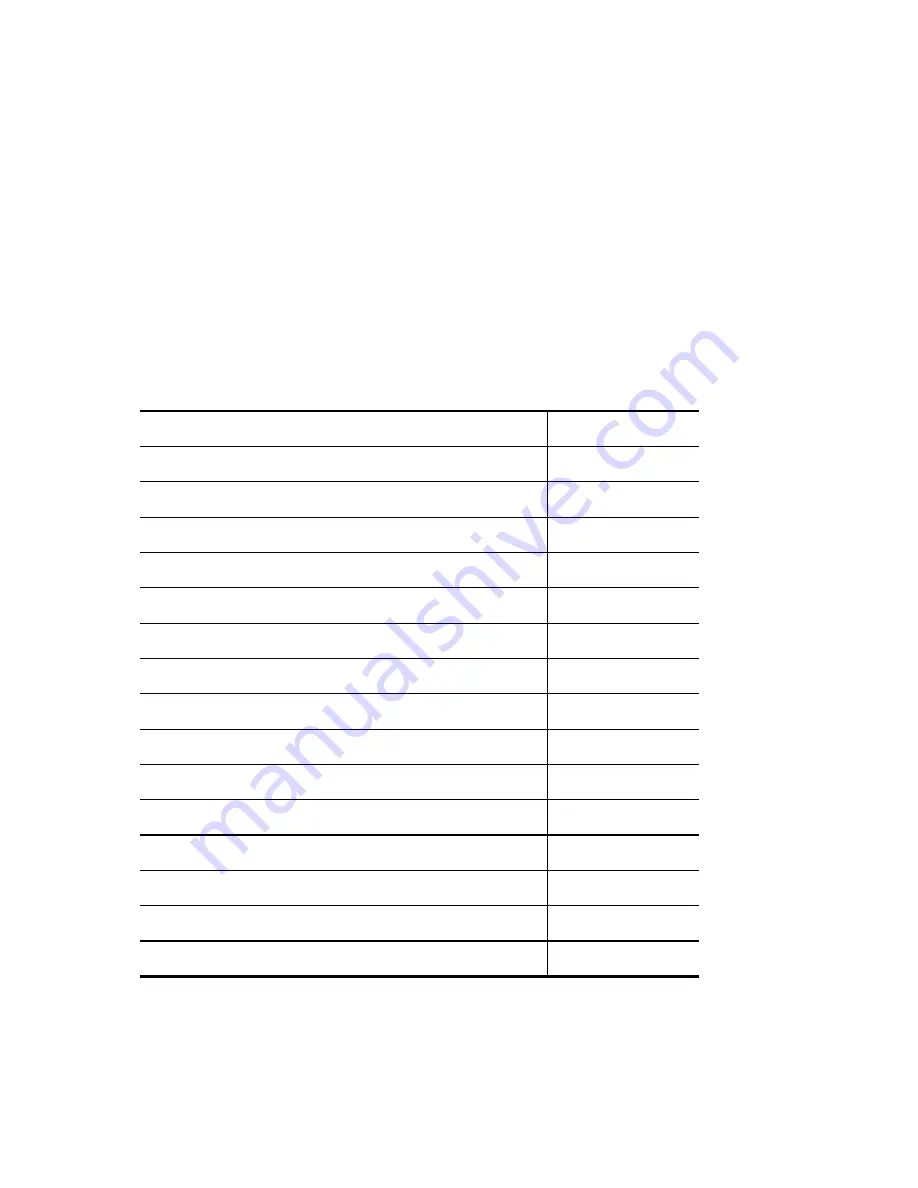
Publication
1797-IN004G-EN-P - August 2017
Installation Instructions
FLEX Ex Thermocouple/RTD Input Module
Catalog Number 1797-IRT8
Contents
For Information About
See Page
Important User Information
2
Module Installation
3
Installation in Zone 1
5
Installation in Zone 22
5
European Communities (EC) Directive Compliance
6
Inputs
8
Indicators
14
Output Map
15
Fault Mode - Write Word 0
16
Add-on Filter Selections - Write Word 0
16
Reference Junction Selection - Write Word 0
16
RTD Offset Select - Write Word 2
17
Sensor Type Select - Write Word 1
18
Specifications
19
Entity Parameters
23
Summary of Contents for FLEX Ex 1797-IRT8
Page 33: ...FLEX Ex Thermocouple RTD Input Module 33 Publication 1797 IN004G EN P August 2017 Notes ...
Page 34: ...34 FLEX Ex Thermocouple RTD Input Module Publication 1797 IN004G EN P August 2017 Notes ...
Page 35: ...FLEX Ex Thermocouple RTD Input Module 35 Publication 1797 IN004G EN P August 2017 Notes ...