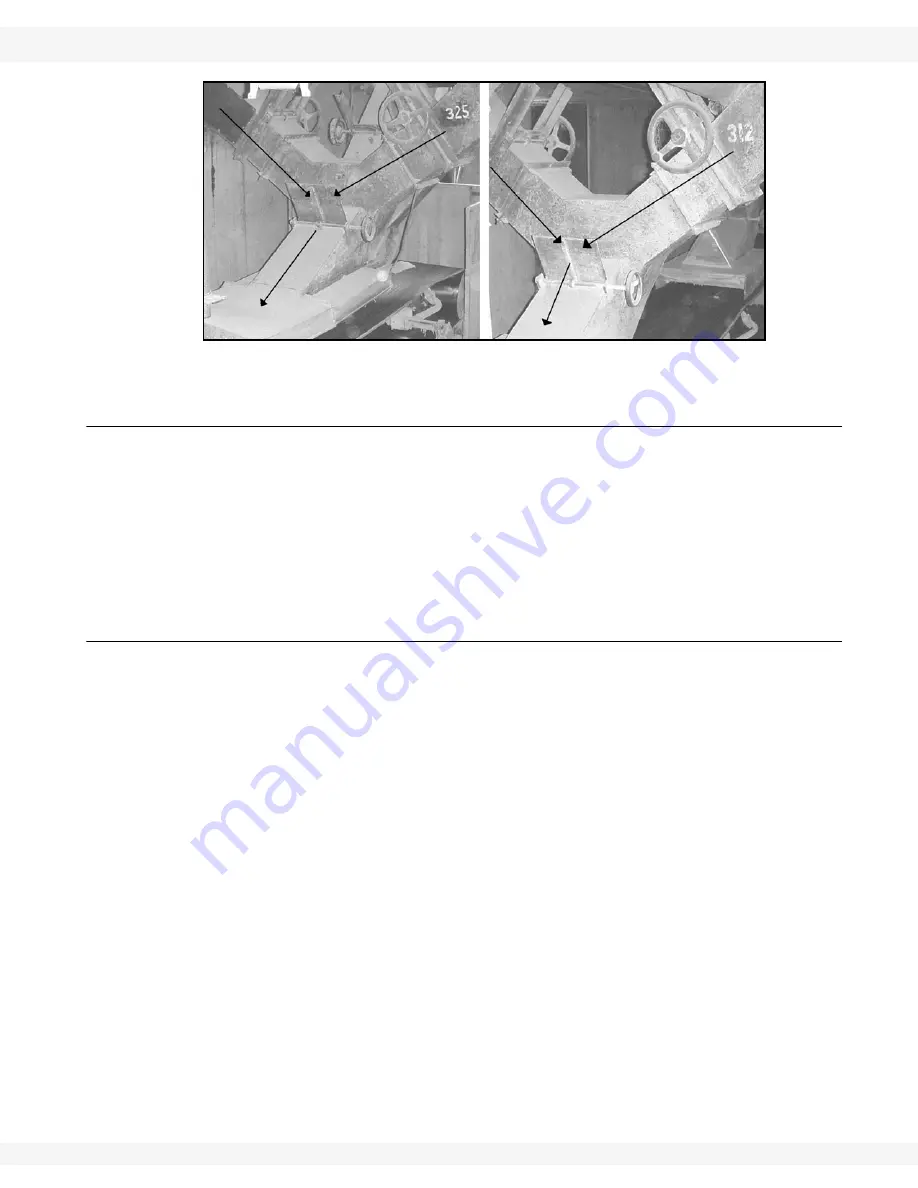
H
I
R
OLLER
- B
ELT
C
ONVEYORS
4. A
PPLICATION
D
ESIGN
C
ONSIDERATIONS
H
I
R
OLLER
, M
INI
R
OLLER
, L
O
R
OLLER
& H
I
L
IFE
4.6. L
OADING
C
ONSIDERATIONS
P115506 R3
31
Figure 4.4
4.6.1. S
PECIAL
L
OADING
A
PPLICATIONS
When overhead clearance does not permit the loader housing to fit, it may be
necessary to cut a portion of the housing off. When this is done, the material will
fall directly onto to the belt without being deflected by the loader backplate.
A deflecting baffle or backplate should be placed in the loader to keep the
material from rolling backward and spilling on the belt. Hi Roller's engineering
department must be consulted for a properly designed and installed special
loader.
4.6.2. L
OADING
G
OALS
1. Material must flow evenly onto the belt at the speed and in the same direction
of the belt.
2. Control gate and spouting must be installed so that the material flows down
the backplate of the loaders as shown in Figure 4.5 and 4.6.
3. Control gates must be installed to open from the back (tail end) of the loader
to the front (head end) so the material flows down the backplate. This must
be done for proper loading.
4. Material speed is very important for proper loading. Material flowing too fast
will cause the material to splash as it hits the belt, then causing boiling
leading to loading problems. Material dropping from more than 3’ - 4’ must be
slowed down with a control gate, dead box, or another type of material
slowing device.
5. The material must be evenly spread across the full width of the backplate of
the loader.
6. Spouting from the side will cause material flow problems in the loader. A
control gate, baffle, or other means to turn the material flow must be included
in the design of the loader.
7. Bi-directional loading is feasible with a properly designed loader. Contact Hi
Roller's engineering department for assistance with this design.