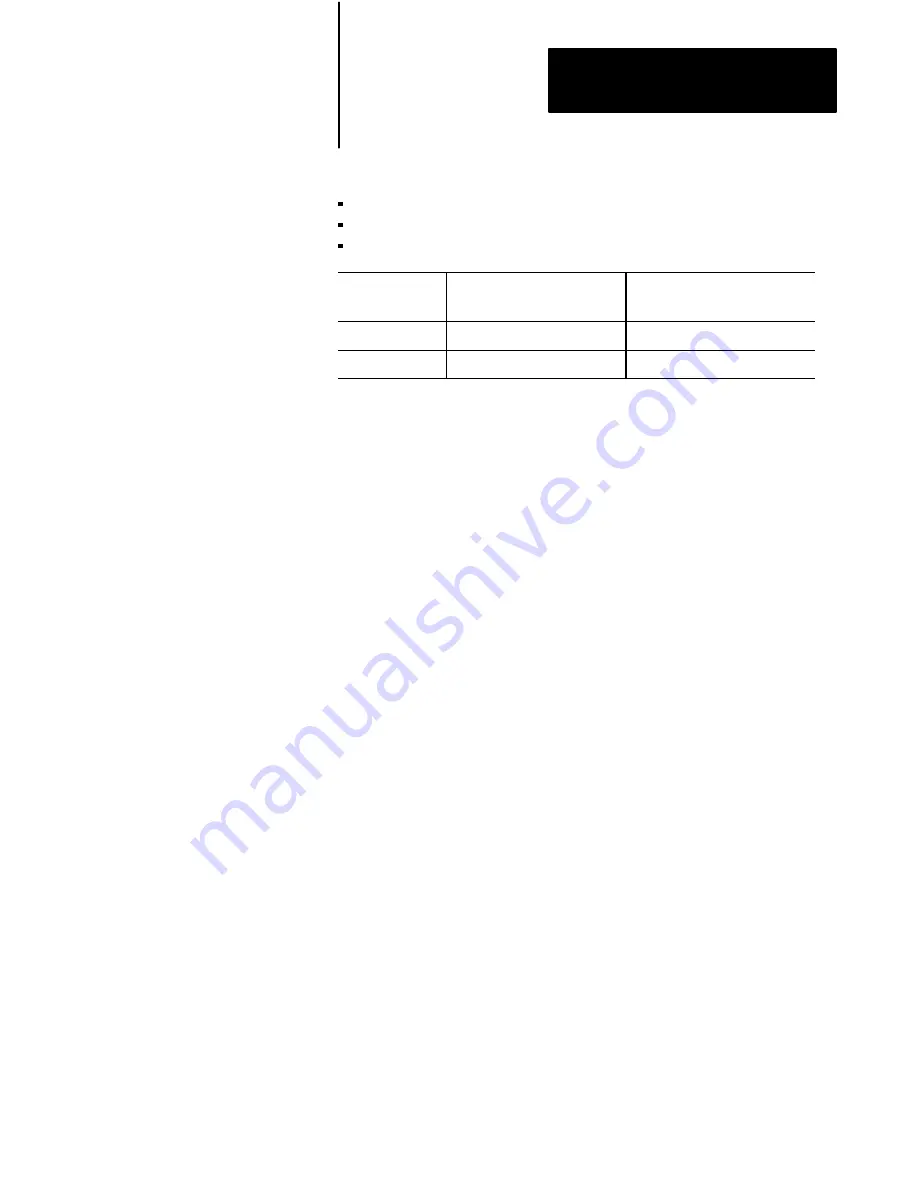
Load Initial Configuration Values
Chapter 7
7-25
Determine Output for Maximum values as follows:
9999 (100%) for uni-directional direct acting valves
0 (0%) or 9999 (100%) for bi-directional valves depending on direction
0 (0%) for uni-directional reverse acting valves
If your selected
pressure valve is:
Then the value in word 48
should be:
And during the profile, the QDC
module does NOT drive the valve
with a % output:
Direct Acting
greater than the value in word 47 greater than the value in word 48
Reverse Acting
less than the value in word 47
less than the value in word 48
Record your initial Output for Maximum value on Worksheet 7-D.
Profile Tuning Constants
(INC4953, PKC4954, HDC4954, and PLC4954)
The QDC module’s PID and velocity feedforward(VelFF) algorithms are
different from classic PID and VelFF algorithms. QDC module algorithms
are sensitive to changes in load (not changes in setpoint) because the QDC
module must respond to a system that is undergoing constant load changes
when hydraulic fluid is introduced into or relieved from the hydraulic
circuit. The algorithm gain constants are typically lower than those used to
control a process that reacts to setpoints changes.
We entered all profile tuning constants on corresponding worksheets.
Profile Pressure Alarm Setpoints
(INC5758, PKC5758, HDC5758, and PLC57)
The QDC module compares the ram (screw) or cavity pressure against
these entries when executing the appropriate profile. The QDC module sets
a corresponding alarm bit any time ram (screw) or cavity pressure equals
or exceeds these entries during the respective profile. A zero entry inhibits
each respective alarm.
We recorded zero for each alarm setpoint on corresponding worksheets.
Set Profile Tuning
Constants, PressureAlarm
Setpoints, and Watchdog
Timer Preset