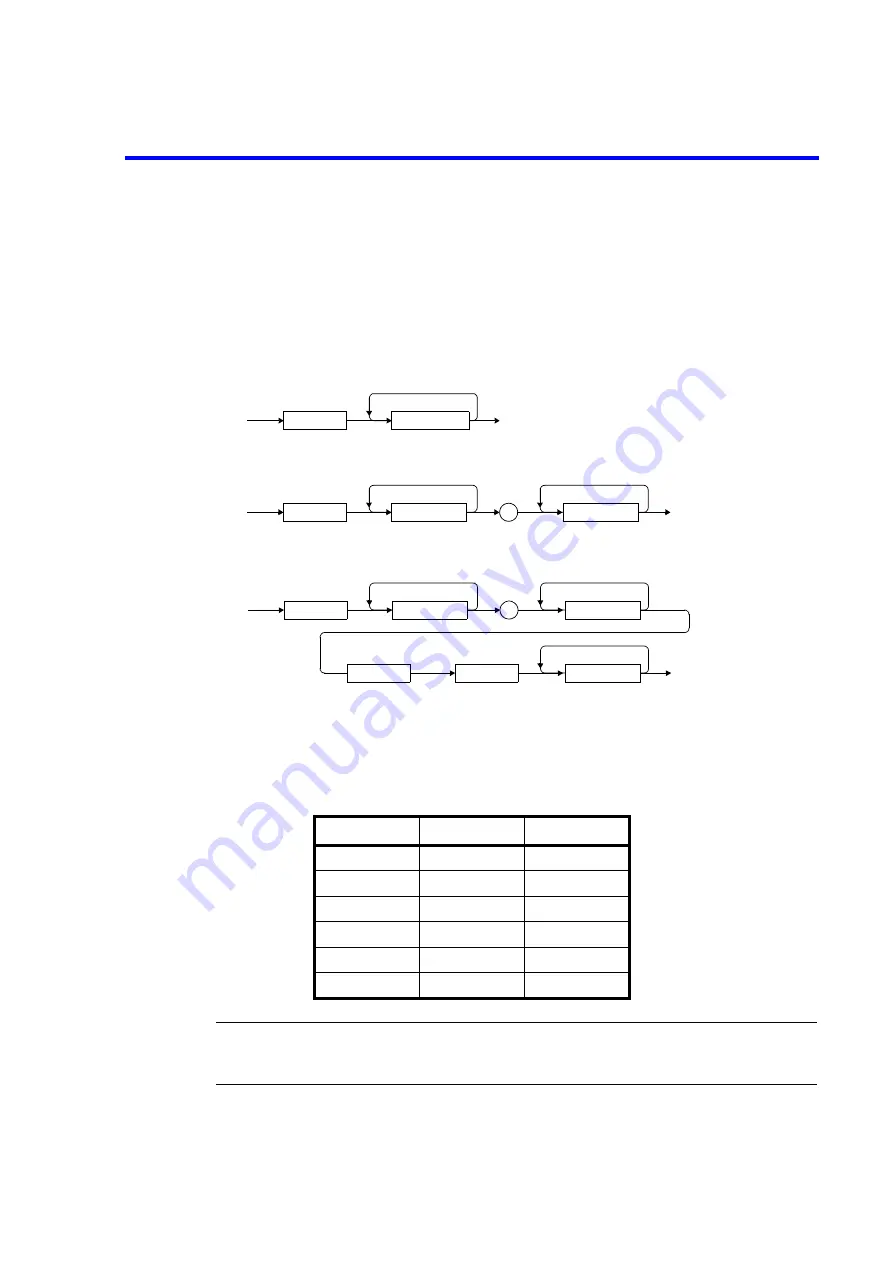
6240B DC Voltage Current Source/Monitor Operation Manual
6.7.2 Data Format
6-23
6.7.2
Data Format
The 6240B uses the following data types for data input and output.
1. Numeric data
There are three numeric data formats, any of which can be used for input.
Some commands can add units to the data when the data is input.
•
Integer type: NR1 format
•
Fixed-point type: NR2 format
•
Floating-point type: NR3 format
2. Units
The table below lists the units that can be used for the D command.
NOTE:
When numeric data is expressed in an exponent format in the 6240B, the number conversion time
becomes too long if the exponent is set to ±31 or higher (xx.xxxE±31). The exponent setting should
not exceed ±30.
Unit
Exponent
Meaning
V
10
0
Voltage
MV
10
-3
Voltage
UV
10
-6
Voltage
A
10
0
Current
MA
10
-3
Current
UA
10
-6
Current
[Sign]
Numeric
[Sign]
Numeric
.
Numeric
[Sign]
.
E/e
[Sign]
Numeric
Numeric
Numeric