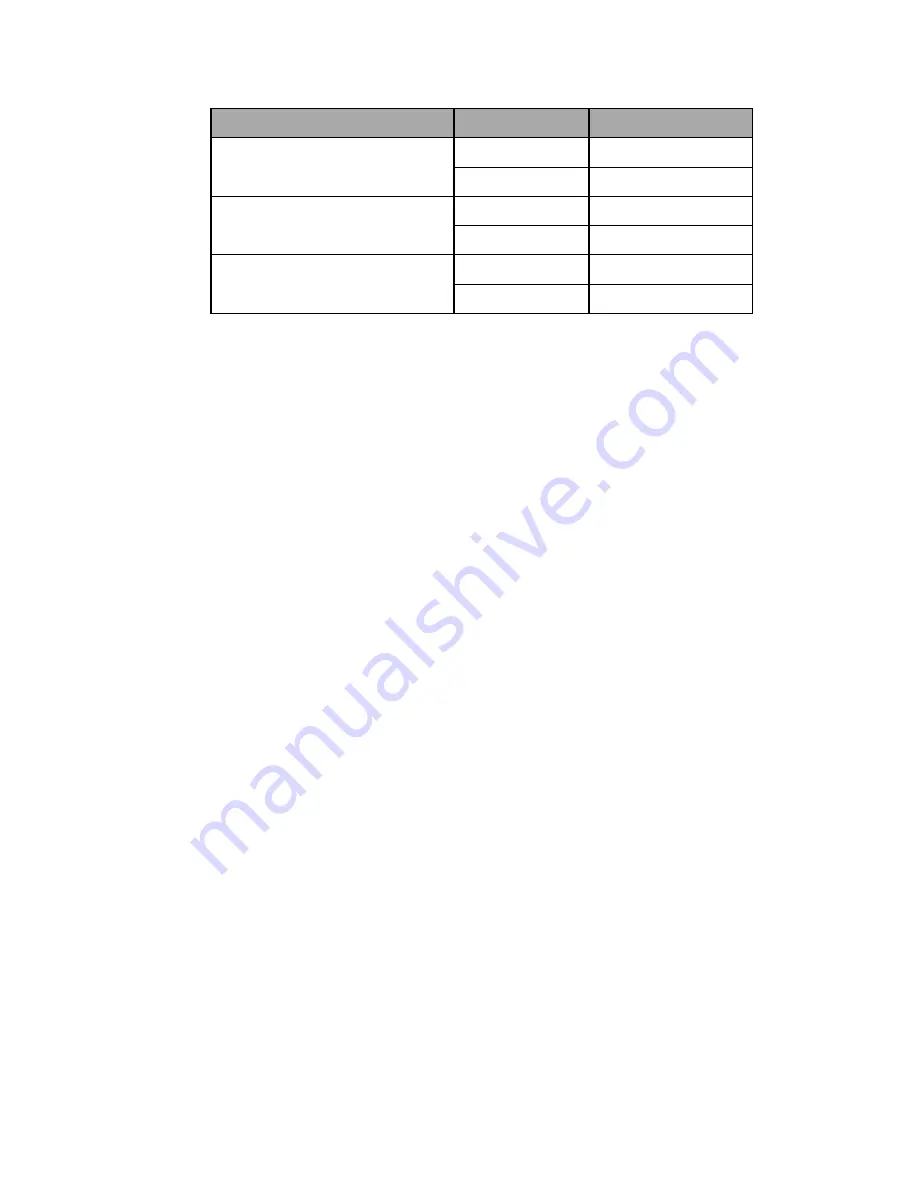
Chapter 3: MotionBlox-60R
Adept Viper s650/s850 Robot with MB-60R/eMB-60R User’s Guide, Rev F
Page 40 of 100
Type
Signal Range
IO Blox 2
Inputs
1121 - 1128
Outputs
0113 - 0120
IO Blox 3
Inputs
1129 - 1136
Outputs
0121 - 0128
IO Blox 4
Inputs
1137 - 1144
Outputs
0129 - 0136
3.5 Using Digital I/O on MB-60R/eMB-60R XIO Connector
The XIO connector on the MB-60R/eMB-60R interface panel offers access to digital I/O, 12
inputs and 8 outputs. These signals can be used by V+/eV+ to perform various functions in the
workcell. See the following table for the XIO signal designations.
l
12 Inputs, signals 1097 to 1108
l
8 Outputs, signals 0097 to 0104
Summary of Contents for eMB-60R
Page 1: ...Adept Viper s650 s850 Robot with MB 60R eMB 60R User s Guide...
Page 2: ......
Page 62: ......
Page 70: ......
Page 82: ......
Page 92: ......
Page 98: ......
Page 99: ......
Page 100: ...P N 05173 060 Rev F 5960 Inglewood Drive Pleasanton CA 94588 925 245 3400...