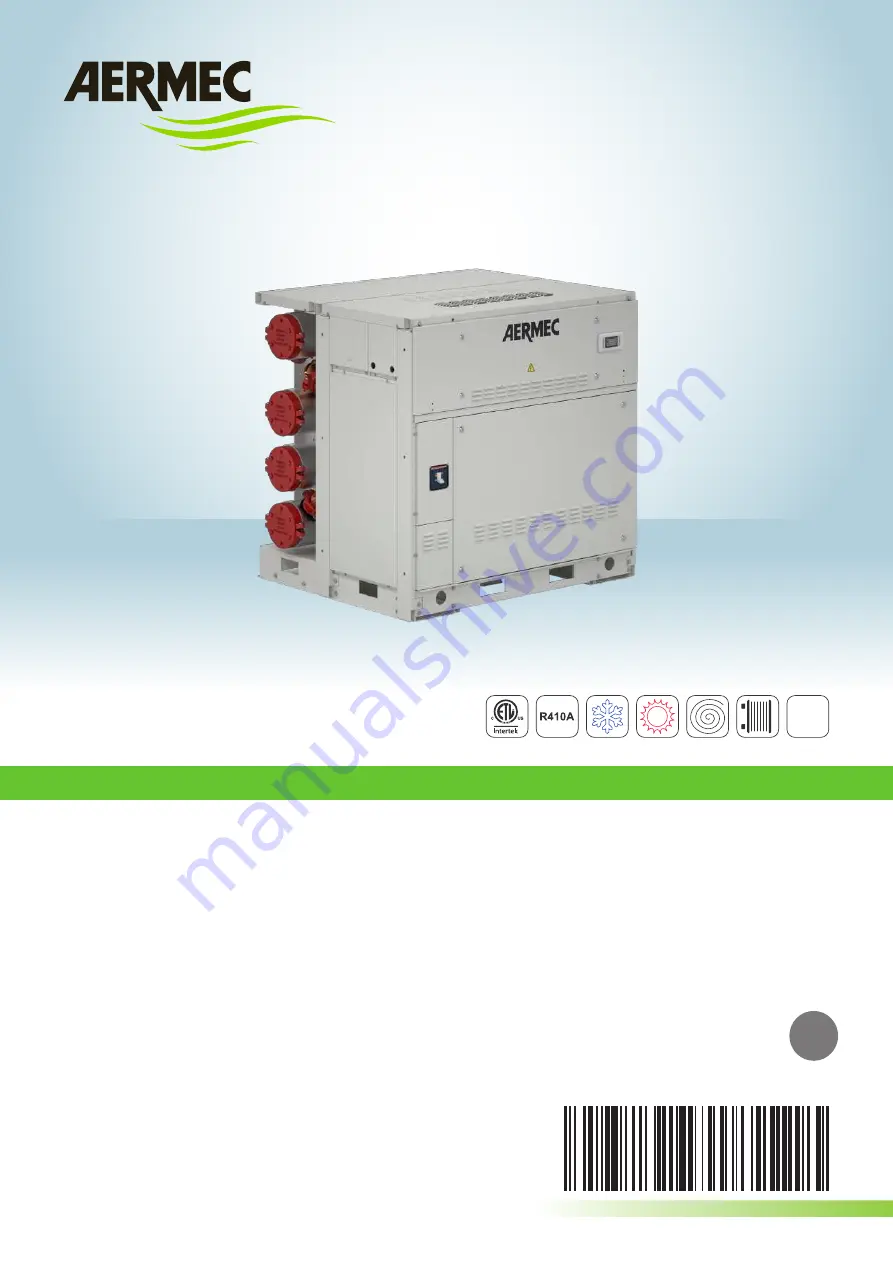
BARCODE
EN
Installation and Maintenance Manual
TRANSLATION FROM ORIGINAL
60Hz
20.10 5046100_08
•
DUAL CIRCUIT
•
COMPACT MODULE
•
RELIABLE AND MODULAR
•
MAX 2 LEVELS OF STACKABLE UNITS
•
EASY AND QUICK TO INSTALL
•
UP TO 36 CONNECTABLE UNITS*
* See the modularity options.
WWM
HEAT PUMP WITH REVERSIBLE WATER SIDE