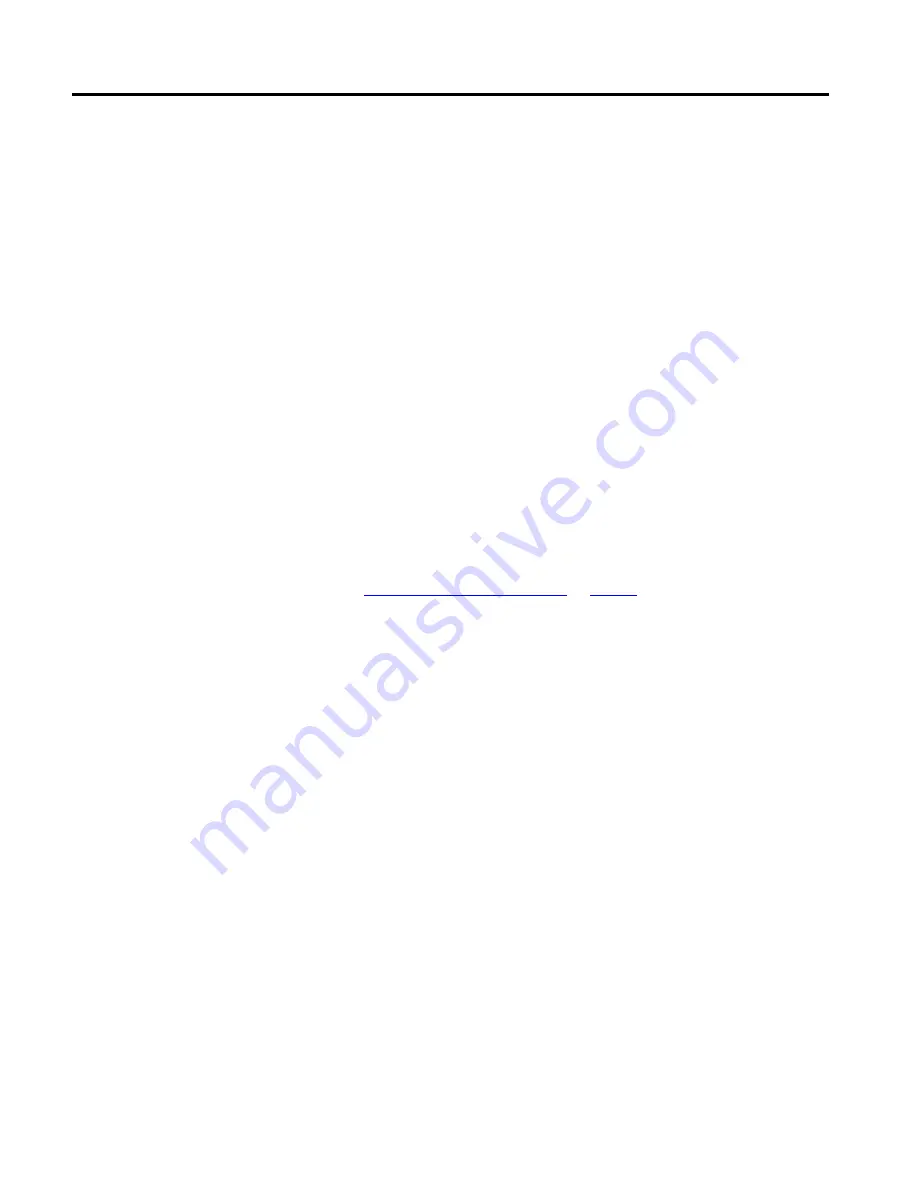
Chapter 2
Behavior models used in CIP Motion
30
Rockwell Automation Publication MOTION-RM003I-EN-P - February 2018
command reference signals to the device's control structure at the device's update
rate.
Another source of command data is a local Motion Planner resident within the
device. The Motion Device Axis Object defines a rich set of features associated
with a device based Motion Planner. These features include support for electronic
gearing, camming, moves, and jogs. Through use of the CIP Motion peer-to-peer
connection, the gearing and camming functions can be directly linked to a master
axis command reference from a producing peer device for high performance
line-shafting applications. Alternatively, the master axis command reference can be
derived from a local motion axis instance. To facilitate these features, the Motion
Planner also supports the ability to establish an absolute position reference to the
machine through homing and redefine position operations as well as perform
rotary unwind functionality. The device's Motion Planner is controlled by CIP
service requests.
Command Data, such as the Controller Velocity Command, can be set directly by
the user. In this context, the device must apply its own Ramp Generator function
to smoothly accelerate or decelerate the motor to the commanded velocity.
See also
For synchronized, high-performance applications using CIP Motion, command
data is received from the CIP Motion C-to-D Connection or the device's local
Motion Planner, and based on the connection's Command Target Update
element being set to 'Interpolate', processed by the Fine Interpolator functionality
of the Command Generator.
The job of the Fine Interpolator is to compute coefficients to a trajectory
polynomial that is designed to reach the command data at its associated
Command Target Time. Depending on the specific command data element, the
trajectory can follow a 1
st
, 2
nd,
or 3
rd
order polynomial trajectory with initial
conditions based on current axis dynamics.
Because the polynomial is a function of time, a new fine command value can be
calculated any time the CIP Motion device needs to perform a control calculation.
As a result, it is not necessary that the device's control calculation period be
integrally divisible into the Controller Update Period.
To improve device interchangeability, a minimum order for the fine interpolators
is recommended. Because contemporary Motion Planners typically generate their
trajectories based on 3
rd
order polynomials in position, it is important that the fine
interpolators reproduce these trajectories with high fidelity. Therefore, the
position fine interpolator is defined as 3
rd
order, the velocity interpolator is 2
nd
order, and the acceleration and torque interpolators are both 1
st
order. Higher
order fine interpolators are possible and are left to the device vendor's discretion.
Command Fine Interpolation