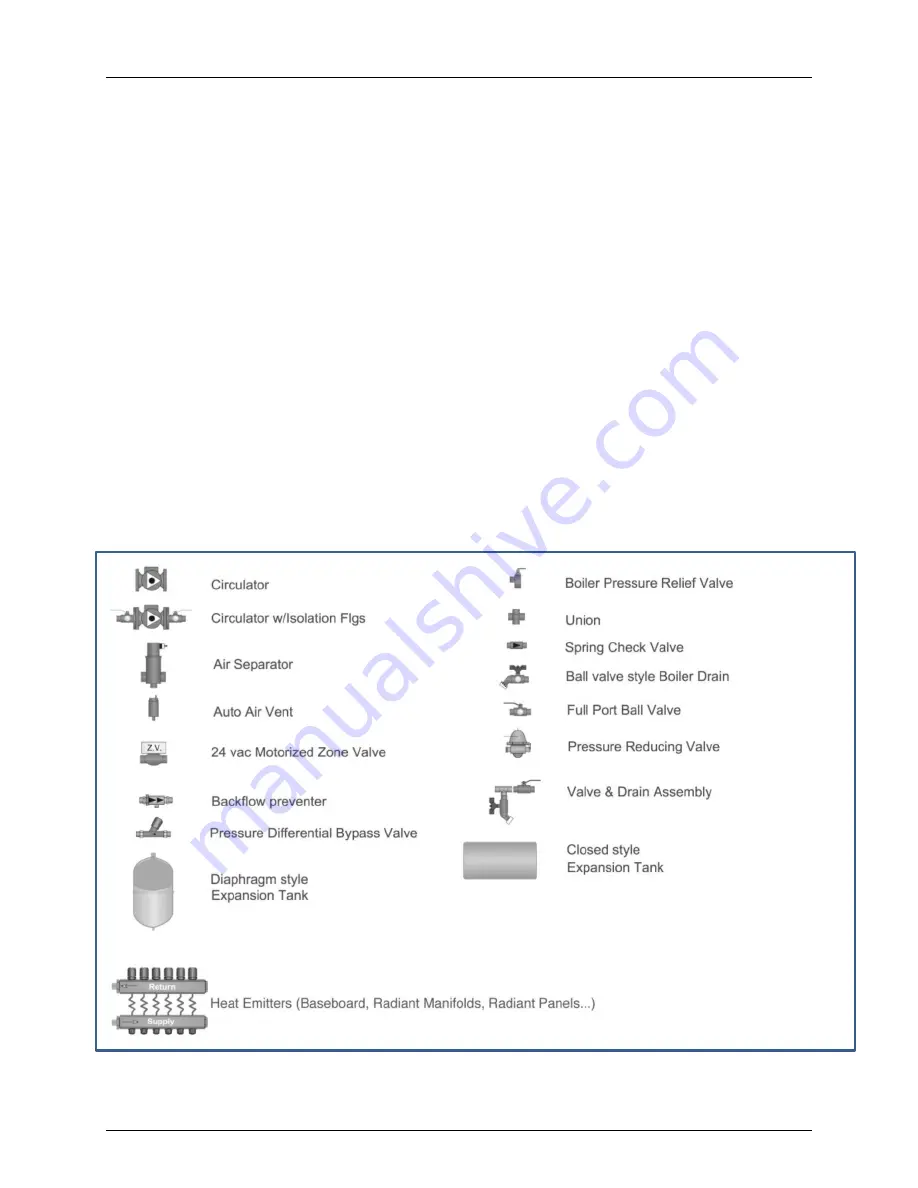
GF-135
Esteem 399 Low NOx Boiler
Chapter 5
OMM-0089_0A
Installation, Operation & Maintenance Manual
Boiler Piping
Page
36
of
188
AERCO International, Inc.
•
100 Oritani Dr.
•
Blauvelt, NY 10913
OMM-0089_0A
MC1 06/19/14
Ph.: 800-526-0288
5.16 SYSTEM PIPING—SPECIAL APPLICATIONS
If the boiler is used in conjunction with a chilled water/medium system, the boiler and chiller
must be piped in parallel. Install flow/check valves to prevent the chilled medium from entering
into the boiler.
If the boiler is used to supply hot water to the heating coils of an air handler where they may
be exposed to chilled air circulation, install flow/check valves or other automatic means to
prevent gravity circulation of the boiler water during cooling cycles.
5.17 SYSTEM PIPING—MULTIPLE UNITS INSTALLATION
Use a balanced manifold system as the primary / secondary connection to the space heating
piping as shown in Figure 5-9
.
Maintain a minimum of 6 inches [153 mm] of clearance between units to allow for servicing.
Refer to Figure 5-3 and Figure 5-4
to install air separator and expansion tank.
For the space heating piping refer to the applications mentioned in this manual or use
recognized design methods.
NOTE
The boiler system piping shown must be a “closed” system to
avoid any contamination and potential failure of any components
in the system.
Figure 5-2: Piping Diagram Component Legend