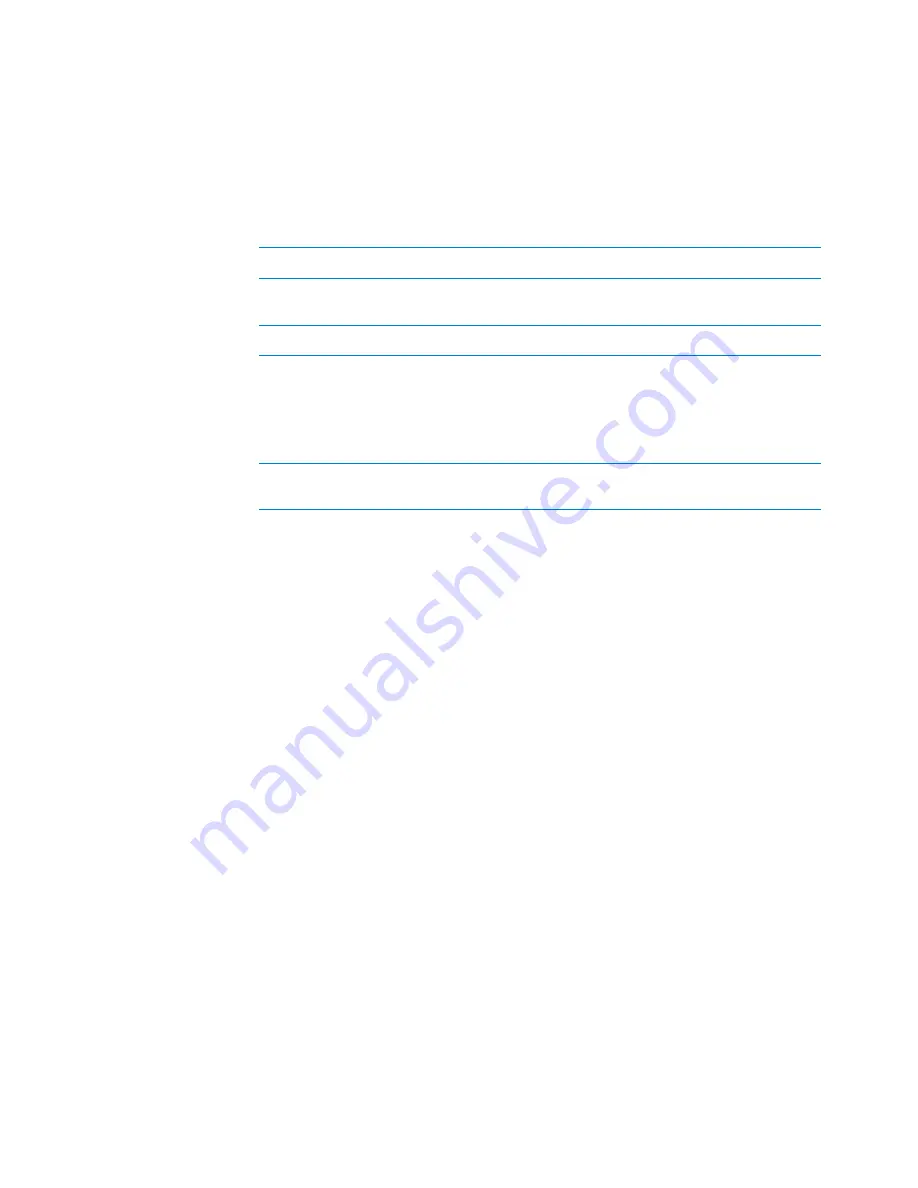
Preface
About this guide
vi
BenchBot Robot Safety and Installation Guide
About this guide
Who should read this guide
This guide is for people with the following job roles:
Installers, integrators, lab managers, and administrators are users who must
have technical expertise. In addition, lab managers and administrators are
individuals or groups responsible for the use and maintenance of the BenchBot
Robot and for ensuring that operators are adequately trained.
What this guide covers
This guide describes the following:
•
Potential safety hazards of the BenchBot Robot and how to avoid them.
•
Specifications and site requirements for the BenchBot Robot. Use this
information to plan the space for the BenchBot Robot. Make sure your site
meets the requirements outlined in this guide before installing the robot.
•
Installation instructions for the robot and, if applicable, the BenchBot
integration plates.
Job role
Responsibilities
Installer
Unpacks, installs, and tests the Agilent BenchBot Robot
before it is used.
Integrator
Configures hardware and writes software.
Lab manager,
administrator,
or technician
•
Manages the automation system that contains the
BenchBot Robot
•
Develops the applications that are run on the system
•
Develops training materials and standard operating
procedures for operators
Operator
Performs the daily production work on the system that
contains the BenchBot Robot and solves routine problems.
Summary of Contents for BenchBot
Page 1: ...BenchBot Robot Safety and Installation Guide Original Instructions...
Page 4: ...Contents iv BenchBot Robot Safety and Installation Guide...
Page 10: ...Preface Reporting problems x BenchBot Robot Safety and Installation Guide...
Page 71: ......
Page 72: ...Safety and Installation Guide G5486 90001 Revision 01 June 2011...