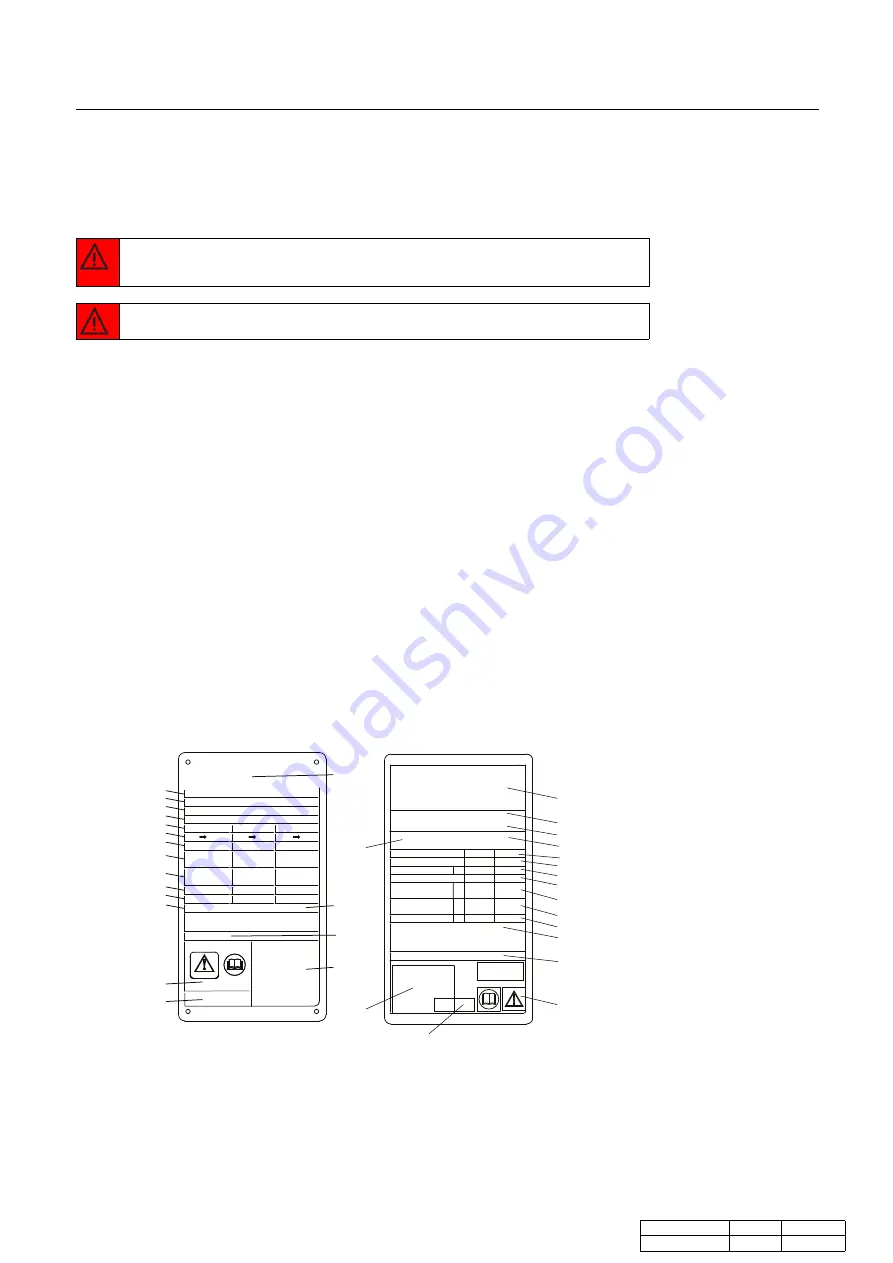
Description
Name plate
The type of unit, manufacturing number and manufacturing year can be found on the name
plate. Pressure vessel details in accordance with the applicable pressure vessel code are also
given. The name plate is fixed to the frame plate, most commonly, or the pressure plate. The
name plate can be a steel plate or a sticker label.
Warning!
The design pressures and temperatures for each unit are marked on the name plate.
These must not be exceeded.
Caution!
Avoid aggressive chemicals for cleaning the heat exchanger when a sticker label is used.
The design pressure (11) and the design temperature (10), as given on the name plate, are the
values against which the heat exchanger is approved according to the pressure vessel code in
question. The design temperature (10) may exceed the maximum operating temperature (8) for
which the gaskets have been selected for. If the operating temperatures as specified on the
PHE drawing are to be changed the supplier should be consulted.
1. Space for logotype
2. Open space
3. Website for service
4. Drawing of possible locations of connections/Location of 3A tag for 3A units
5. Space for mark of approval
6. Warning, read manual
7. Date of pressure test
8. Maximum operating temperature
9. Manufacturer test pressure (PT)
10. Allowable temperatures Min/Max (TS)
11. Allowable pressures Min/Max (PS)
12. Decisive volume or volume for each fluid (V)
13. Locations of the connections for each fluid
14. Decisive fluid group
15. Year of manufacture
16. Serial number
17. Type
18. Manufacturer’s name
1
2
3
4
18
17
16
15
14
13
12
11
10
9
8
7
6
5
1
18
15
13
14
12
8
11
10
9
6
5
4
17
7
3
TS
V
INLET → OUTLET
VOLUME
MIN./MAX.
ALLOWABLE PRESS.
→
→
STATISTICAL BASIS.
MANUFACTURER
FOR SERVICE:
PRESSURE TESTING PERFORMED ON
PRESSURE TESTED
MAX. OP. TEMP.
FLUID GROUP
YEAR OF MANUFACTURING:
MANUFACTURER:
ALLOWABLE TEMP.
MIN./MAX.
TYPE:
SERIAL NUMBER:
PT
PS
Service
Year
Manufacturer
Fluid group
Inlet Outlet
Allowable press.
Allowable temp.
Volume V
Manufacturer
Serial No.
Type
Max. op. temp.
Test pressure date
WARNING
Min./Max. PS
Min./Max. TS
PT
16
Figure 1. Example of CE metallic name plate to the left and CE sticker label name plate to
the right
Document ID
Language
Edition
8
Instruction Manual - Plate Heat Exchangers
3490017599
EN
2016-06
Summary of Contents for FrontLine WideGap 100
Page 2: ......