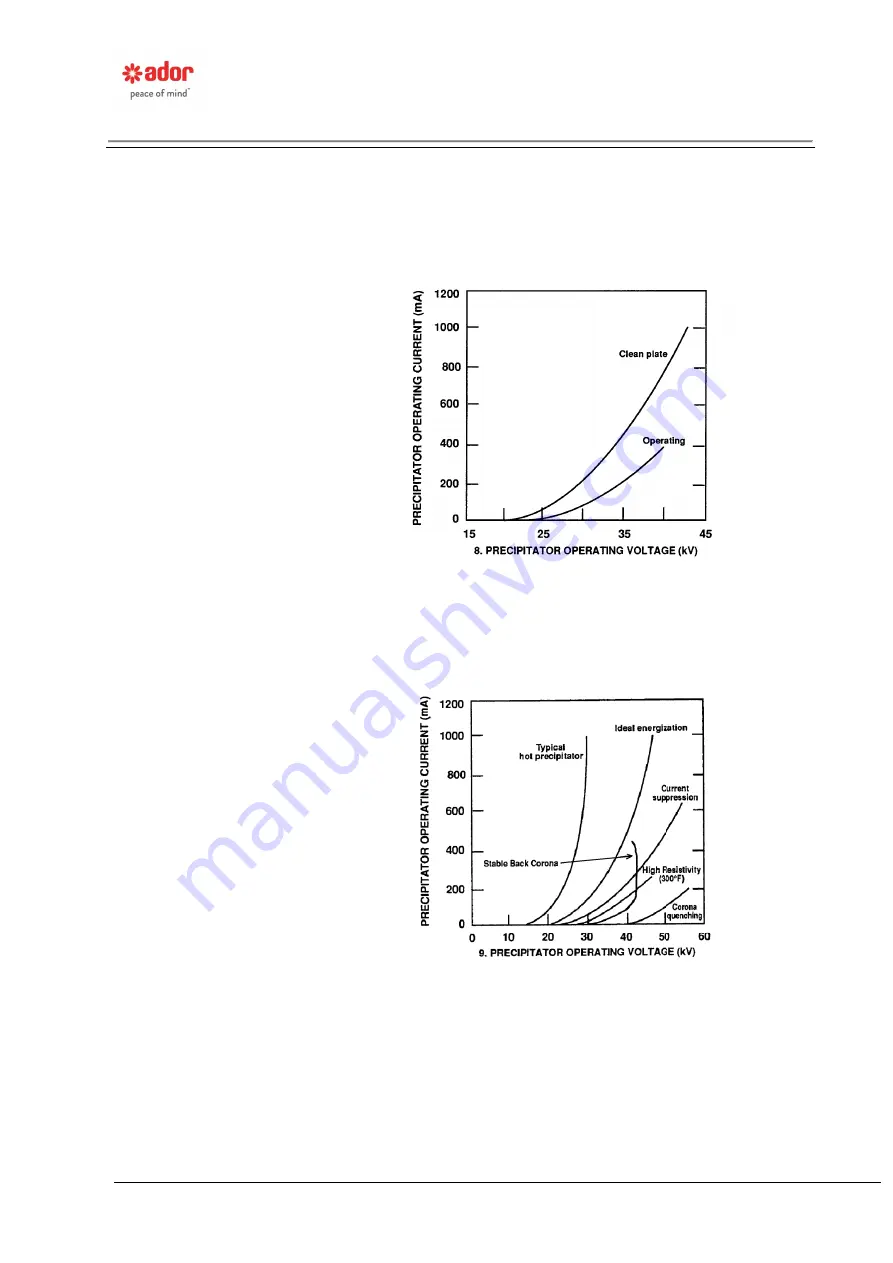
RK3000 High Frequency Power Supply
Operating Manual
Page 57 of 73
Waveforms #8 and #9, Back Corona Control
Waveform #8 shows a typical secondary voltage versus secondary current curve for
moderate and low resistivity precipitator operation.
Sketch 8: Precipitator Operating Voltage (kV)
Waveform #9 shows a typical secondary voltage versus secondary current curve for high-
resistivity precipitator operation where the precipitator is experiencing Back Corona.
Sketch 9: Precipitator Operating Voltage (kV)
Notice that with Back Corona, the current increases without a corresponding increase in
voltage. The point where the current starts to increase but the voltage remains the same
(or even decreased) is the optimum operating point for Back Corona operation.
Operating at higher current provides no increase in precipitator efficiency and only results
in wasted power (and, in most cases, poorer collection efficiency).