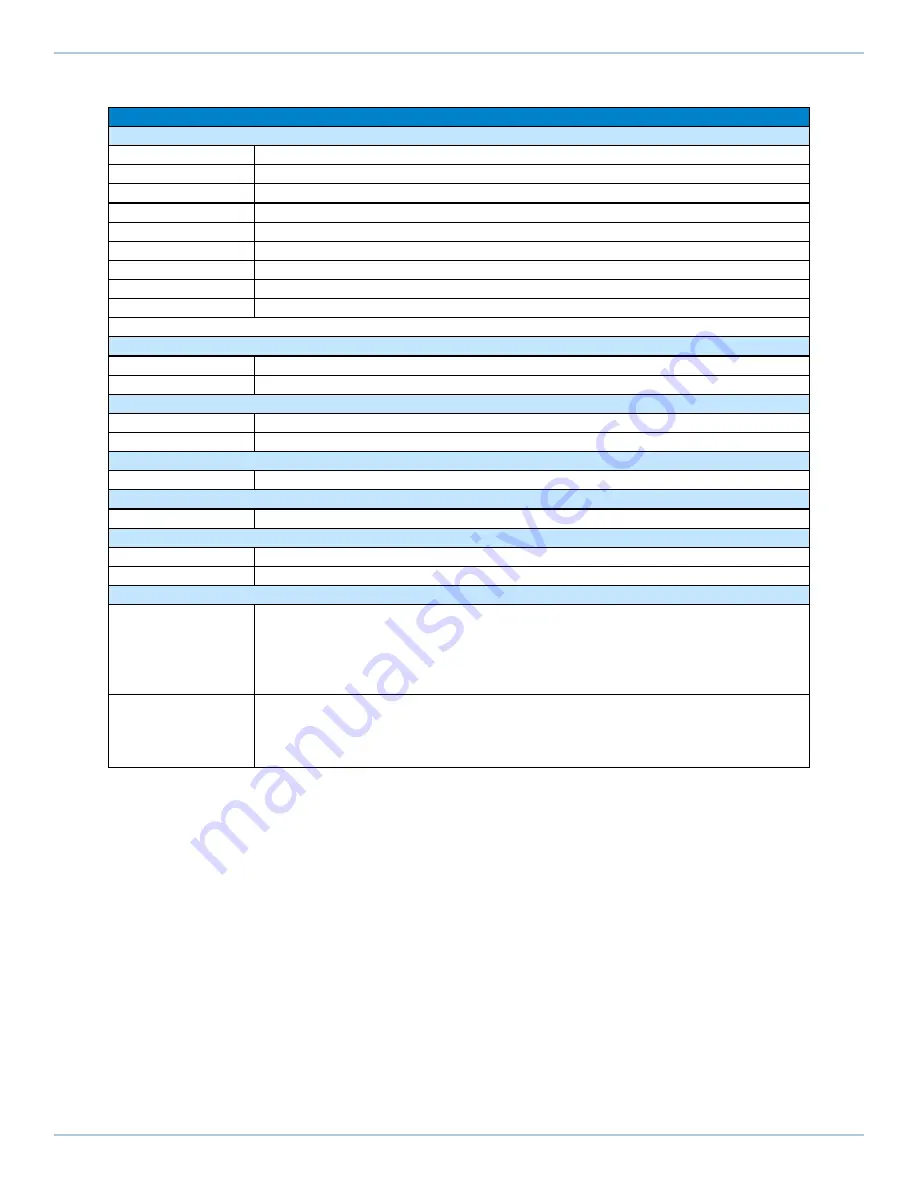
Table 1-1:
Ordering Options
AGV3D Series High Performance Galvanometer Scanner
Wavelength (Required)
-W001
10.6 µm
-W003
1552 nm
-W004
1064 nm
-W005
1030 nm
-W006
532 nm
-W007
515 nm
-W008
355 nm
-W009
343 nm
-W012
9.3 µm
NOTE: Custom wavelengths are available. Contact the factory for details.
Scanner Aperture (Required)
-20
20 mm Scanner Aperture
-30
30 mm Scanner Aperture
Field Configuration (Required)
-F1
Near Field of View
-F2
Far Field of View
Air Cooling (Optional, refer to
)
-AC
Air cooling
Water Cooling (Optional, refer to
-WC
Water cooling
Plate (Optional)
-MP1
Rear Mounting Plate
-MP2
Bottom Mounting Plate
Integration (Required)
-TAS
Integration - Test as system
Testing, integration, and documentation of a group of components as a complete
system that will be used together (ex: drive, controller, and stage). This includes
parameter file generation, system tuning, and documentation of the system
configuration.
-TAC
Integration - Test as components
Testing and integration of individual items as discrete components that ship together.
This is typically used for spare parts, replacement parts, or items that will not be used
together. These components may or may not be part of a larger system.
AGV3D Hardware Manual
Chapter 1: Overview
www.aerotech.com
17
Summary of Contents for AGV3D Series
Page 1: ...Revision 2 00 AGV3D Three Axis Laser Scan Head HARDWARE MANUAL...
Page 6: ...This page intentionally left blank List of Tables AGV3D Hardware Manual 6 www aerotech com...
Page 12: ...This page intentionally left blank Laser Shutter AGV3D Hardware Manual 12 www aerotech com...
Page 16: ...Figure 1 2 Standard AGV3D Chapter 1 Overview AGV3D Hardware Manual 16 www aerotech com...