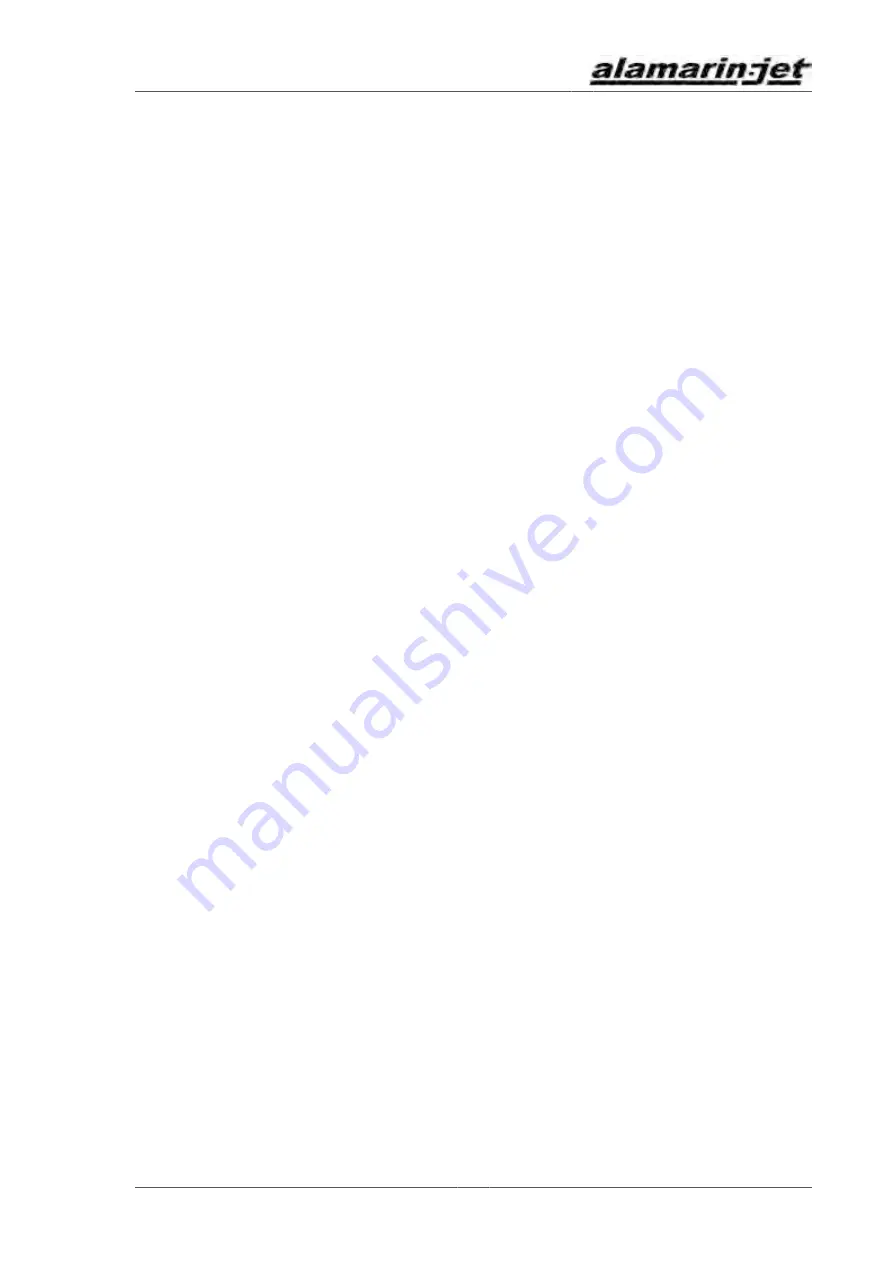
Oil recommendations
Operation and maintenance manual
KHO/340/EN/1.0.0.
43
Appendix 3. Oil recommendations
The operating hydraulic system of the reversing deflector and the lubrication
of the front bearing are designed to use oil that is specifically intended
for automatic transmission systems. The oil must meet the following
requirements:
Kinematic viscosity 40℃
33-36 mm
2
/s
Kinematic viscosity 100°C
7.1-7.7 mm
2
/s
Viscosity index
min. 170
Density 15°C
0.835–0.890 g/cm
3
Pour point
max. -42 ℃
Flashpoint
min. 180 ℃
Recommended oil brands:
• Mobil ATF 320
• FormulaShell ATF DEXRON III
• Neste ATF-X
• BP Autran DX III
Summary of Contents for AJ 340
Page 1: ...Operation and maintenance manual ...
Page 2: ......
Page 4: ......
Page 10: ...The jet propulsion unit Operation and maintenance manual 6 KHO 340 EN 1 0 0 ...
Page 18: ...Operation Operation and maintenance manual 14 KHO 340 EN 1 0 0 ...
Page 38: ...Maintenance Operation and maintenance manual 34 KHO 340 EN 1 0 0 ...
Page 44: ...Problem situations Operation and maintenance manual 40 KHO 340 EN 1 0 0 ...